Emerson Process Management ControlWave XFC User Manual
Page 61
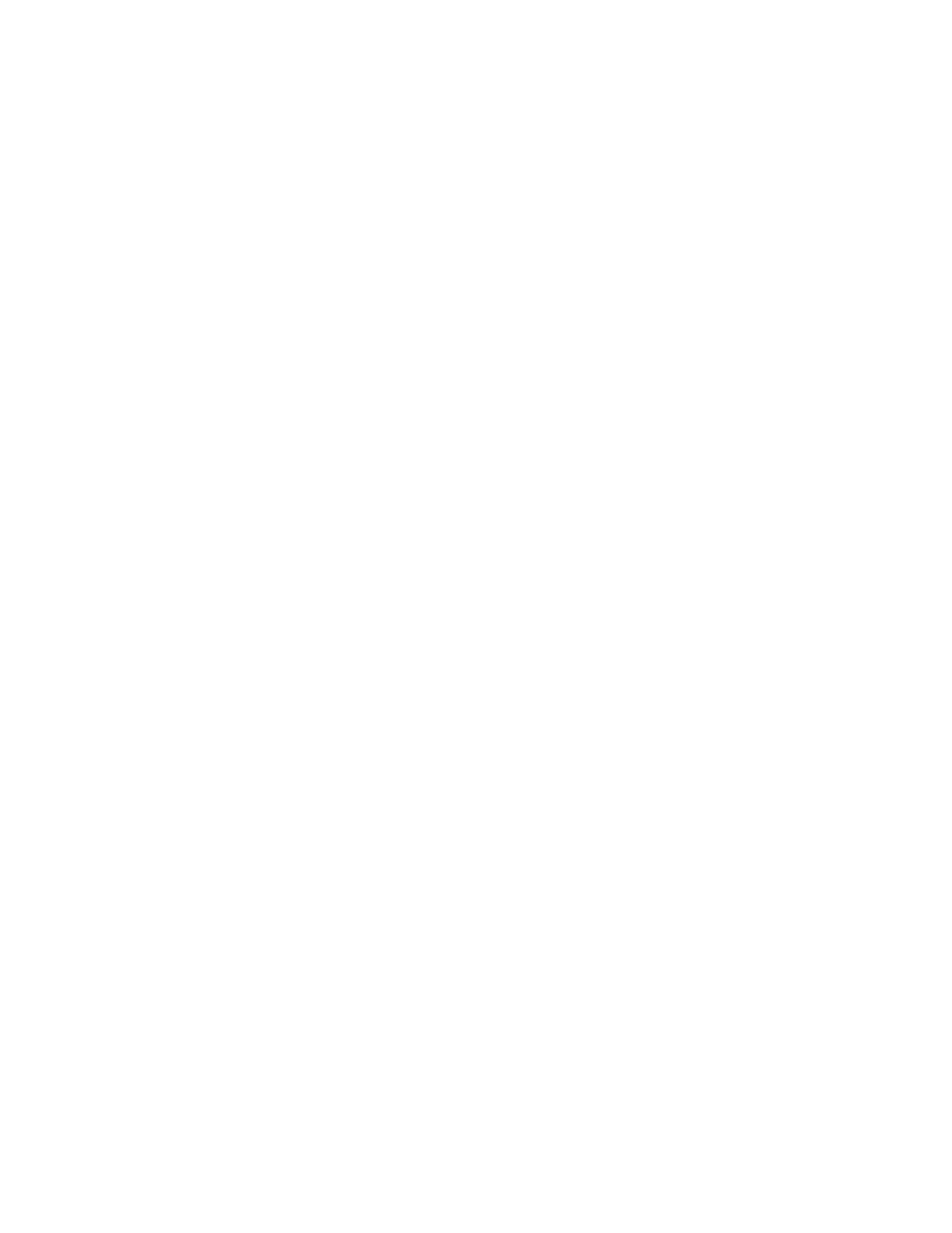
CI-ControlWave XFC
Installation & Operation / 2-19
by inserting the wire’s bared end (1/4” max) into the clamp beneath the screw and securing
the screw. The wire should be inserted fully so that no bare wires are exposed to cause
shorts. If using standard wire, tin the bare end with solder to prevent flattening and
improve conductivity.
Allow some slack in the wires when making terminal connections. The slack makes the
connections more manageable and minimizes mechanical strain on the terminal blocks.
For safety reasons and to prevent accidental damage to a user supplied external bulk DC
Power Supply, it is recommended that the pluggable Power Terminal Block J6 on the
Terminal Plate Assembly be disconnected until the entire unit has been wired, and
hardware configured. Sections 2.3.6.1 & 2.3.6.2 provide details on DC Power Connector
wiring.
2.3.3.2 Shielding and Grounding
The use of twisted-pair, shielded and insulated cable for I/O signal wiring will minimize
signal errors caused by electromagnetic interference (EMI), radio frequency interference
(RFI) and transients. When using shielded cable, all shields should only be grounded at one
point in the appropriate system. This is necessary to prevent circulating ground current
loops that can cause signal errors.
2.3.3.3 Non-isolated Discrete Input/Output Connector Block J5
(see Figure 2-10)
ControlWave XFCs contain field interface circuitry for up to 2 Discrete (Digital) Inputs
and 4 Discrete (Digital) Outputs. Surge Suppression and signal conditioning is provided for
each DI. DO circuits consist of an open drain MOSFETs and Surge Suppression. DI/O
circuitry utilizes a 12-point Terminal Block Assembly (J5) that is located on the Terminal
Plate.
DI/O circuitry provides internally sourced DI operation for Dry Contacts pulled internally
to 3.6Vdc when the field input is open. Each DI is protected with a surge suppressor. DI
filtering is 15 milliseconds. DO circuitry utilizes open drain MOSFETs and surge sup-
pressors. The DOs sink current to digital ground.
2.3.3.3.1 Discrete Input/Output Configurations
Terminal Plate Terminal Block J5 supports two non-configurable DIs and 4 non-
configurable externally powered DOs. Each DI provides either a 60uA source current from
3.6Vdc. Open drain MOSFETs associated with each DO provide up to 400mA each @ 30Vdc
to an externally powered device. Field wiring assignments are provided in Figure 2-10.
2.3.3.4 Non-isolated Analog Input Connector Block J4 (see Figure 2-10)
ControlWave XFCs contain field interface circuitry for up to three (3) Analog Inputs (1 to
5V operation). Field power source can be from the ControlWave XFC’s V+ supply [where
V+ ≈ Input Power - .6Vdc (and doesn’t exceed 15Vdc)], or an external 11 to 30Vdc power
source.
Each AI signal is channeled through signal conditioning circuitry (that provides a 2 Hertz
low pass filter), a transorb for surge suppression, multiplexer, and an A to D Converter
(ADC).