Emerson Process Management ControlWave XFC User Manual
Page 32
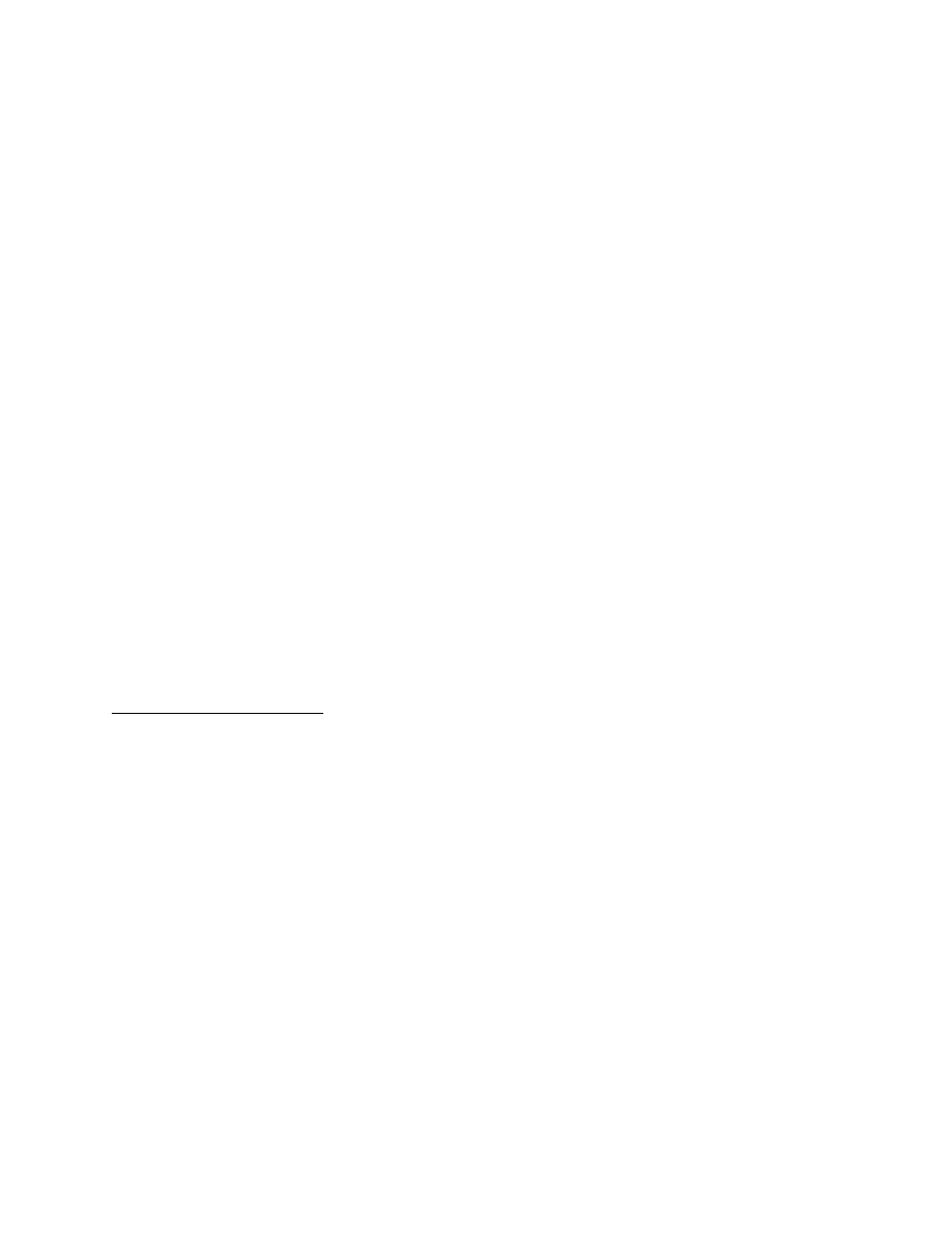
1-18 / Introduction
CI-ControlWave XFC
separately to prevent recurring alarms from overwriting configuration audit data.
Externally, they are reported to the user as a single entity. Both operate in a circular
fashion with new entries overwriting the oldest entry when the buffer is full.
The following circumstances cause an entry to be made in the Audit Trail Buffer:
• Any operator change to a ControlWave XFC configuration variable
• Any change in the state of a ControlWave XFC alarm signal
• A system restart
• Certain other system events
1.5.4 LCD Display
In normal operation, the display stays on after the unit is configured and placed in service.
ControlWave XFC Display Assembly contains an upper row consisting of a
± LCD character
and nine 7-Segment LCD characters, and a bottom row consisting of six 14-Segment LCD
characters. Signal values controlled by the “application load,” are posted to the upper
characters and signal names are posted to the lower characters. Signal names may include
units up to 20 characters in length which scroll across the bottom row.
1.5.5 Communications
A ControlWave XFC can be configured as a Master or Slave node on either a MODBUS
network or a BSAP network. Up to three serial communication ports are contained on the
ControlWave XFC I/O Board assembly and are user accessible via the Terminal Plate.
Communication ports are designated as follows:
Communication Ports COM1, COM2 & COM3 support serial asynchronous operation. Any
serial communication port can be configured for local communications, i.e., connected to a
PC loaded with ControlWave Designer and OpenBSI software.
Term. Plate Connector J2:
COM1 - (Referred to as the Local Port) - 3-Pin - RS-232) (Half Duplex Oeration)
COM2 - (Referred to as the Network Port) - 7-Pin - RS-232) (Full/Half Duplex Oeration)
COM3 - 3-Pin - RS-485 (Half Duplex Operation)
RS-232 Ports
An RS-232 interface supports Point to Point, half-duplex (COM1/2) and full-duplex (COM2)
communications (20 feet maximum, using data quality cable). Half-duplex communications
supported by the ControlWave XFC utilize MODBUS or BSAP protocol, while full-duplex
is supported by the Point to Point (PPP) protocol. ControlWave XFC RS-232 port COM2
utilizes the “null modem” cable (Figure 2-9A) to interconnect with other devices such as a
PC, printer, another ControlWave XFC/GFC, ControlWave MICRO, ControlWave
EFM, or Control-Wave unit, a ControlWave I/O Expansion Rack or a ControlWaveLP
unit when the ControlWave XFC is communicating using the full-duplex PPP protocol.
RS-485 Ports
ControlWave XFC can use an RS-485 communication port for network communications to
multiple nodes. Essentially, the master and the first slave transmit and receive data on
opposite lines; all slaves (from the first to the "nth") are paralleled (daisy chained) across
the same lines. The master node should be wired to one end of the RS-485 cable run. A 24-
gauge paired conductor cable, such as Belden 9843 should be used. No termination resistors
are required; operating at 19,200 baud, a 4000’ network is supported. For user