Emerson Process Management ControlWave XFC User Manual
Page 60
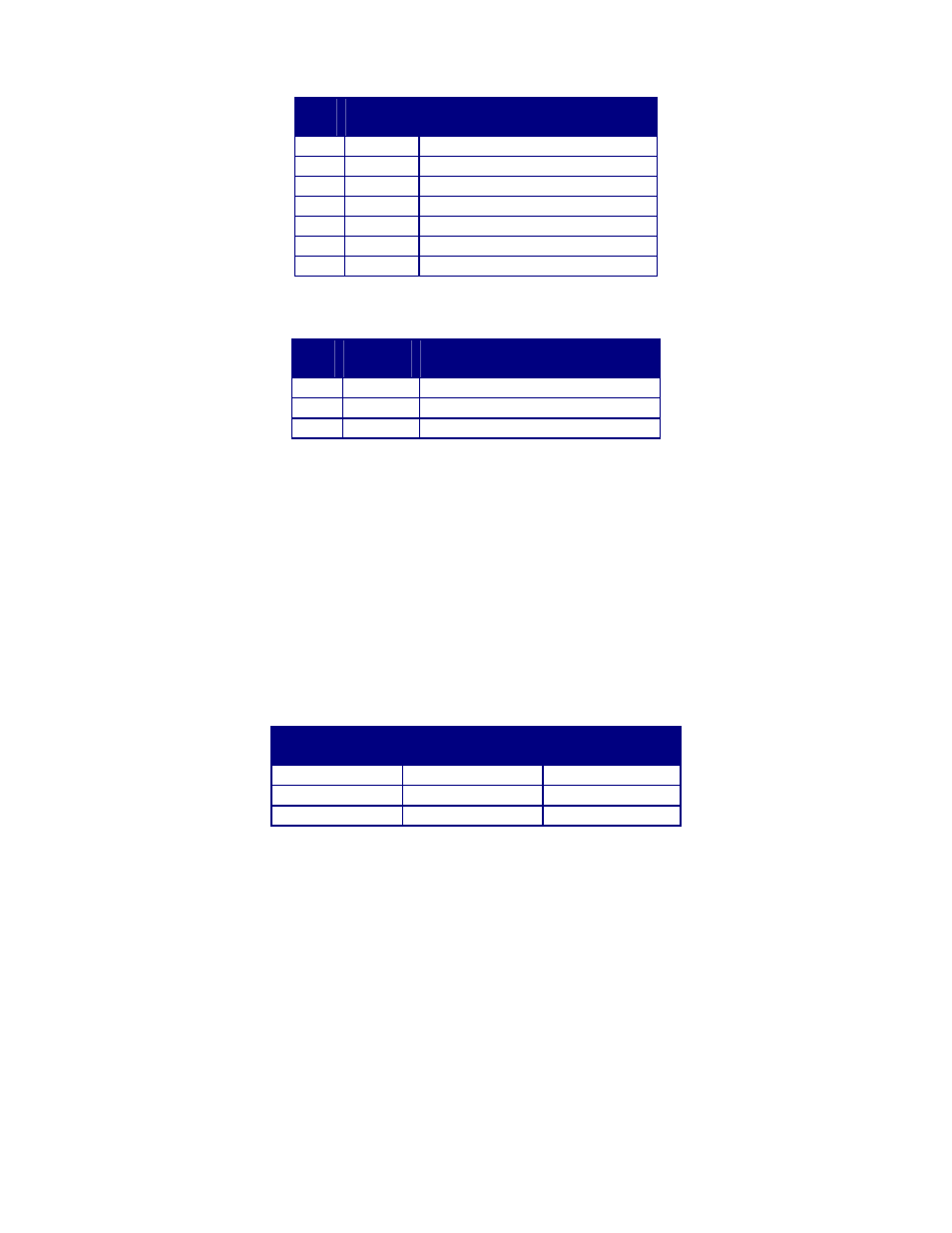
2-18 / Installation & Operation
CI-ControlWave XFC
Table 2-2B - RS-232 Ports (COM2) Terminal Plate Connector J2 Pin Assignments
Pin
#
Signal
RS-232
Description:
RS-232 Signals
8
TXD
Transmit Data Output
9
RXD
Receive Data Input
10
RTS
Request To Send Output
11
CTS
Clear To Send Input
12
DTR
Data Terminal Ready Output
13
DCD
Data Carrier Detect Input
14 GND Power
Ground
Table 2-2C - RS-485 Port (COM3) Terminal Plate Connector J2 Pin Assignments
Pin
#
Signal
RS-485
Description:
RS-485 Signals
1
GND
Power Ground
2
TR
− Transmit/Receive
Data
−I/O
3
TR+
Transmit/Receive Data + I/O
RS-485 Ports
ControlWave XFC can use an RS-485 communication port for local network com-
munications to multiple nodes up to 4000 feet away. Since this interface is intended for
network communications, Table 2-3 provides the appropriate connections for wiring the
master, 1st slave, and nth slave. The master node should be wired to one end of the RS-485
cable run. A 24-gauge paired conductor cable, such as Belden 9843 should be used. Note:
Only half-duplex RS-485 networks are supported.
Table 2-2C provides connector pin assignments for Comm. Port COM3.
Table 2-3 - RS-485 Network Connections
(see Table 2-2C ControlWave XFC RS-485 Port Pin # Assignments)
From
Master
To 1st
Slave
To nth
Slave
TR+ TR+ TR+
TR
− TR− TR−
GND GND GND
Note: When wiring to four-wire RS-485 Ports connect TR+ to TXD+ & RXD+
and connect TR- to TXD- and RXD-.
Note: Pins 1, 2, 3, 4 & 9 of BBI Series 3305, 3310, 3330, 3335 & 3340 RTU/DPC
RS-485 Comm. Ports are assigned as follows: 1 = TXD+, 2 = TXD-, 3 = RXD+, 4
= RXD- & 9 = ISOGND.
2.3.3 I/O Wiring
ControlWave XFCs are provided with Card Edge Terminal Blocks that accommodate field
wiring. Wiring is routed into the enclosure through a ¾” Conduit Fitting.
2.3.3.1 I/O Wire Connections
ControlWave XFC electronic flow computers utilize Terminal Blocks equipped with
compression-type terminals that accommodate up to #14 AWG wire. A connection is made