Appendix a specifications, Functional design – Rockwell Automation 150 SMC-Flex User Manual User Manual
Page 127
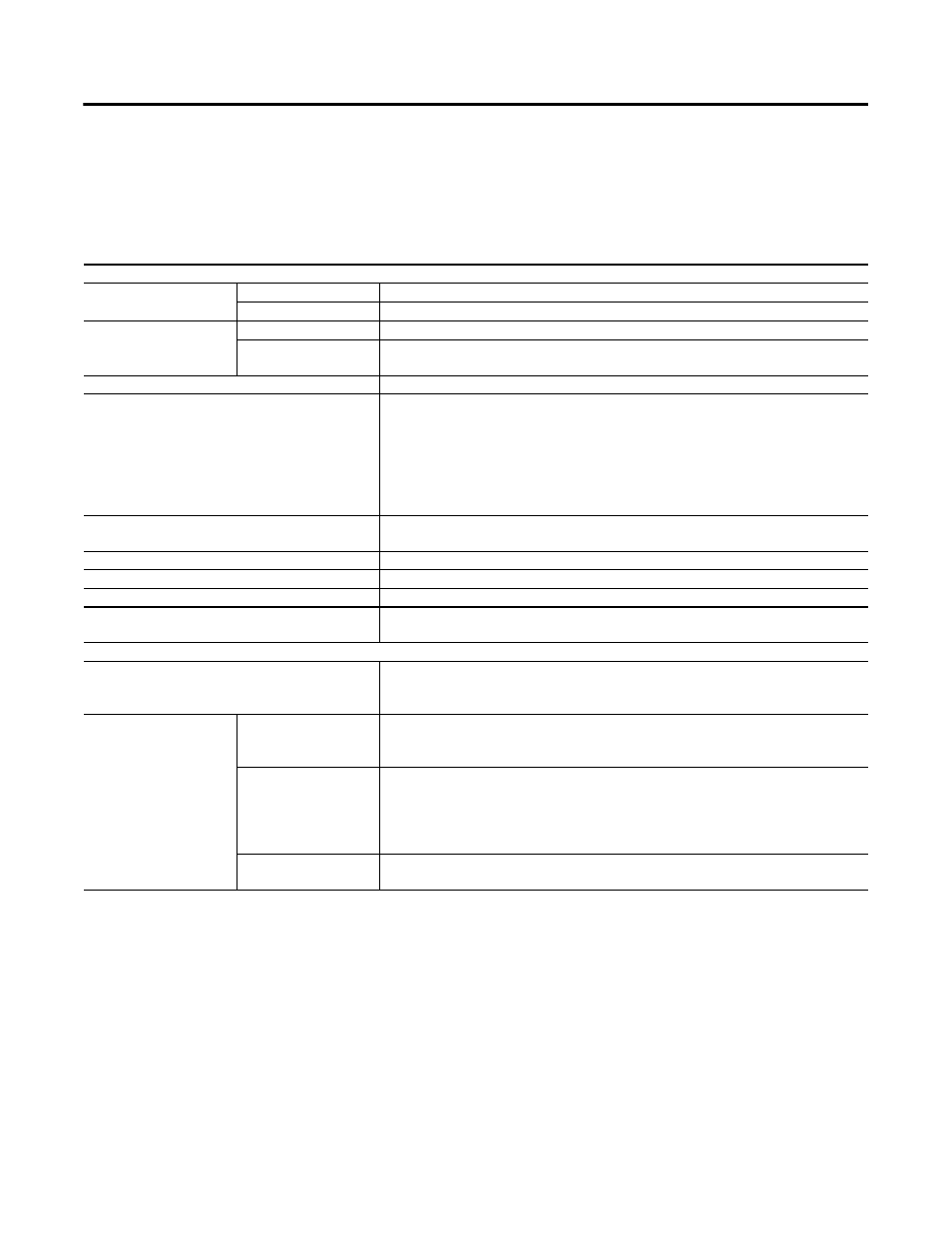
Rockwell Automation Publication 150-UM011A-EN-P - August 2010
Appendix A
Specifications
Functional Design
Standard Features
Installation
Power Wiring
Standard squirrel-cage induction motor or a Wye-Delta, six-lead motor.
Control Wiring
2- and 3-wire control for a wide variety of applications.
Setup
Keypad
Front keypad and backlit LCD display.
Software
Parameter values can be downloaded to the SMC-Flex Controller with DriveTools
programming software and the Cat. No. 20-COMM… DPI communication module.
Communications
One DPI provided for connection to optional human interface and communication modules.
Starting and Stopping Modes
•
Soft Start
•
Current Limit Start
•
Dual Ramp
•
Full Voltage
•
Linear Speed Acceleration
•
Preset Slow Speed
•
Soft Stop
Protection and Diagnostics
Power loss, line fault, voltage unbalance, excessive starts/hour, phase reversal, undervoltage,
overvoltage, controller temp, stall, jam, open gate, overload, underload, communication fault.
Metering
A, V, kW, kWH, MW, MWH elapsed time, power factor, motor thermal capacity usage.
Alarm Contact
Overload, underload, undervoltage, overvoltage, unbalance, jam, stall, and ground fault
Status Indication
Stopped, starting, stopping, at speed, alarm, and fault.
Auxiliary Contacts
Four fully programmable contacts as normal/up-to-speed network (N.O./N.C.) or external
bypass (N.O. only).
Optional Features
Pump Control
Helps reduce fluid surges in centrifugal pumping systems during starting and stopping period.
Starting time is adjustable from 0…30 seconds. Stopping time is adjustable from 0…120
seconds.
Braking Control
SMB Smart Motor Braking
Provides motor braking without additional equipment for applications that require the motor to
stop quickly. Braking current is adjustable from 0…400% of the motor’s full-load current
rating.
Accu-Stop
Provides controlled position stopping. During stopping, braking torque is applied to the motor
until it reaches preset slow speed (7% or 15% of rated speed) and holds the motor at this
speed until a stop command is given. Braking torque is then applied until the motor reaches
zero speed.
Braking current is programmable from 0…450% of full-load current.
Slow Speed with Braking
Used on applications that require slow speed (in the forward direction) for positioning or
alignment and also require braking control to stop.