Rockwell Automation 150 SMC-Flex User Manual User Manual
Page 121
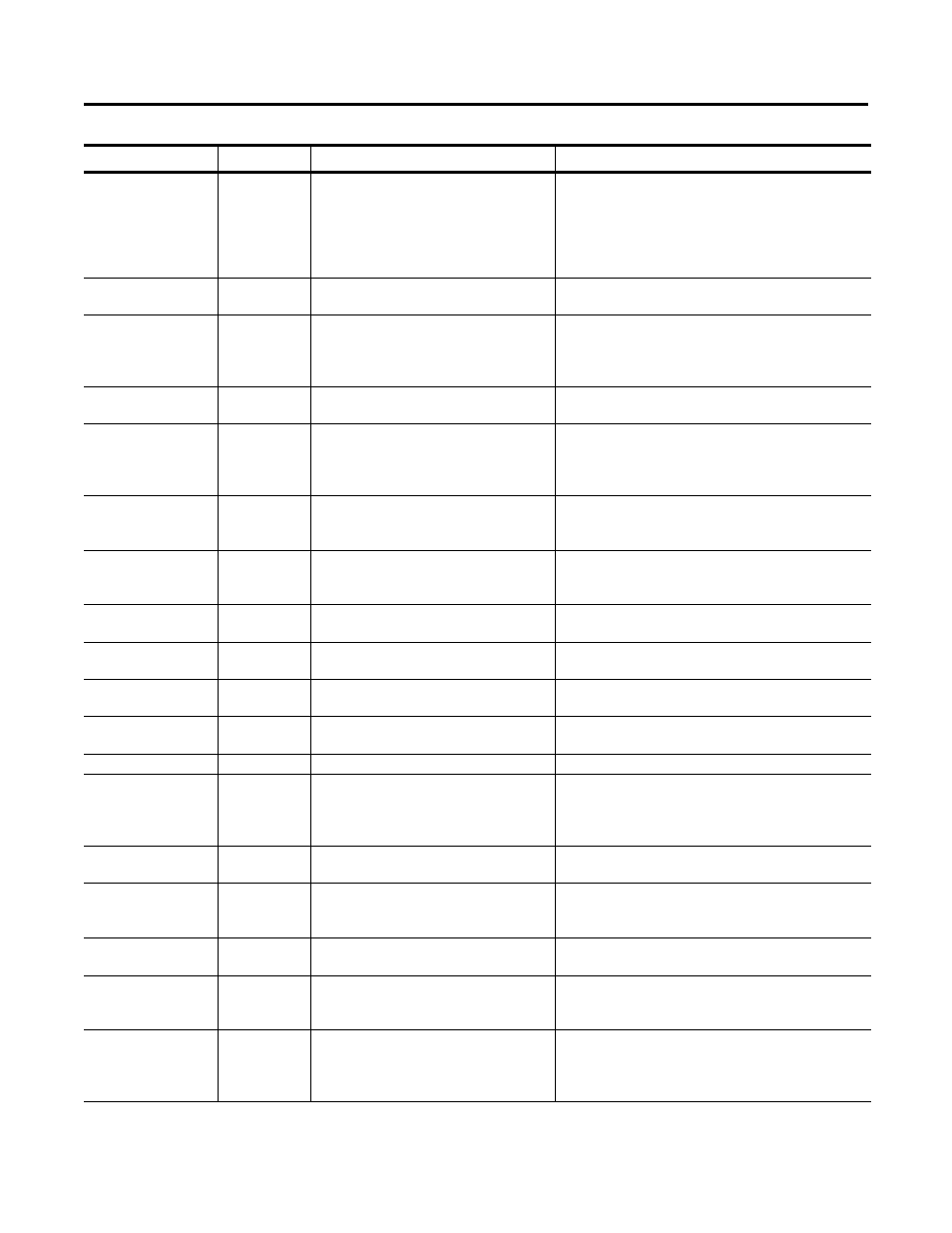
Troubleshooting
9-3
Open Bypass
13, 14, & 15
•
Control voltage is low
•
Inoperable power module bypass
•
Check control voltage power supply
•
Replace power module
•
Check control module TB2…TB4 and TB5…TB7 for
secureness
•
Check Aux 1, 2, 3, 4 configurations are not set to
External Bypass
No Load
16, 17, 18, &
40
•
Loss of load side power wiring
•
Check all load side power connections and motor
windings
Line Unbalance
19
•
Supply unbalance is greater than the
user-programmed value
•
The delay time is too short for the
application
•
Check power system and correct if necessary
•
Extend the delay time to match the application
requirements
Overvoltage
20
•
Supply voltage is greater than user-
programmed value
•
Check power system and correct if necessary
•
Correct the user-programmed value
Undervoltage
21
•
Supply voltage is less than user-
programmed value
•
The delay time is too short for the
application
•
Check power system and correct if necessary
•
Correct the user-programmed value
•
Extend the delay time to match the application
requirements
Overload
22
•
Motor overloaded
•
Overload parameters are not matched
to the motor
•
Check motor overload condition
•
Check programmed values for overload class and
motor FLC
Underload
23
•
Broken motor shaft
•
Broken belts, toolbits, etc.
•
Pump cavitation
•
Repair or replace motor
•
Check machine
•
Check pump system
Jam
24
•
Motor current has exceeded the user
programmed jam level.
•
Correct source of jam
•
Check programmed time value
Stall
25
•
Motor has not reached full speed by
the end of the programmed ramp time
•
Correct source of stall
Phase Reversal
26
•
Incoming supply voltage is not in the
expected ABC sequence
•
Check power wiring
Coms Loss
27, 28, & 29
•
Communication disconnection at the
serial port
•
Check for a communication cable disconnection to
the SMC-Flex controller
Network
30, 31, & 32
•
DPI network loss
•
Reconnect for each DPI connected device
Ground Fault
33
•
Ground fault current level has
exceeded programmed value
•
Check power system and motor; correct if
necessary
•
Check programmed ground fault levels to match
application requirements
Excess Starts/Hr.
34
•
Number of starts in a one hour period
has exceeded the value programmed
•
Wait an appropriate amount of time to restart
•
Turn off the Starts/Hr. feature
Power Loss
➀
(with phase
indication)
35, 36,
& 37
•
Missing supply phase (as indicated)
•
Check for open line (i.e., blown line fuse)
Hall ID
38
•
Incorrect power module has been
installed
•
Check power module and replace
NVS Error
39
•
Data entry error
•
Check user data
•
Replace control module
•
Reset default values
Line Loss
41, 42, 43
•
Line distortion
•
High impedance connection
•
Check supply voltage for capability to start/stop
motor
•
Check for loose connections on line side or motor
side of power wires
Table 9.A SMC Fault Display Explanation (Continued)
Display
Fault Code
Possible Causes
Possible Solutions