Rockwell Automation 20L PowerFlex 700L Frame 1X Liquid-Cooled Adjustable Frequency AC Drive User Manual
Page 4
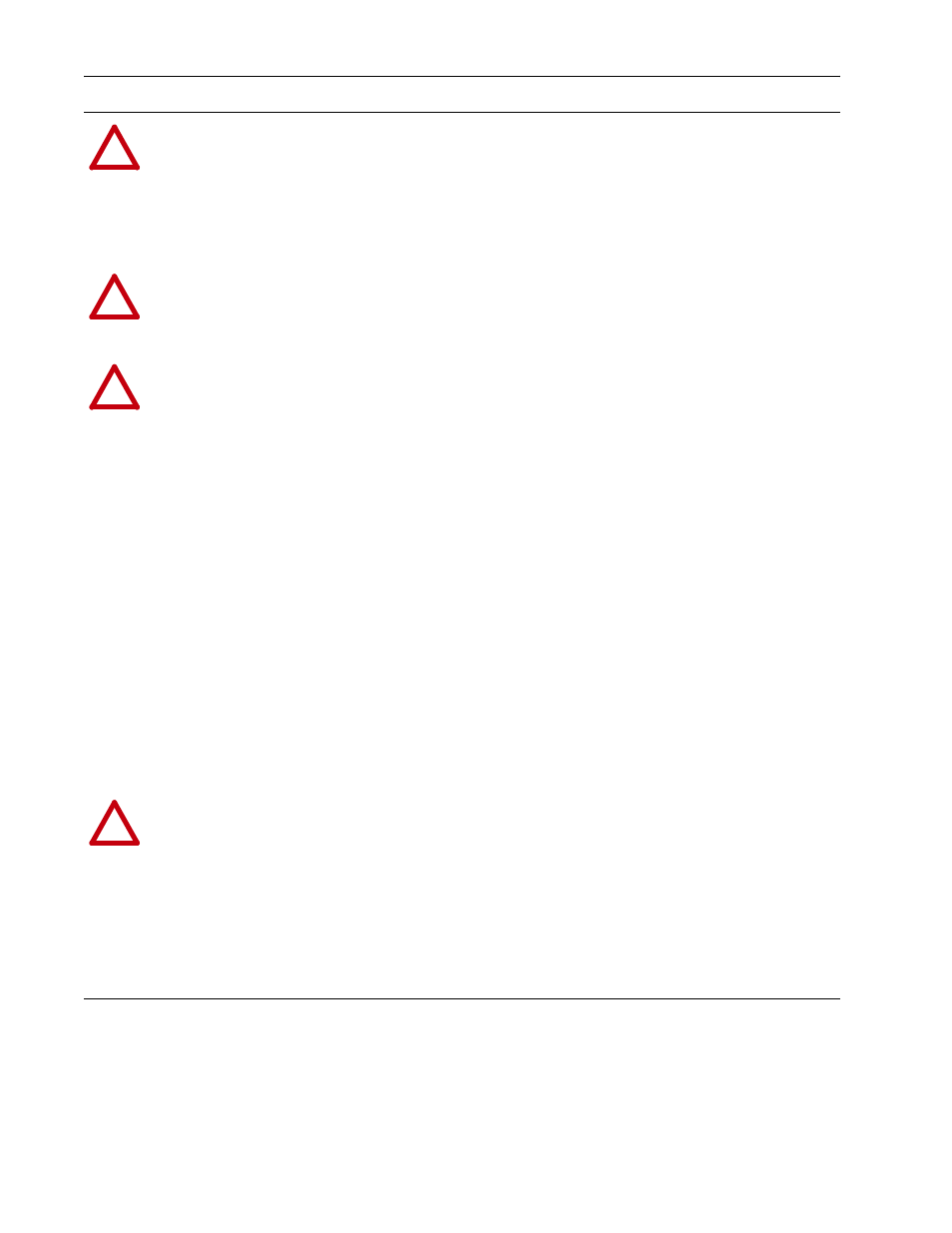
PowerFlex 700L Frame 1X Drive Installation Instructions – Publication 20L-IN013A-EN-P – June 2009
4
!
ATTENTION: An incorrectly applied or installed bypass system can result in component damage
or reduction in product life. The most common causes are:
•
Wiring AC line to drive output or control terminals.
•
Improper bypass or output circuits not approved by Allen-Bradley.
•
Output circuits which do not connect directly to the motor.
Contact Allen-Bradley for assistance with application or wiring.
!
ATTENTION: A contactor or other device that routinely disconnects and reapplies the AC line to
the drive to start and stop the motor can cause drive hardware damage. The drive is designed to use
control input signals that will start and stop the motor. If an input device is used, operation must not
exceed one cycle per minute or drive damage will occur.
!
ATTENTION: The “adjust freq” portion of the bus regulator function is extremely useful for
preventing nuisance overvoltage faults resulting from aggressive decelerations, overhauling loads,
and eccentric loads. It forces the output frequency to be greater than commanded frequency while
the drive's bus voltage is increasing towards levels that would otherwise cause a fault. However, it
can also cause either of the following two conditions to occur.
1. Fast positive changes in input voltage (more than a 10% increase within 6 minutes) can cause
uncommanded positive speed changes. However an “OverSpeed Limit” fault (F25) will occur if
the speed reaches [Maximum Speed] + [Overspeed Limit], (Parameters 82 and 83). If this
condition is unacceptable, action should be taken to 1) limit supply voltages within the
specification of the drive and, 2) limit fast positive input voltage changes to less than 10%.
Without taking such actions, if this operation is unacceptable, the “adjust freq” portion of the bus
regulator function must be disabled (see Parameters 161 and 162).
2. Actual deceleration times can be longer than commanded deceleration times. However, a “Decel
Inhibit” fault (F24) is generated if the drive stops decelerating altogether. If this condition is
unacceptable, the “adjust freq” portion of the bus regulator must be disabled (see Parameters 161
and 162). In addition, installing a properly-sized dynamic brake resistor will provide equal or
better performance in most cases.
Important: These faults are not instantaneous. Test results have shown that they can take
between 2…12 seconds to occur.
!
ATTENTION: To guard against drive damage when using output contactors, the following
information must be read and understood. One or more output contactors may be installed between
the drive and motor(s) for the purpose of disconnecting or isolating certain motors/loads. If a
contactor is opened while the drive is operating, power will be removed from the respective motor,
but the drive will continue to produce voltage at the output terminals. In addition, reconnecting a
motor to an active drive (by closing the contactor) could produce excessive current that may cause
the drive to fault. If any of these conditions are determined to be undesirable or unsafe, an auxiliary
contact on the output contactor should be wired to a drive digital input that is programmed as
“Enable.” This will cause the drive to execute a coast-to-stop (cease output) whenever an output
contactor is opened.