Encoder interface option (vector control only) – Rockwell Automation 20L PowerFlex 700L Frame 1X Liquid-Cooled Adjustable Frequency AC Drive User Manual
Page 31
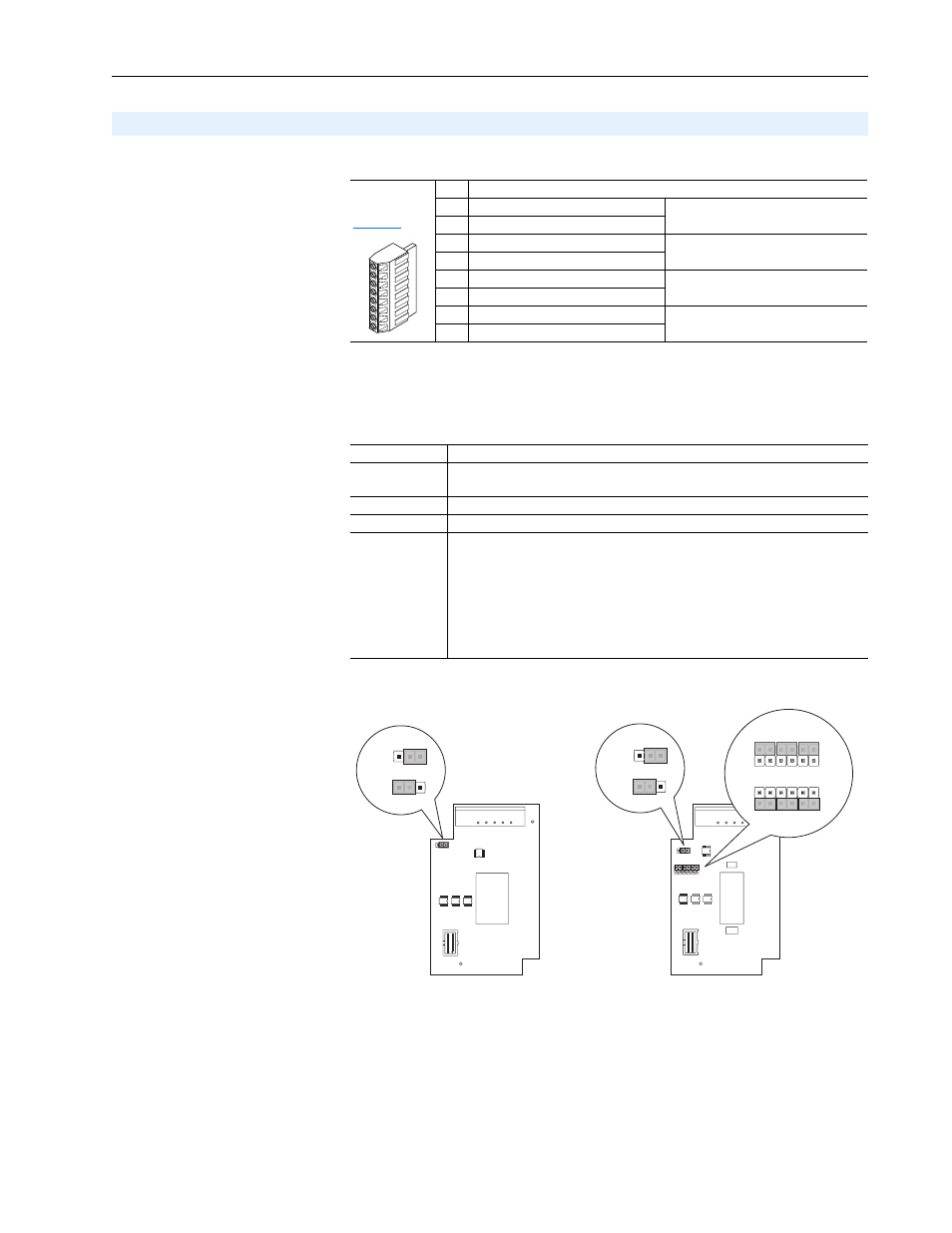
PowerFlex 700L Frame 1X Drive Installation Instructions – Publication 20L-IN013A-EN-P – June 2009
31
Table 10 Encoder Terminal Designations
Table 11 Encoder Specifications
Figure 13
Encoder Board Jumper Settings
Encoder Interface Option (Vector Control Only)
No.
Description
See “Detail” in
Figure 10
8
+12V
(1)
DC Power
(1)
Jumper selectable +5/12V is available on 20B-ENC-1 Encoder Boards.
Internal power source 250 mA.
7
+12V
DC Return (Common)
6
Encoder Z (NOT)
Pulse, marker or registration input.
(2)
(2)
Z channel can be used as a pulse input while A and B are used for encoder.
5
Encoder Z
4
Encoder B (NOT)
Quadrature B input.
3
Encoder B
2
Encoder A (NOT)
Single channel or quadrature A input.
1
Encoder A
Type:
Incremental, dual channel
Supply:
12V, 250 mA. 12V, 10 mA minimum inputs isolated with differential transmitter,
250 kHz maximum.
Quadrature:
90°
,
±
27° at 25 °C.
Duty Cycle:
50%, +10%
Requirements:
Encoders must be line driver type, quadrature (dual channel) or pulse (single
channel), 8…15V DC output (3.5…6V DC when jumpers are in 5V position),
single-ended or differential and capable of supplying a minimum of 10 mA per
channel. Maximum input frequency is 250 kHz. The Encoder Interface Board
accepts 12V DC square-wave with a minimum high state voltage of 7.0V DC. With
the jumpers in the 5V position, the encoder will accept a 5V DC square-wave with
a minimum high state voltage of 3.1V DC. In either jumper position, the maximum
low state voltage is 0.4V DC.
8
1
5/12V
(20B-ENC-2)
J3
J2
+12V
1
2
3
12 11
21
+5VREF
5/12V
(20B-ENC-1, Series B)
J3
+12V
1
2
3
+5VREF
1
2
3
+5V
+12V
1
2
3
+12V
+5V
12 11
21
12 11
21
J3
Output
Configuration
J3
Output
Configuration
J2
Input
Configuration
1
2
3
+5V
+12V
1
2
3