Class1 FoamLogix 2.1A & 1.7AHP REV D User Manual
Page 36
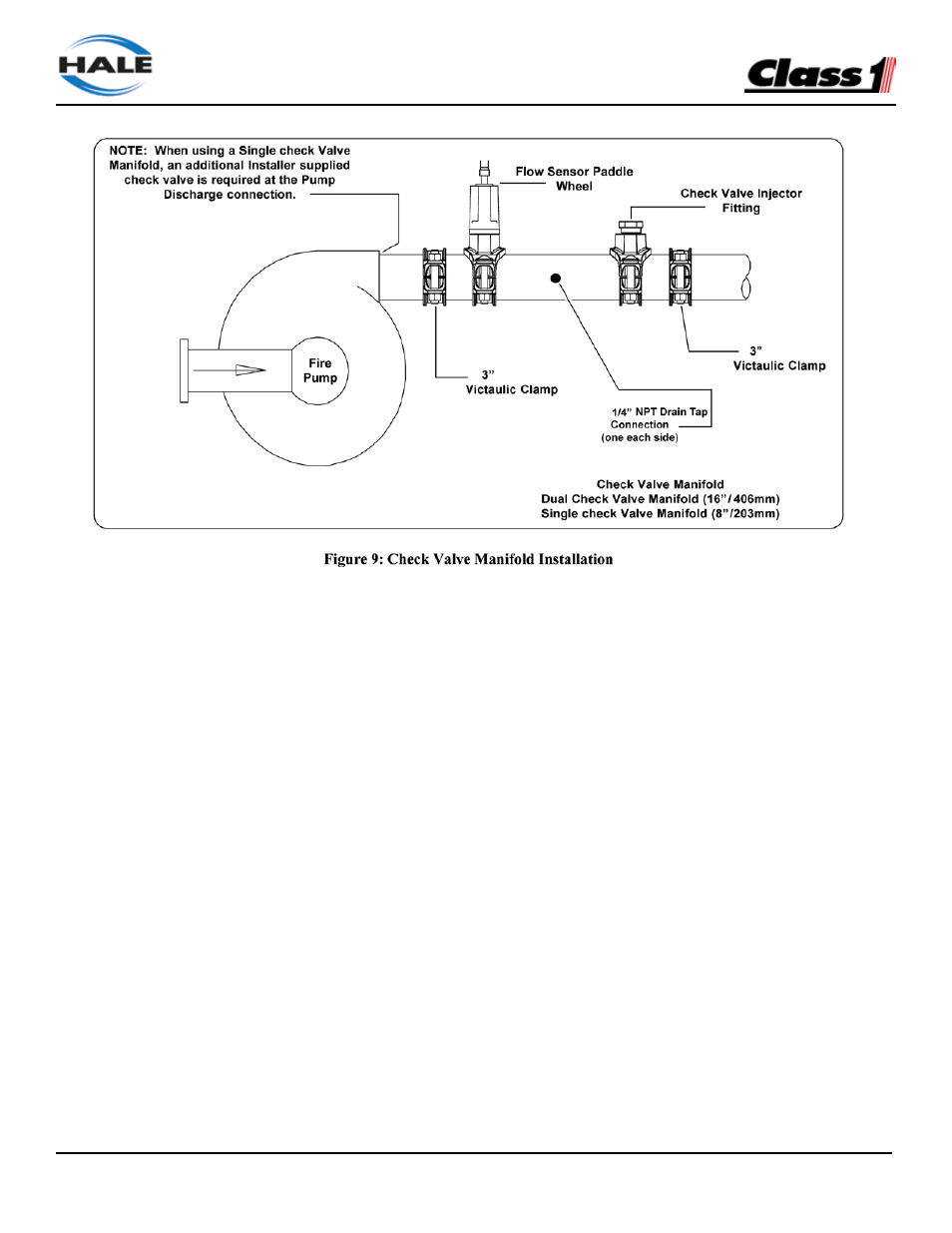
FoamLogix, Model 2.1A and 1.7AHP Class “A”
Electronic Foam Proportioning Systems
36
Note: When the manifold is installed the drain tap
that must be placed in the “down” position and
plumbed to an individual drain.
When properly mounted, the flow sensor and check
valve/injector fitting are on the side of the manifold
and one of the drain ports is on the bottom. The
flow sensor should point upwards slightly to allow
drainage of water and sediment. See Figure 12:
“Flow Sensor Tee Position Range,” on page 38.
Optional Hale Piping Components
Hale piping components, such as 3” (76mm) and
4” (102mm) wafer-type check valves, 115 and 2433
series flanges, mini manifold, etc. are available
to simplify installation of water and foam solution
discharge piping.
The arrangement shown in Figure 10: “Typi cal
Midship Pump Installation,” on page 37, provides
accurate proportioning across a wide range for up to
four discharges from the mini manifold.
The Hale mini manifold provides a 1” NPT tap for
installation of the check valve/injector fitting.
The Hale mini manifold and elbow compo nents
offer 4-3/8” diameter bolt circles and minimize
fabrication and pipe work. After installation, make
sure all pipes, hoses and tubes are supported
using the best industry practices.
Figure 11: “Typical 4” Check Valve Installa tion,
Midship Pump” on page 37 shows a suggested
installation arrangement using Hale 4” (102mm)
check valves, pipe and Hale 2433 flanges.
“Waterway” Check Valves
Check valves in the waterway, rated at 500 PSI
(34.5 BAR), are required to keep foam solution out
of the main pump and allow pump priming without
drawing foam into the piping.