4 putting it all together to run the mpc vector – Pulsafeeder MPC Vector User Manual
Page 68
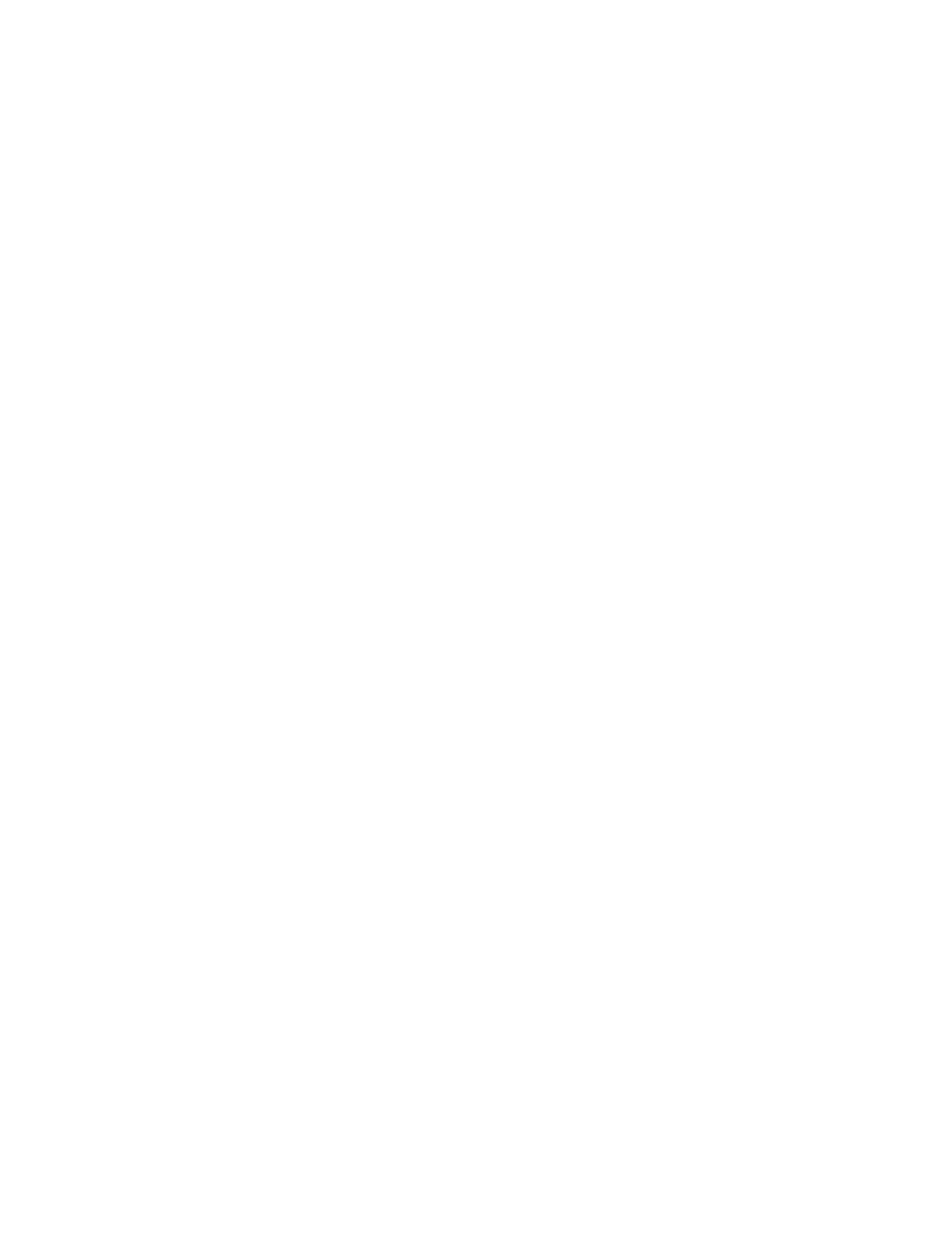
62
21.4
Putting it all together to run the MPC Vector
The proportional, integral, and differential components are all added together into a command sum which is
used to set the motor speed. The motor speed command does have software protection which prevents the
motor speed from ever exceeding the max motor speed or from being negative and therefore if the command
loop is unstable, no damage can be caused to the drive, motor, or pump. Please be aware though that the
motor could reach maximum speed during tuning and all necessary system precautions should be taken.
Also note that the differential part alone can not be used to start the motor since it depends on previous values.
If the previous saved error matches the current error then the differential part will be 0 and therefore the
differential part alone will not start the motor reliably. It is possible to eliminate one of the parts by setting the
appropriate coefficient to 0 (i.e. if you want a PI only controller set Kd to 0 to eliminate the differential part).
However the tuning steps below assume that all 3 parts will be used.
Step 1 – Configure the MPC Vector (reference earlier sections of this IOM for more detail)
1. Make sure that the chosen flow meter is hooked up to the proper location in the MPC Vector.
2. Flow units should be set appropriately in the menu
3. Max flow should be set to at least the max flow achievable by the pump at max speed.
4. Flow sensor type should be set appropriately (digital or analog)
5. Flow calibration should be performed to make sure the MPC Vector flow reading matches flow meter
feedback.
Step 2 – Choosing the test setpoint
In order to tune the PID loop it is necessary to choose a test speed. For most purposes the test flow should be
set to approximately 80 – 85% of the max flow. If the test point is too close to the maximum flow, you may
not notice the overshoot. If the test point is too low you may have an unstable system at higher flow rates.
Step 3 – Tune the Proportional gain
1. Start with an integral gain of 0 and a derivative gain of 0. The proportional gain should be set to allow
the motor to start reliably.
2. Set the motor to the test setpoint
3. Start with a proportional gain of 0.1
4. Make sure that the integral and differential gains are 0
5. At the main operations mode screen, attempt to start the pump. If the motor starts and settles at a low
speed with minimal flow then the proportional gain is set. If not, increase the gain by 0.05 and try
again. Continue until motor start condition is met reliably.
Step 4 – Tune the Integral gain
1. The Integral gain is what will ultimately pull the speed up to the desired setpoint. Note that because
the Integral gain is based on a sum it takes some time for the Integral part to stabilize.
2. Make sure that the proportional gain is set as found above. differential gain is still 0
3. Start with an integral gain of 0.05
4. At the main operations mode screen, start the pump. You should see that the flow is now slowly
building towards the setpoint. Increasing the integral gain will cause the buildup to occur faster. Keep
adding 0.05 to the integral gain until you overshoot your setpoint. As an example, if your setpoint is 5
GPM, your gain might go to 5.1 GPM before falling down to 4.9 GPM or so and oscillate for a few
seconds.