2 density calibration, Density calibration, On 8.2 – KROHNE MFC 010 C Converter User Manual
Page 74
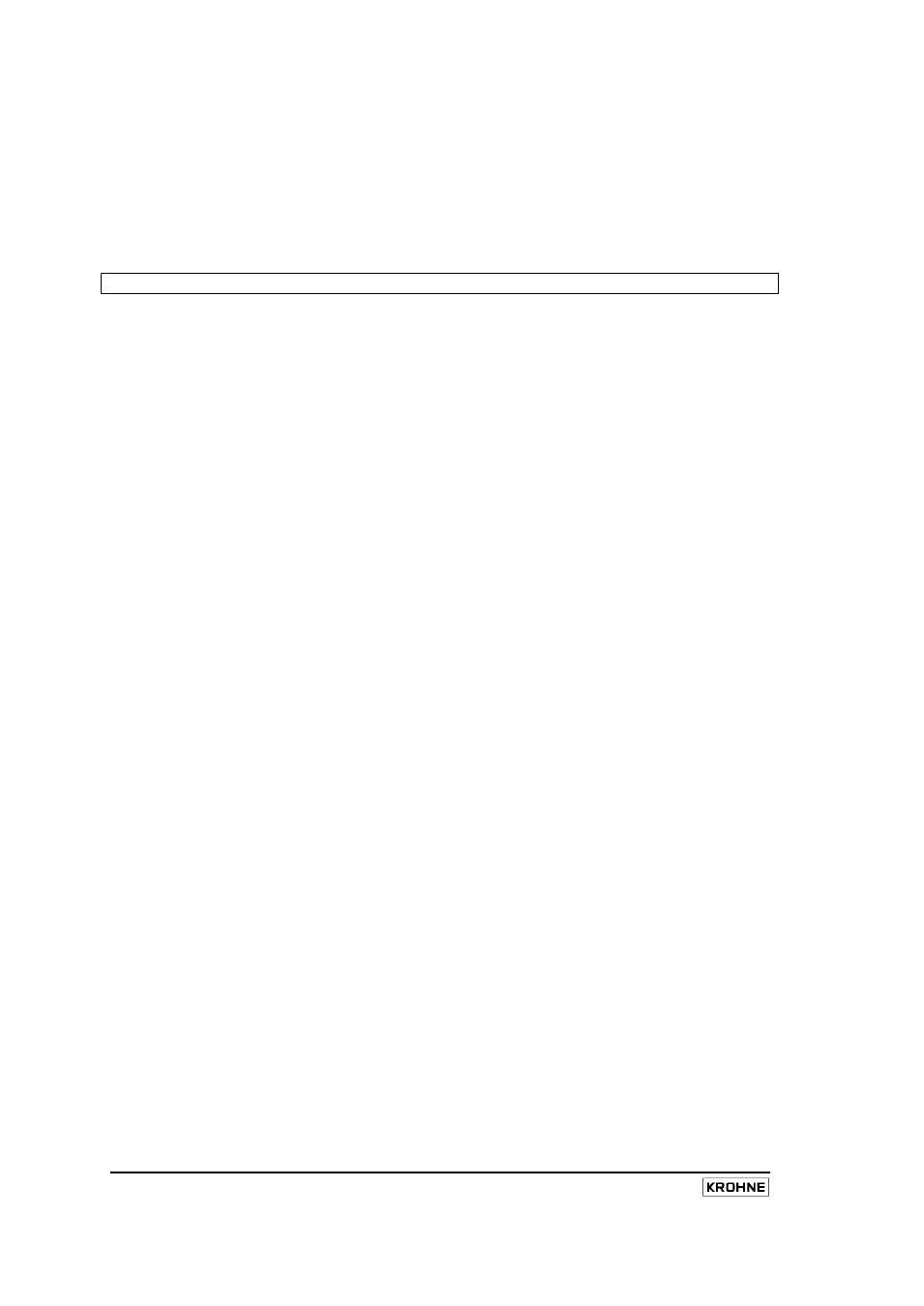
72
MFC010 Interface Manual
The “Zero Calibration Status Flag”, held in Binary Input register no. 1008, indicates when the system has
detected an er ror dur ing t he c alibration pr ocess and has s ubsequently abandoned t he c alibration
operation. There are two r easons f or t his t o oc cur. T he f irst w ill oc cur w hen t he f low r ate dur ing
calibration exceeds ±10% of the sensors nominal flow. The second will occur when the system is not in
“Measurement” m ode, dur ing t he c alibration per iod. A t the instant the system mode changes from
“Measurement” the Zero Calibration process will be terminated, this is also the case if the system is not in
“Measurement” mode when the calibration is initiated.
8.2
Density Calibration
Although an accurate calibration of density is performed during the manufacturing process, this factory
calibration is performed on Air and Water and as such covers a large range of possible measurement due
to the wide-ranging applications into which the Optimass sensors are installed. It is always advisable, if
possible, for the user/installer to perform a density calibration on the actual process fluid, preferably at the
two extremes of the process density. T his will provide a m uch greater degree of accuracy for the target
application process.
The U ser c an c hoose t o per form ei ther a “ One poi nt” or “Two point” c alibration. T he “ Two poi nt”
calibration i s bes t t o be us ed when t here ar e t wo c learly def ined process densities, the single point is
more appropriate when there is one, or a l ess clearly defined or narrow range of process densities. The
procedure f or t he “ One poi nt” and “ Two poi nt” c alibrations i s v ery m uch t he s ame, t he “ Two poi nt”
calibration merely being a case of repeating the “Single point” calibration, though the user should note
that the output status registers used to initiate the “One point” and “Two point” calibrations are different (
see section 7.2 ).
The User can choose to use one of three preset product types (see Holding Register No 1028) for which
the system will use internally programmed polynomials to determine the correct density at the measured
process t emperature. Alternatively the user can select the fourth product type, “Other”, and enter a
density value i nto t he c alibration dens ity hol ding r egister ( see H olding R egister N o 3093) . D uring t he
calibration pr ocess t he s ystem w ill measure the tube par ameters f or t he s elected pr ocess dens ity and
temperature and store them for use in the measurement algorithms.
Should it be necessary the user can elect to restore the original factory calibration values by selecting
output r egister num ber 1014 . T he us er m ust t hen s ave t he r estored configuration to the non-volatile
memory by selecting output register number 1001.
When a “ One poi nt” c alibration i s performed for t he f irst t ime, t he M FC010 w ill r eplace t he f actory
calibrated “Empty” value with the new user calibration value. Subsequently, the MFC010 will use the
newly calibrated value to replace the calibration value that is the closest to it.
NB
. The OPTIGAS 5000 meter does not measure density, so any attempt to perform a density calibration
will be rejected and will result in an error condition in the density status.