A.1.9 cs40 - dual two-loop cascade controller – Micromod Micro-DCI: 53MC5000 Multi-Loop Process Controller FLEXIBLE CONTROL STRATEGIES User Manual
Page 162
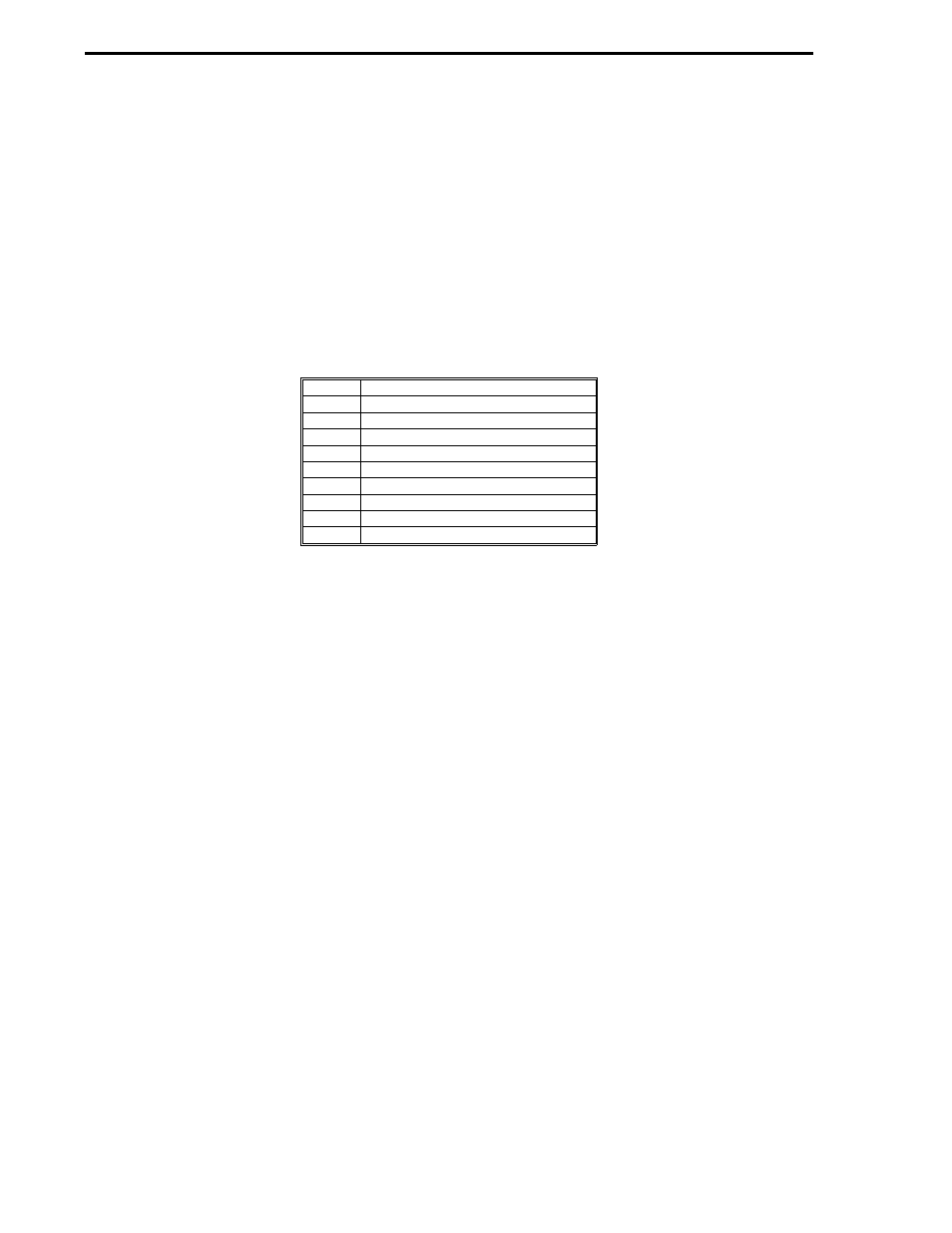
A.1.9 CS40 - DUAL TWO-LOOP CASCADE CONTROLLER
The dual two-loop cascade controller consists of four standard PID control loops, arranged as two
cascade pairs, with a primary and a related secondary controller.
Loading CS40 initializes the ANI1–3 engineering spans to 100.0, C076 and C085 to 1.0, C077 and
C086 to -1.0, and the four loop control list sequence. The control scheme is shown in block dia-
gram form in Figure A-9. Also provided is Table A-9, which is a worksheet that shows the CS40
wirelist connections; wirelist datapoints not connected are left at default. Table A-9 is partitioned
by FCS module type applicable to CS40 (those modules illustrated in Figures 2-1 through 2-3).
The datapoint parameters for each module are shown with their default values.
The following I/O assignments result from loading CS40:
ANI0
Process Variable Loop 1
ANI1
Process Variable Loop 2
ANI2
Process Variable Secondary Loop 1
ANI3
Process Variable Secondary Loop 2
ANO0
Control Output Secondary Loop 1
ANO1
Control Output Secondary Loop 2
CCI0
Cascade Enable Loop 1
CCI1
Cascade Enable Loop 2
CCO0
Process Alarms Secondary Loop 1
CCO1
Process Alarms Secondary Loop 2
Each cascade control setup provides bumpless/balanceless transfer between local and cascade
control by forcing the primary output to match the secondary setpoint when the secondary is in lo-
cal mode. Proper scaling of the primary output (secondary setpoint) is accomplished using the K1
and B1 parameters of the secondary controller. ANI2 and ANI3 are the controlled process vari-
ables of the secondaries for their respective cascade loops. Outputs ANO0 and ANO1 drive the fi-
nal control elements regulating their values. The primary process variables are provided by ANI0
and ANI1 for their respective cascade loops. Each cascade loop provides a contact input (CCI0 or
CCI1) that will disable the cascade if the contact is not closed.
Alarm conditions of the secondary controllers are indicated by CCO0 and CCO1. To permit selec-
tion of local and cascade operation, the remote enable parameters of the secondaries (L163 and
L187) must be set to 1; otherwise, only local operation is possible.
FCS 53MC5000 Flexible Control Strategies
A–72
419-TXT