Pid m – IDEC MicroSmart Pentra User Manual
Page 36
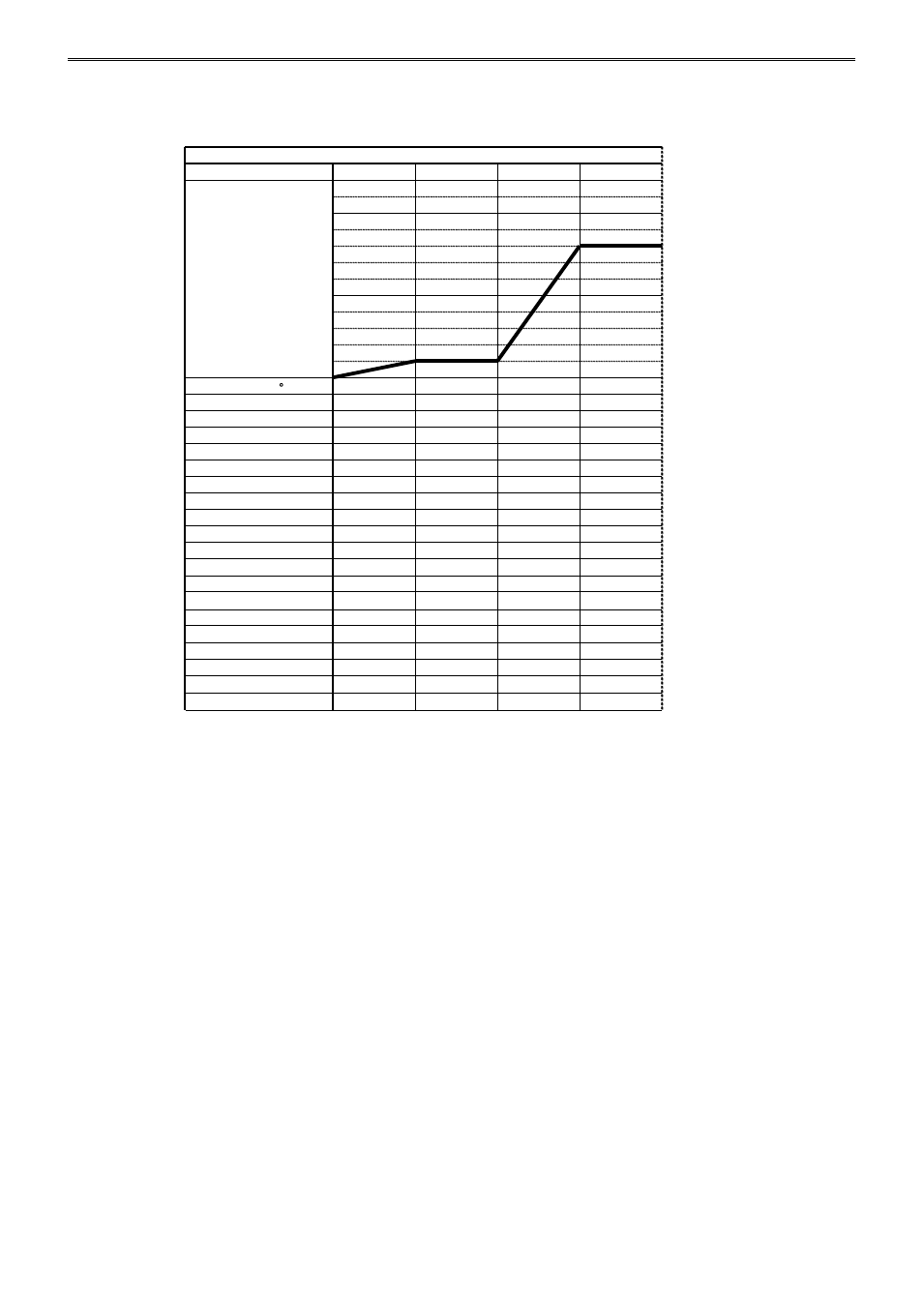
PID M
ODULE
M
AIN
F
UNCTIONS
FC5A MicroSmart PID Module User’s Manual FC9Y-B1283
4-13
Program Pattern
100
100
800
800
0
500
1000
60
60
300
30
10
0
10
0
0
1
2
3
10
10
10
10
200
200
200
200
50
50
50
50
50
50
50
50
0
0
0
0
0
10
0
10
0
0
0
0
0
0
0
0
0
0
0
0
0
0
0
0
0
0
0
0
0
0
0
0
0
0
0
0
100
100
100
100
0
0
0
0
1.0
1.0
1.0
1.0
0.0
0.0
0.0
0.0
Step No.
Set Point (SP)
Set Point
Wait Value
Proportional Term
Integral Time
ARW
Output MV Rate-of-Change
Alarm 1 Value
Output MV Upper Limit
Output MV Lower Limit
Cooling Proportional Band
Overlap/Dead Band
Time (Minutes)
C
Derivative Time
( )
Alarm 2 Value
Alarm 3 Value
Alarm 4 Value
Alarm 5 Value
Alarm 6 Value
Alarm 7 Value
Alarm 8 Value
(SP)
Program Pattern Example
The set point (SP) configured for each step is handled as the set point (SP) at the end of the step. The
time configured for each step is the process time of each step.
When the program pattern is configured as shown in the above table, the following control is
performed at each step:
[Step 0]: The set point (SP) is gradually risen to 100
°C
in 60 minutes.
When the step 0 ends, the wait function works so that the program control does not
proceed to the step 1 until the process variable (PV) reaches 90
°C.
[Step 1]: The fixed value control is performed at 100
°C
of the set point (SP) for 60 minutes.
[Step 2]: The set point (SP) is gradually risen to 800
°C
in 5 hours.
When the step ends, the wait function works so that the program control does not proceed
to the step 3 until the process variable (PV) reaches 790°C.
[Step 3]: The fixed value control is performed at 800
°C
of the set point (SP) for 30 minutes.