Application examples, Application example 1, Pplication – IDEC MicroSmart Pentra User Manual
Page 122: Xamples, Application example 1 -1
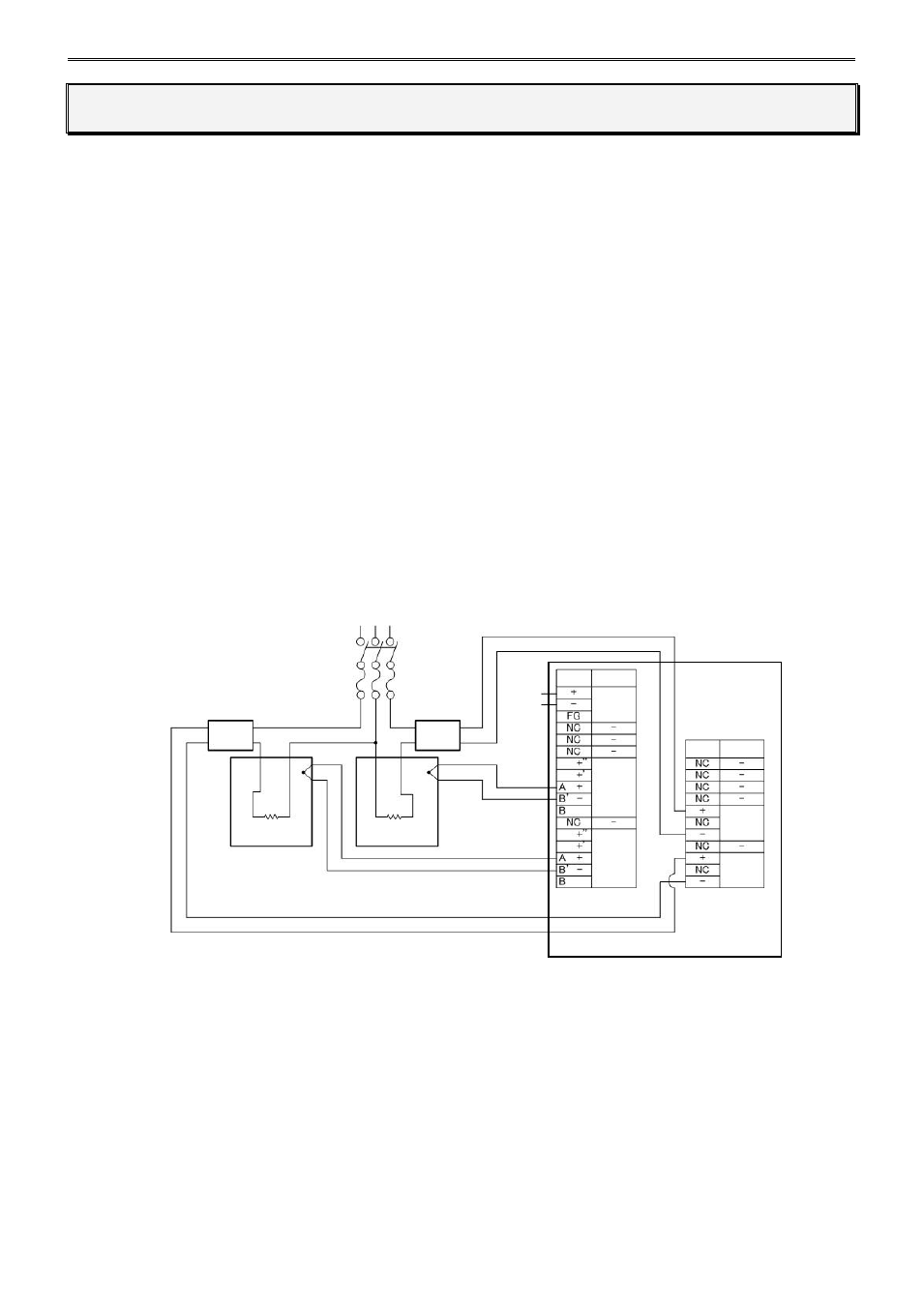
A
PPLICATION
E
XAMPLES
FC5A MicroSmart PID Module User’s Manual FC9Y-B1283
7-1
7: A
PPLICATION
E
XAMPLES
This chapter describes the PID modules application examples.
Application Example 1
This application example demonstrates the temperature control for a system using two electric furnaces. The
set point (SP) of CH0 control is 200°C. The set point (SP) of CH1 control is 210°C.
• PID control is performed based on the temperature input to the PID module. The control output is turned on
or off in accordance with the output manipulated variable (MV).
• PID parameters (proportional band/proportional gain, integral time, derivative time, and ARW) are
automatically calculated using auto-tuning (AT).
• If the process variable (PV) of CH0 control becomes 205°C or higher, the upper limit alarm output (Q0) is
turned on and the control is disabled.
• If the process variable (PV) of CH1 control becomes 215°C or higher, the upper limit alarm output (Q1) is
turned on and the control is disabled.
System Configuration and Wiring
Wiring Example of the FC5A-F2M2 [Non-contact voltage output (for SSR drive)/current output type]
3-phase
Power Supply
CH0 Thermocouple
CH1 Thermocouple
+
-
+
-
SSR
SSR
+
-
+
-
Power
Supply
Electric
Furnace 2
Electric
Furnace 1
PID Module (FC5A-F2M2)
Channel
Terminal
No.
IN0
24V DC
OUT0
OUT1
IN1
Terminal
No.
Channel