5 operation sequence at occurrence of alarm – Yaskawa Sigma-5 User Manual: MECHATROLINK-II Commands User Manual
Page 30
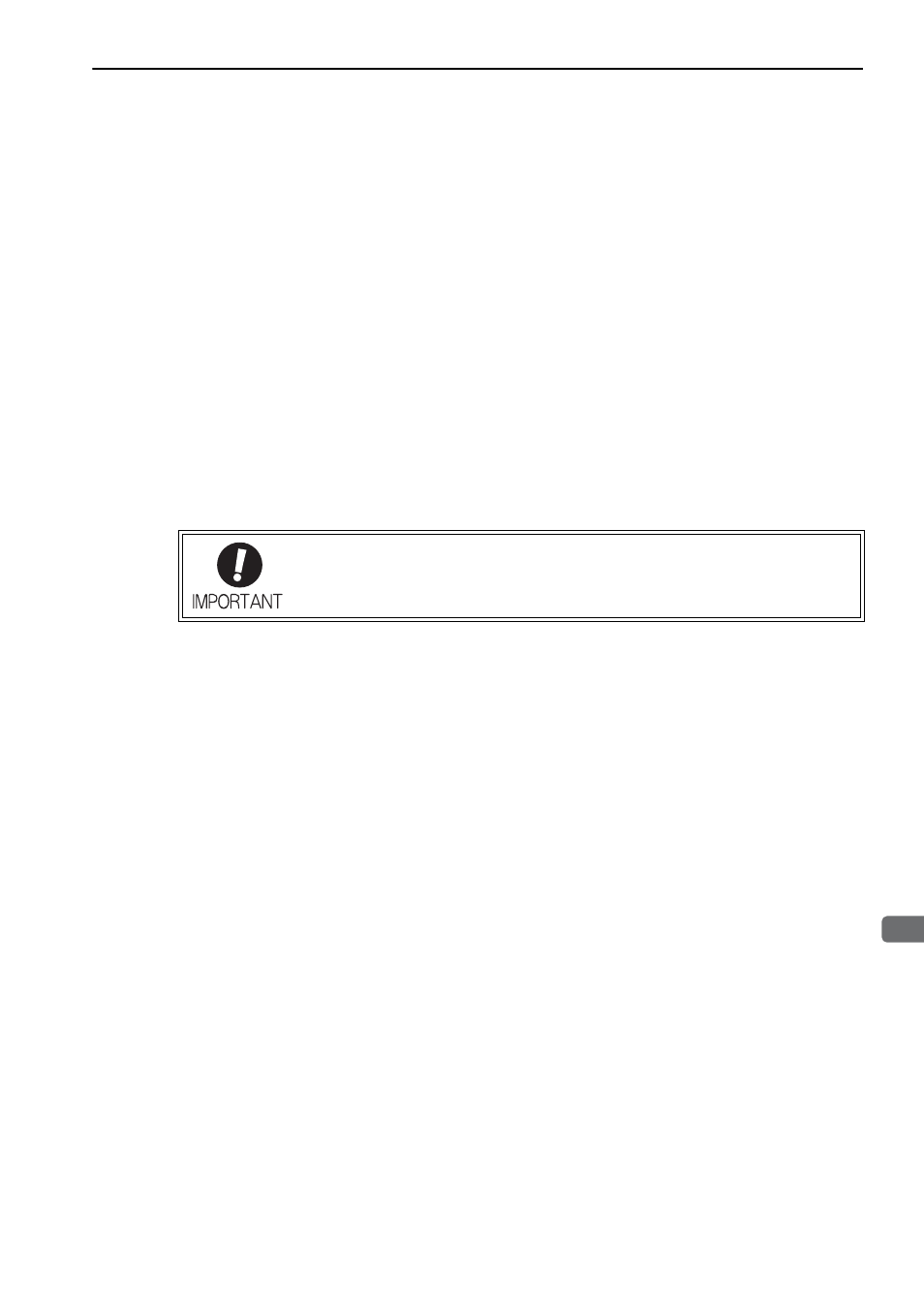
2.4 Specific Operation Sequences
2-13
2
Operation Sequence
2.4.5 Operation Sequence at Occurrence of Alarm
When the ALM bit in STATUS field of response turns on (= 1), send SV_OFF command. Use ALM_RD com-
mand to check the alarm occurrence status.
To clear the alarm status, send ALM_CLR command after removing the cause of alarm. However, the alarms
that require turning the power supply off and then on again to clear the alarm status, sending ALM_CLR com-
mand will not clear the alarm status.
If a communications alarm A.E5
or A.E6
occurs, send ALM_CLR command to reset the alarm and then
send SYNC_SET command.
2.4.6 When Motion Command Is Interrupted and Servomotor Is in Position
During execution of a Motion command, any one of the following statuses on the SERVOPACK will cause
interruption of the motion command and an in-position status of PSET=1.
• Alarm occurrence (ALM of STATUS field =1) causes Servo-Off (SVON of STATUS field =0).
• Main power supply OFF (PON of STATUS field =0) causes Servo-Off (SVON of STATUS field =0).
• OT ON (P-OT or N-OT of IO_MON field = 1) or Software-Limit ON (P_SOT or N_SOT of STATUS field
= 1) causes the motor to stop.
Even when PSET is 1 in these cases, the motor may not reach the target position that the host controller speci-
fied. Obtain the feedback position (APOS) to make sure that the axis has stopped at a safe position.
The host controller may not be able to monitor a brief change in the P-OT or N-OT signal
to P-OT=1 or N-OT=1. Proper selection, installation and wiring in the limit switch is
required to avoid chattering and malfunctions in the OT signal.