Control technology | ethercat communication manual – Lenze EtherCAT control technology User Manual
Page 93
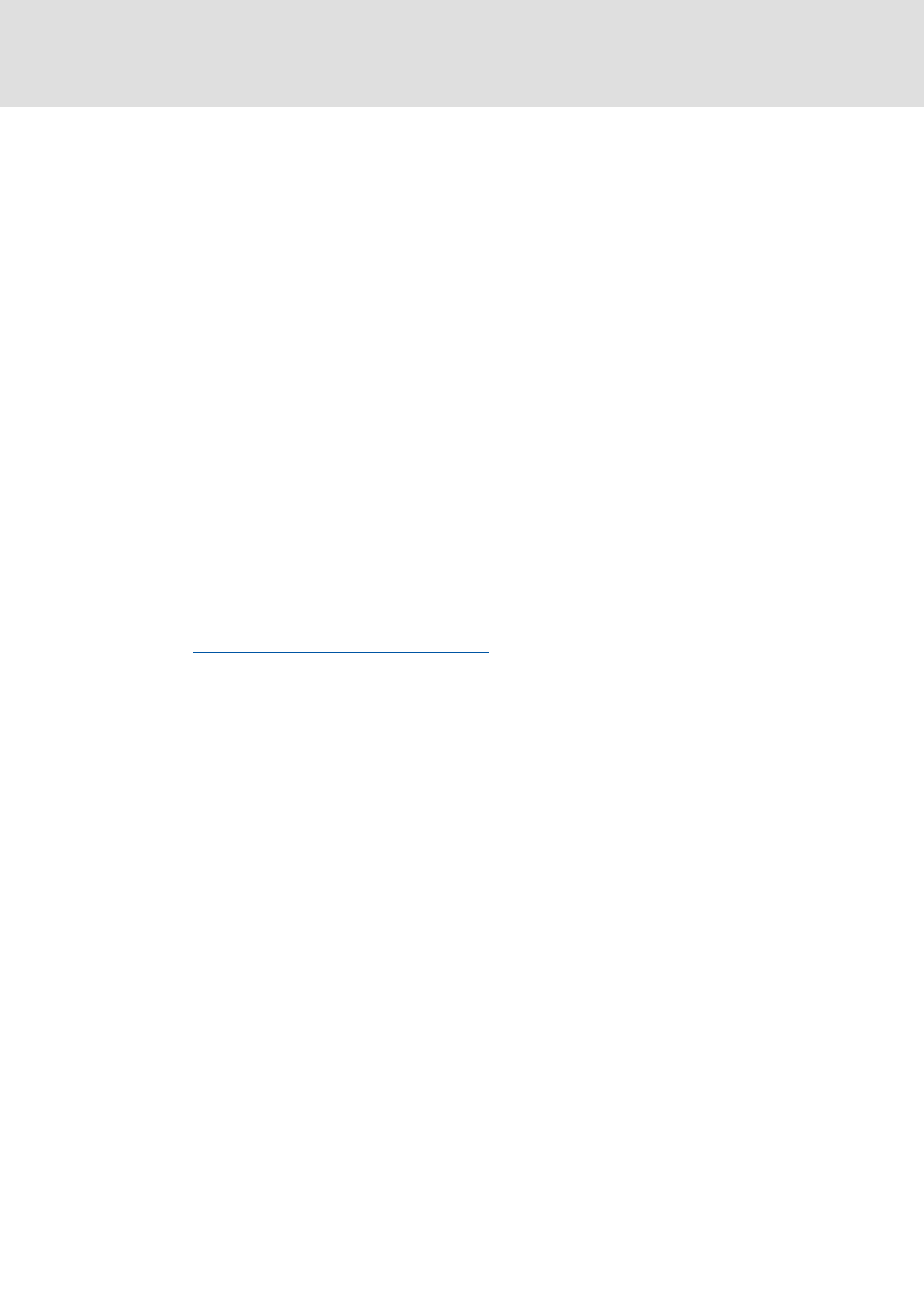
DMS 3.1 EN 01/2011 TD17
L
93
Control technology | EtherCAT communication manual
EtherCAT with CANopen or PROFIBUS
Addressing EtherCAT nodes using CANopen/PROFIBUS nodes
8.2
Addressing EtherCAT nodes using CANopen/PROFIBUS nodes
The addresses for input and output objects of the EtherCAT stations are allocated in the
»EtherCAT Configurator«. Afterwards, the EtherCAT configuration is imported into the
»PLC Designer« control configuration.
There are two cases for the control configuration in the »PLC Designer«:
1. PROFIBUS/CANopen before EtherCAT:
– Keep the standard settings for address allocation for the PROFIBUS/CANopen
stations in the »PLC Designer« control configuration. (The addressing of the
PROFIBUS/CAN stations starts with ’0’.)
– Define a sufficient address offset for the first input and output object in the
»EtherCAT Configurator« at the first EtherCAT slave (> PROFIBUS/CAN addresses).
The addresses of the other input and output objects are updated automatically after
the entry.
Thus, address conflicts can be prevented after the import of the EtherCAT
configuration into the »PLC Designer« control configuration.
2. EtherCAT before PROFIBUS/CANopen:
– Do not define any address offsets in the »EtherCAT Configurator«. (The addressing of
the EtherCAT stations starts with ’0’.)
– For PROFIBUS/CANopen stations, no address offsets must be defined in the »PLC
Designer« control configuration. If address offsets are defined, the offsets must be
greater than the EtherCAT addresses.