Drive motor reassembly, Drive motor reassembly -34, Bearing pressure guidelines -34 – JLG 3246ES Service Manual User Manual
Page 70
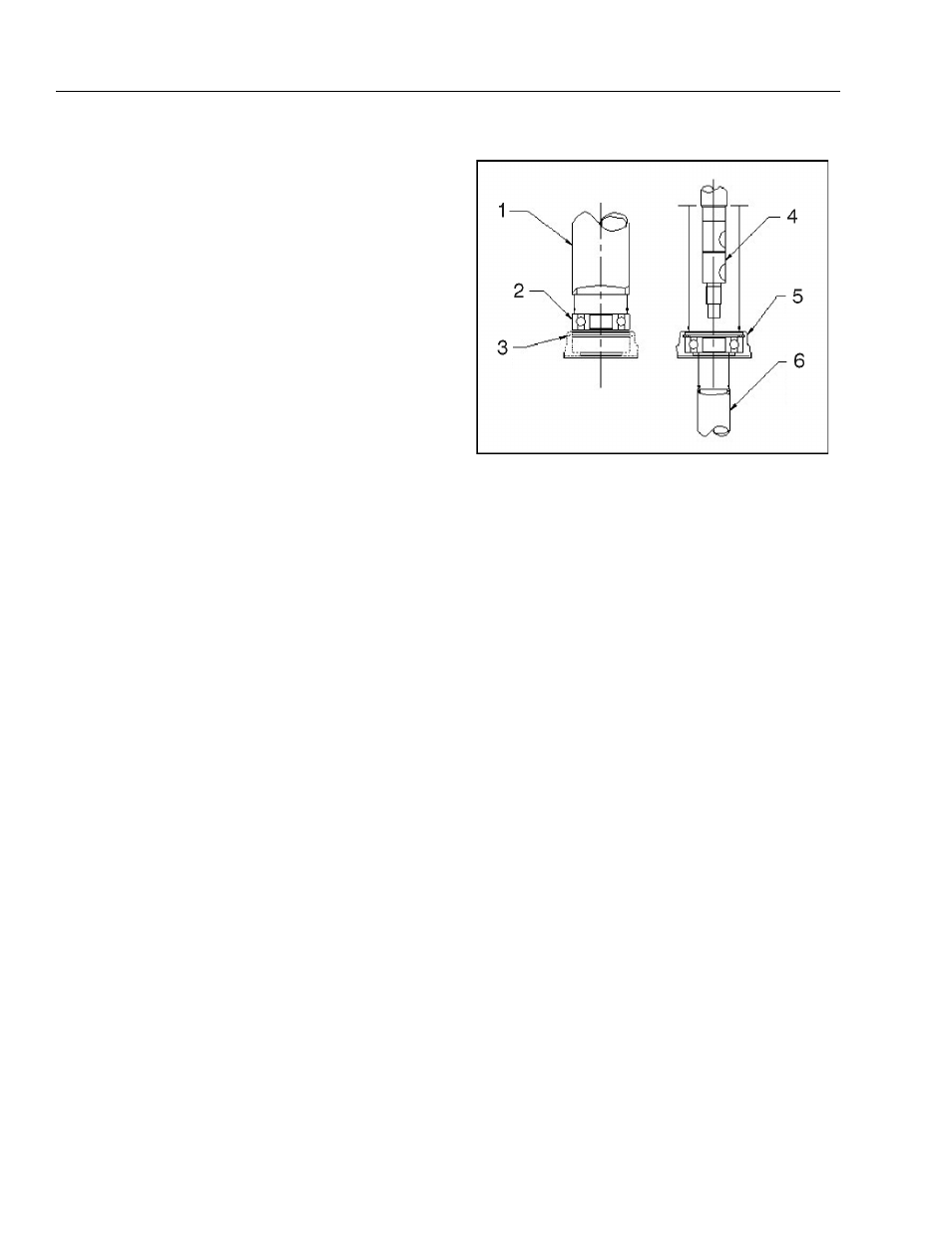
SECTION 3 - CHASSIS & SCISSOR ARMS
3-34
– JLG Lift –
3121166
dition. Verify that pole screws are torqued to 250 -
300 in-lb (28.2 - 33.9 Nm). Verify field resistance
using a suitable ohmmeter per the appropriate
motor specification. Verify that the field is electri-
cally isolated from the frame using a dielectric tes-
ter. Replace as necessary.
5.
Visually inspect the Armature Assembly (3) for
signs of overheating or physical damage. Visually
inspect the seal surface of the shaft for excessive
wear. Check for grounded circuits using a dielec-
tric tester by applying voltage between the com-
mutator and the shaft. Visually inspect the
commutator for excessive wear and overheating.
Replace as necessary.
6.
Visually inspect the brake surfaces for excessive
wear. Replace Brake Assembly (11) if necessary.
7.
Visually inspect the Wire Harness (1) for frayed
insulation, loose terminals, or other damage.
Replace as necessary.
Drive Motor Reassembly
NOTE: Refer to Figure 3-29.
1.
After inspection and servicing, reassemble the wir-
ing in the Commutator End Head (9) as originally
found. Ensure the wiring does not contact metal
parts and that it allows the brushes to move unre-
stricted in the holders. Motor terminals must be
assembled as shown Figure 3-31. Torque bottom
terminal nut to 110 - 140 in-lb (12.4 - 15.8 Nm).
2.
After the motor has been disassembled, it is rec-
ommended that new bearings be installed
because bearings may have been damaged during
removal. Although the bearings may appear and
feel good, the bearing races could be “brinelled”
(races or balls deformed) and may exhibit noise
and vibration problems or fail within a relatively
short period of service. Press a new bearing into
the commutator end head, pressing on the outer
race only. See Figure 3-27.. Replace the Retaining
Ring (7) in the retaining ring groove.
3.
Press the Armature (3) commutator end into the
commutator end head and bearing assembly,
carefully supporting the inner-race of the bearing.
See Figure 3-27.
4.
Carefully release the Brush Springs (4) allowing the
Brushes (5) to contact the commutator. Make sure
brush shunts do not interfere with spring move-
ment.
5.
Assemble the commutator end head to the Frame
& Field Assembly (2) and tighten the screws to 120
- 140 in-lb (13.6 - 15.8 Nm). Make sure to align the
field connection with the notch in the commuta-
tor end head. Seal wires where they exit from com-
mutator end head with the Grommet (10).
6.
Place the Gasket Seal (12) in the bottom of the
notch in the commutator end head. Align wires
from the Brake Assembly (11) into the notch in the
commutator end head. Secure brake assembly to
commutator end head using three bolts.
7.
Install Wire Harness (1) to motor by connecting the
brake connectors and securing the armature ter-
minals to the terminal studs. Crimp the field con-
nection (red/orange to orange and blue to blue)
together and heat shrink. Motor terminals must be
assembled as shown in Always secure the bot-
tom nut with a wrench as you tighten the top
nut. Torque top nut to 90 - 110 in-lb (10.2 - 12.4
Nm).
1.
Press Fixture must press against Outer Race
2.
Bearing
3.
End Head (held stationary)
4.
Armature Assembly
5.
Assembled End Head, Bearing, and Retaining
Ring
6.
Press Fixture must press against Inner Race (held
stationary)
Figure 3-30. Bearing Pressure Guidelines