5 electric drive motor, Disassembly, Replacing motor bearing – JLG 3246ES Service Manual User Manual
Page 62: Inspecting motor brushes, Replacing motor brushes, Replacing the motor cable, Electric drive motor -26
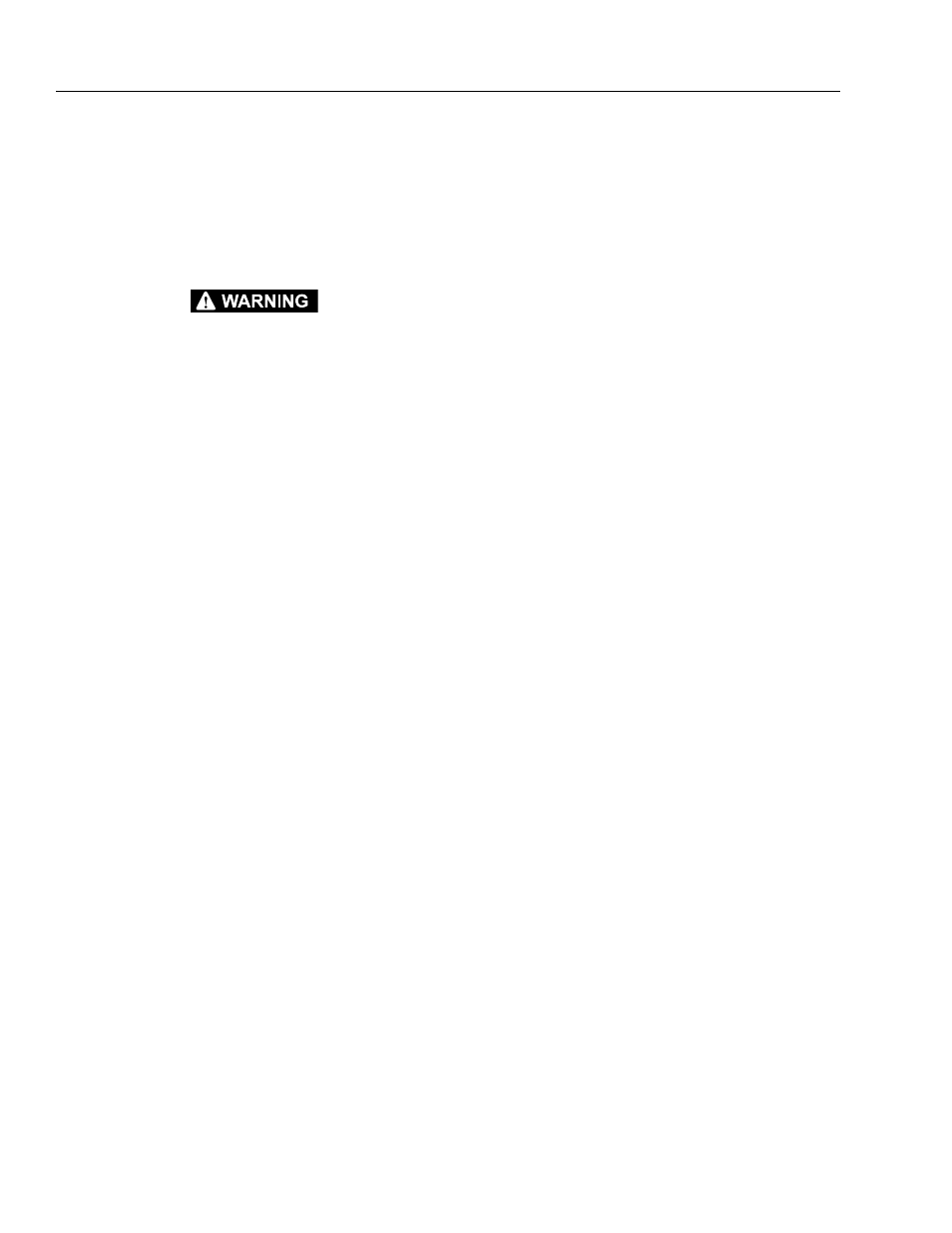
SECTION 3 - CHASSIS & SCISSOR ARMS
3-26
– JLG Lift –
3121166
3.5
ELECTRIC DRIVE MOTOR
NOTE: The information contained within this section
applies to the following machines:
USA machines built S/N 0200152825 to S/N
020170585,
Belgium machines built S/N 1200008481 to S/N
1200015159.
DISCONNECT THE BATTERY AND ALLOW THE MOTOR TO COOL
DOWN BEFORE PERFORMING ANY MAINTENANCE. THE SUR-
FACE TEMPERATURE OF THE MOTOR FRAME MAY CAUSE INJURY
TO PERSONNEL.
Disassembly
1.
Disassemble the motor from the gearbox.
2.
Mark the position of the motor end cap to the
motor shell.
3.
Remove the end cap retaining bolt.
4.
Remove the retention bolt and washer from the
end of the armature and remove armature from
the motor shell.
NOTE: The load spring that is behind the motor bearing will
be loose when the armature is removed. Take care
not to lose it.
Replacing Motor Bearing
1.
Carefully remove the bearing from the armature
by using a bearing puller.
2.
Support the armature securely, Using a sleeve
pressing tool or a large socket press the bearing
onto the end of the shaft until it bottoms out on
the shoulder. The pressing tool must touch the
bearing on the inner raceway.
Inspecting Motor Brushes
NOTE: Motor brushes should be inspected every 1000 hours.
1.
Loosen the strain relief of the cable and push
approximately 1 in. (25 mm) of cable into the
motor.
2.
Separate the end piece from the motor shell by
approximately 1 in. (25 mm).
3.
Using compressed air, clean the brush housing
area of any accumulated carbon dust.
4.
Remove the screw in each of the brush holders
that connects the brush wires.
5.
Remove each of the four brushes from the brush
holder.
6.
Inspect each brush, if the brush is equal to or less
than 3/8 in. (9.5 mm), the brush will need replaced.
Replacing Motor Brushes
1.
When installing new brushes, the motor commu-
tator must be cleaned to allow for good brush con-
tact. To do this, mount the armature in a lathe and
take a skin cut on the commutator diameter.
2.
Remove any copper chips that may have settled
between the commutator bars.
3.
Measure the diameter of the commutator. If the
diameter is less than 2.8 in. (70.5 mm) the commu-
tator can no longer be used.
4.
Measure the depth of the commutator mica (com-
mutator bar insulation). Verify that the depth of
the mica is at least.016 in. (0.4 mm). If the depth is
too shallow, undercut the mica to a maximum
depth of 0.048 in. (1.2 mm). After undercut, clean
the armature of any loose mica.
5.
Install the new brushes into the brush holders.
Make sure the brush is in the correct orientation to
make smooth contact on the commutator.
6.
Connect the brush wires to the terminal on the
brush holder using the bolts that were removed
earlier.
7.
Pull each brush spring so that it is contacting the
side of the brush. Push the brush springs towards
the outside of each brush box so that the armature
can be reassembled.
Replacing the Motor Cable
1.
Using a knife, remove the shrink tubing from the
cable butt splices that stick through a cast hole in
the motor cap end.
2.
Mark the brush leads at each splice according to
the color of the cable lead that it is connected to.
3.
Cut the leads going into each butt splice.
NOTE: Be sure to cut the leads just below the splice to leave
as much cable as possible.
4.
Cut off the motor connector that connects to the
brake.
5.
Remove the motor end cap from the motor shell.
6.
Using a knife, remove the shrink tubing that is on
the field lead butt splices. There should be 2
splices.
7.
Mark the field leads going into each splice accord-
ing to the color of the cable lead.
8.
Cut the leads going into each butt splice.
NOTE: Be sure cut the leads just below the splice to leave as
much cable as possible.
9.
Remove the old cable from the motor shell.
10.
Install the new motor cable into the motor shell
through the strain relief such that the end of the