Derivative time 64, Output power offset (manual reset) 64, Pid adjustments 64 – Red Lion TCU User Manual
Page 72
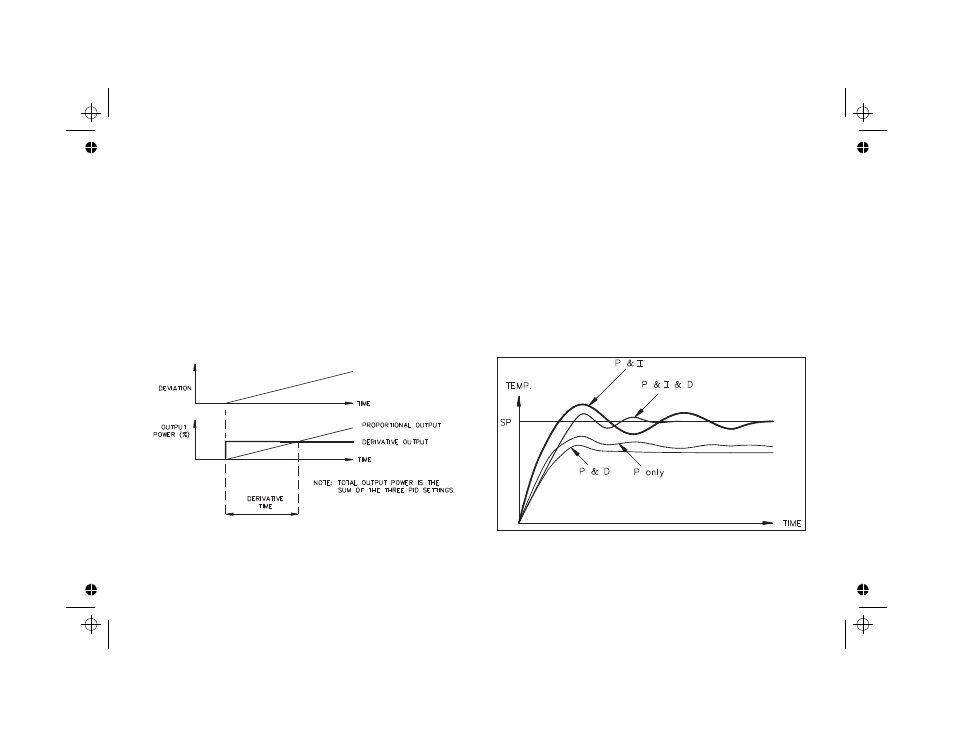
Derivative Time
Derivative time is defined as the time, in seconds, in which the output due
to proportional action alone equals the output due to derivative action with a
ramping process error. As long as a ramping error exists, the derivative action
is “repeated” by proportional action every derivative time. The units of
derivative time are seconds per repeat.
Derivative action is used to shorten the process response time and helps to
stabilize the process by providing an output based on the rate of change of the
process. In effect, derivative action anticipates where the process is headed
and changes the output before it actually “arrives”. Increasing the derivative
time helps to stabilize the response, but too much derivative time coupled
with noisy signal processes, may cause the output to fluctuate too greatly,
yielding poor control. None or too little derivative action usually results in
decreased stability with higher overshoots. No derivative action usually
requires a wider proportional and slower integral times to maintain the same
degree of stability as with derivative action. Derivative action is disabled by
setting the time to zero.
Output Power Offset (Manual Reset)
If the integral time is set to zero (automatic reset is off), it may be necessary
to modify the output power to eliminate errors in the steady state. The output
power offset (OPOF) is used to shift the proportional band to compensate for
errors in the steady state. The output power offset (OPOF) parameter appears
in the unprotected mode, if the integral time equals zero. If integral action
(automatic reset) is later invoked, the controller continues from the previous
output power offset and updates accordingly.
PID Adjustments
To aid in the adjustment of the PID parameters for improved process
control, a temperature chart recorder is necessary to provide a visual means of
analyzing the process. Compare the actual process response to the PID
response figures with a step change to the process. Make changes to the PID
parameters in no more than 20% increments from the starting value and allow
the process sufficient time to stabilize before evaluating the effects of the new
parameter settings.
64
Figure 33, Derivative Time
Figure 34, Typical Response Curve