Local/remote setpoint transfer modes (sptr) 38, Secondary output power dampening (opd2) 38, Valve positioner module (8-vp) 38 – Red Lion TCU User Manual
Page 46
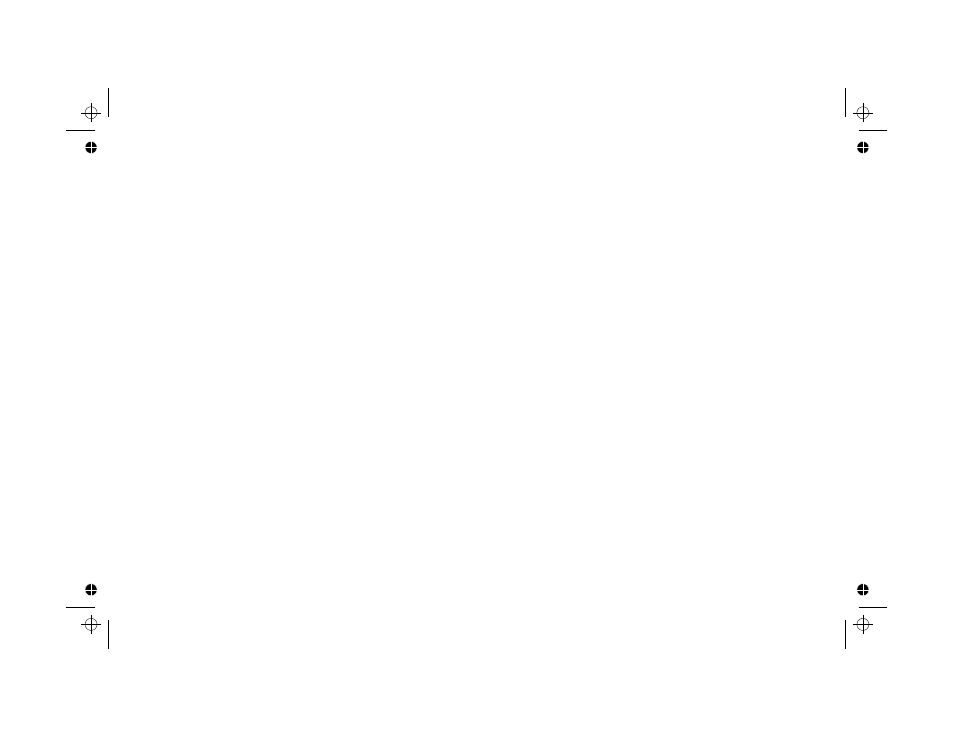
Local/Remote Setpoint Transfer Modes (SPtr)
When switching from/to Local or Remote Setpoint, the response of the
controller can be programmed to act in a variety of ways.
These responses apply to changes in setpoint mode from the controller’s
front panel, User Input or Serial communications. The table summarizes the
responses for Setpoint transfer operation:
SPtr parameter
Local to Remote
Remote to Local
nor
-
Output may bump.
Output may bump.
Auto
-
No output bump. Process
error eliminated at rate of
integral action.
No output bump. Process
error eliminated at rate of
integral action.
trAC
-
Output may bump.
Local setpoint assumes
value of Remote setpoint
(tracks). No output bump.
Note: In situations where an output bump may occur, the setpoint ramp
function (SPrP) can be used to reduce or eliminate bumping when switching
setpoint modes. The setpoint ramp feature ramps the setpoint from the old
setpoint mode to the new setpoint mode. After the initial ramp has been
completed, the active setpoint (Local or Remote) remains in the setpoint ramp
mode.
Secondary Output Power Dampening (OPd2)
The output power of the secondary loop (Internal Cascade) can be
dampened (filtered) independent of the primary loop. The secondary output
power is the actual output of the controller. The primary output power
(setpoint to the secondary) is dampened by the OPdP parameter. The
secondary output power is dampened by the OPd2 parameter.
Valve Positioner Module (8-VP)
The Valve Positioner controller must be configured to operate in either
Position Mode or Velocity Mode. Position Mode requires a slidewire
feedback signal from the valve or valve positioner. Velocity Mode does not
require a slidewire feedback signal. See
Valve Position Option,
page 58, for
an overview of valve position control.
Valve Position 1 And Valve Position 2 (VPS1, VPS2)
The full closed valve position and the full open valve position are
represented by parameters VPS1 and VPS2, respectively. These values are
expressed as a percentage of the valve open position. They do not represent
slidewire resistance. Normally, for position mode control, VPS1 = 0.0% and
VPS2 = 100.0%. In some processes, it may be necessary to limit the range
over which the controller positions the valve. In such a case, VPS1 defines the
minimum open position and VPS2 defines the maximum open position. The
controller then scales the valve position values to represent 0 and 100%
output power. In this way the valve is confined to work over a smaller portion
of its total range.
Setting both parameters to 0.0% engages velocity mode control. Slidewire
feedback is not required for velocity mode. Additionally, slightly different
controller parameters are required for this mode.
For position mode control, there are several ways to determine the valve
position values:
1) Position the valve to the closed or open positions (by use of the controller
or manually) and have the controller measure and record these positions.
To engage this mode, press the DSP button while either VPS1 or VPS2
parameters are called. %PW and DEV annunciators flash to indicate this
mode. The valve may then be positioned directly through the use of the
front panel UP and DOWN buttons. The UP button causes the valve to
move open and the DOWN button causes the valve to move closed.
Simultaneously, the controller indicates the slidewire position. After the
valve has been moved to the desired position (by use of the button and
observing the display), press PAR to record the position. This technique is
preferred because it compensates for leadwire resistance errors.
2) Use the specifications provided by the valve manufacturer. Divide the
closed and open position resistance values by the total slidewire resistance
to yield percentage values. Directly key-in the values as a percentage.
38