Red Lion GEMINI 33 User Manual
Page 19
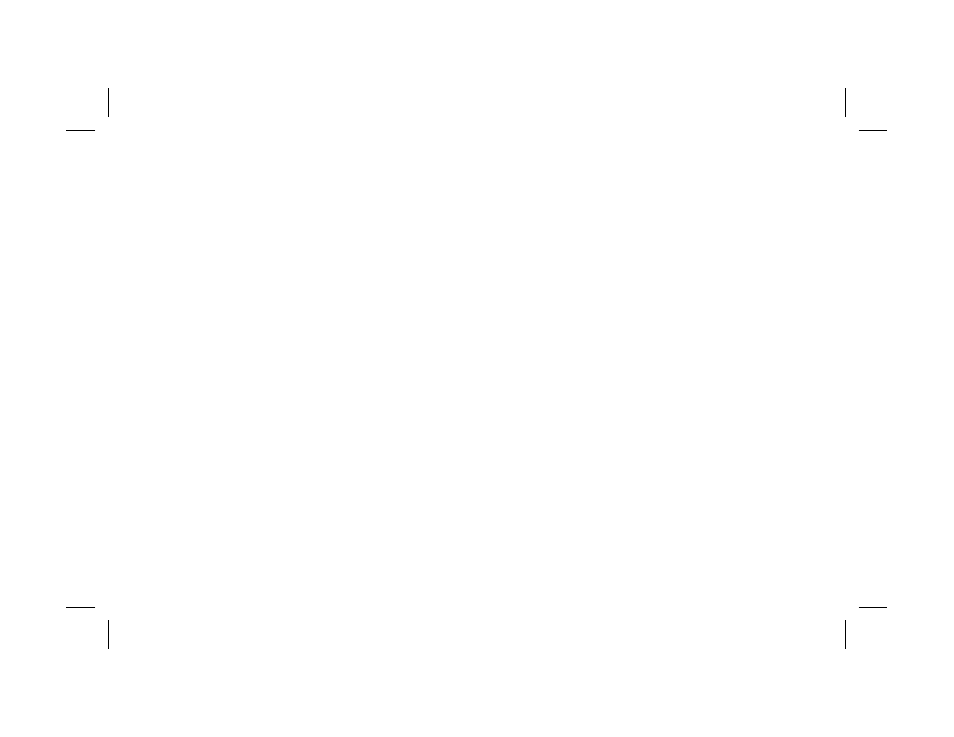
SCALING THE COUNTER
In order to scale the counter, the procedure and formulas in Appendix “E” -
“Scaling for Counting” are used.
In converting pulse units to “Display Units”, it is known that 60 pulses are
equivalent to 1 revolution of the feed roll, which is equivalent to 2.5 feet
linear travel of the wire screen. The number of “Display Units”, therefore is
2.5 and the “Number of Pulses” per 2.5 display units is 60.
STEP 1 - Calculate the Total Scaling Factor, “K
T
”, using Formula #1 of
Appendix “E”.
K
T
= Display Units/Number of Pulses
K
T
= 2.5/60 = 0.0416667
STEP 2 - Determine the Number of Count Edges, “NCE”, necessary for this
application, and calculate the Remaining Scaling required, “K
R
”, using
Formula #2 of Appendix “E”.
Since the Total Scaling Factor, “K
T
”, is less than 1, single edge counting
can be used, therefore, the Number of Count Edges, “NCE”, is 1.
K
R
= KT/NCE
K
R
= 0.0416667/1 = 0.0416667
STEP 3 - Determine the Scale Multiplier Value, “SCM”, and calculate the
Scale Factor, “SF”, using Formula #3 of Appendix “E”.
A Scale Multiplier value of 0.01 is chosen to provide the maximum number
of significant digits in the Scale Factor.
SF = KR/SCM
SF = 0.0416667/0.01 = 4.1667
HARDWARE SET-UP
The application drawing shows how the hardware for this system is to be
connected. The red, black, and white wires of the LMPC are connected to the
DC OUT, COMM., and INPUT A terminals respectively. The shield of the
LMPC cable is also connected to COMM. A remote reset button is connected
between the RST. and COMM. terminals. After the programming is
completed, a jumper is placed between the PGM.DIS. and COMM. terminals
of the Gemini 3300. This terminal, in conjunction with the “Operator
Accessible Functions” mode, will prevent accidental changes in the unit’s
operating modes. The Normally Open contact of Relay 1 is connected to the
slow down actuator and the Normally Open contact of Relay 2 is connected to
the motor control. A 12 VDC external relay (RLC # RLY10000) is used to
deactivate the motor drive control and turn on the indicator light.
DIP switch 1 is set to the logic position. This allows Input A to function as
the count input. Switch position 2 is set to SNK. (current sinking), which
provides an internal pull-up resistor to 12 VDC. Position 3 is set to HI FRQ.
because of the high count speeds involved. Position 4 is set to HI BIAS for
higher noise immunity.
In this application, the “Count with Inhibit” Inputs A & B Response mode
will be used. The application will not use the inhibit function, so Input B will
be set-up in the non-inhibiting state.
STEP BY STEP PROGRAMMING OF THE GEMINI 3300
Refer to the “Programming the Gemini 3300” section for instructions on
programming the function codes and entering the Scale Factor and Presets.
STEP 1 - Enter Code 43 (Inputs A & B Response Modes), and enter a mode
identifier of 1 (Input A = Count, Input B = Inhibit).
STEP 2 - Enter Code 44 (Number of Count Edges), and enter a 1 for single
edge counting.
STEP 3 - Enter Code 45 (Scale Multiplier), and enter a mode identifier of 3
for a Scale Multiplier of 0.01.
STEP 4 - Enter Code 46 (Decimal Point and Leading Zero Blanking), and enter
a mode identifier of 1 for no decimal points with Lead Zero Blanking.
STEP 5 - Enter Code 52 (Output 1 Termination Modes), and enter mode
identifier of 3 for terminate at start of manual reset. Output 1 is the slow down
output, which once activated, should remain so until the unit is manually reset.
STEP 6 - Enter Code 54 (Output 2 Termination Modes), and enter a mode
identifier of -3 (terminate at start of manual reset, reverse phase
operation). This mode was selected so that when the system is powered up,
the relay would be in the open condition which is motor drive off. To start
the process, the Reset button is pushed which would close the Output 2
Relay (turn on motor drive) and would stay closed until Preset 2 is reached,
at which time it would open (turn motor drive off).
STEP 7 - Enter Code 61 (Reset Button and Terminal Actuation Modes), and
enter a mode identifier of 1 (Reset Process Counter). With this mode, when
the Reset button is pushed, only the Process Counter will reset. To reset the
Batch or Total Counters, the two button reset, or Total Counter Load Value
must be utilized.
-17-