Part a system installation and start-up – KROHNE TIDALFLUX IFM 4110 PF EN User Manual
Page 7
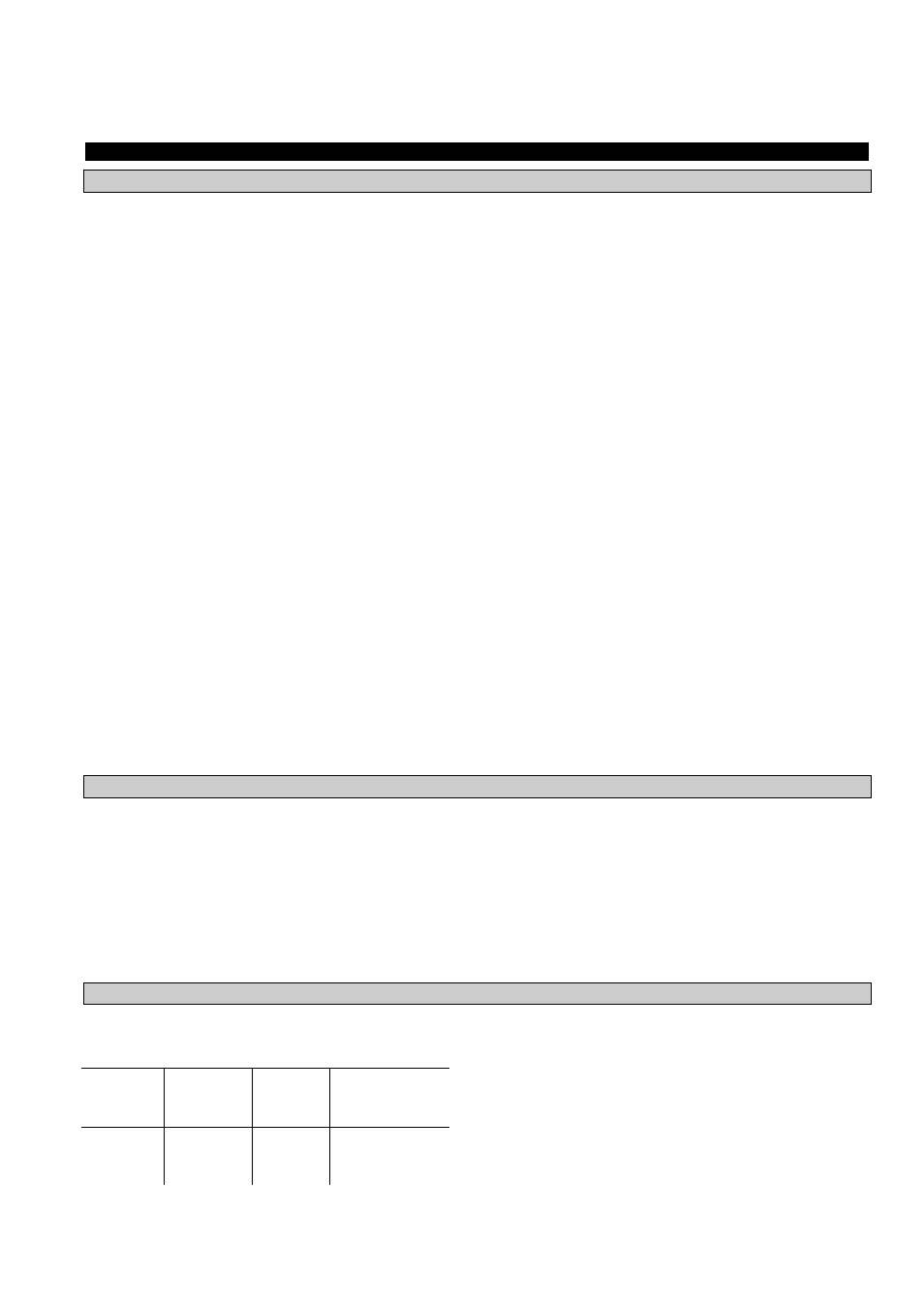
7.30830.32.00
7
Part A
System installation and start-up
1
Installation of the primary head
1.1
Selecting the installation location
1. Location and position as required, but electrode axis must be approximately horizontal. Max. deviation ± 2
°
.
2. Slope of measuring section, primary head with in- and outlet sections, is allowed to have maximum deviation of
±1% compared to horizontal.
3. Flow direction +/-, arrow on primary head must point in direction of flow.
4. Bolts and nuts: to install, make sure there is sufficient room next to the pipe flanges.
5. Vibration: support the pipeline on both sides of the flowmeter.
6. Use adapter pipes to permit axial shifting of counter flanges to facilitate installation.
7. Straight inlet run minimum of 5 x DN and outlet run minimum of 3 x DN (DN = meter size), measured from the
electrode axis. These are minimum values! Please take precautions to make sure that the flow profile inside the tube is
axially symmetric. If this is not the case, the inlet and/or outlet sections have to be increased. Also, take precautions to
minimize the amount of air bubbles in the fluid, i.e. caused by falling water in front of the primary head. Increase the inlet
section if air can not be avoided.
8. Vortex or corkscrew flow: increase inlet and outlet sections or install flow straighteners.
9. Strong electromagnetic fields and large “iron masses”: avoid in vicinity of flowmeter.
10. Zero setting is automatic in flowmeters with pulsed DC field. Electrode contamination does therefore not cause any
zero drift.
For most applications it is convenient and customary to check the zero by shutting off the flow. Shutoff valves should
therefore be provided upstream and/or downstream of the primary head unless the pipe configuration already rules out the
possibility of the primary head being drained of fluid. For zero check see section 7.1.
12 Mixing different fluid products. Install flowmeter upstream of mixing point or at an adequate distance downstream,
minimum 30 x DN (DN = meter size), otherwise output/display may be unsteady.
13 Ambient temperature < 60
°°C / 140 °°F
Refer to sect. 10.1 for process temperature and pressure limits due to material used for measuring
section/liner.
When the primary head has to be installed in direct sunlight, please install a sunshade if necessary.
14 Long pipelines. Always install control and shutoff valves downstream of flowmeter (vacuum!).
15 Pumps. Never install flowmeter on pump suction side (vacuum!).
16 Service opening. It is strongly advised to construct some kind of service opening at the top of the connecting pipeline,
just before or just after the Tidalflux. In this way it is possible to see the flow, which can be helpful if problems occur.
Also, it can be helpful to clean the liner if this gets polluted.
1.2
Grounding rings
•
Required in conjunction with electrically non-conductive pipes, i.e. synthetic, internally coated or concrete pipes. Especially
for the level measurement system special grounding rings have to be used. These rings have a cylindrical part that must go
into the connected pipelines. Therefore the inner diameter of the pipeline must be known so the grounding rings can be
made in a way they just fit in the pipeline. This is very important to keep a good flow profile of the fluid with as less
disturbances as possible.
•
Grounding rings form a conductive connection with the fluid in order to get a low-impedance connection
•
Material CrNi steel 1.4571 or SS 316 Ti-AISI, others on request.
•
For grounding and connection of the grounding rings, refer to sect. 1.4.
1.3
Torques
Bolts: tighten uniformly in diagonally opposite sequence, see table for number and type
IFS 4000 PF with Irathane liner, > 12 mm / > 0.47”:
Meter
size DN
mm
Pressure
rating [PN]
Bolts
Max. torque
Nm (ft lbf)
200
10
8x M20
68 (49.2)
250
10
12x M20
65 (47.0)
300
10
12x M20
76 (54.9)