BEI Sensors MHK5 Absolute Hollow Shaft Encoder User Manual
Page 6
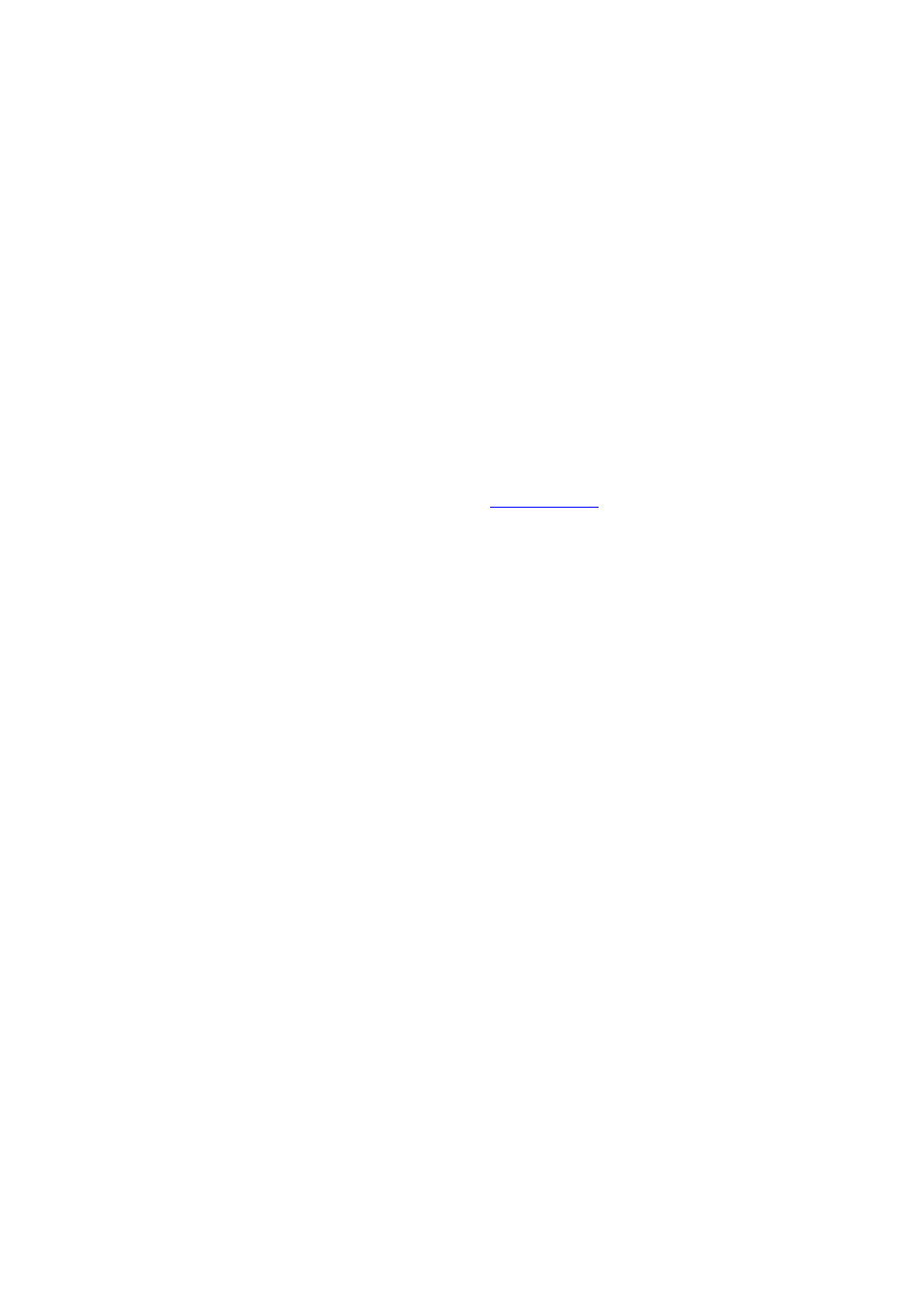
Version 07/10
BEI Sensors CANopen Manual serie M
6
the device. It is unique on a bus. The function
code varies according to the type of message
being sent:
Management messages (LMT, NMT)
Messaging and service (SDOs)
Data exchange (PDOs)
Layer Setting Services (LSS)
Predefined messages (synchronization,
emergency messages)
The absolute rotary encoder supports the
following operating modes:
Polled mode: The position value is only
given on request.
Cyclic mode: The position value is sent
cyclically (regular, adjustable interval)
on the bus.
SYNC mode: The position value is sent
after a synchronization message
(SYNC) is received. The position value
is sent every n SYNCs (n ≥ 1).
Other functions (offset values, resolution, etc)
can be configured. The absolute rotary encoder
corresponds to the class 2 encoder profile (DS
406 in which the characteristics of encoder with
CANopen interface are defined). The node
number and speed in bauds are determined via
rotary switches.
The transmission speed can range from
20kBaud up to 1Mbaud 1Mbaud (30m cable for
a maximum speed of 1Mbaud, 1000 m cable for
a maximum speed of 10 kbaud). Various
software tools for configuration and parameter-
setting are available from different suppliers. It is
easy to align and program the rotary encoders
using the EDS (electronic data sheet)
configuration file provided.
Further CAN-information is available at:
CAN in Automation (CiA) - International Users
and Manufacturers Group e.V.
Kontumazgarten 3
DE-90429 Nuremberg
(*) Reference: CAN Application Layer for
Industrial Applications
CiA DS201..207 V1.1 CAL-based
Communication Profile for Industrial
Systems
CiA DS301 CANopen Application Layer
CiA DS406 Device Profile for Encoders
We do not assume responsibility for
technical inaccuracies or omissions.
Specifications are subject to change without
notice.