Introduction, 1 general canopen information – BEI Sensors MHK5 Absolute Hollow Shaft Encoder User Manual
Page 5
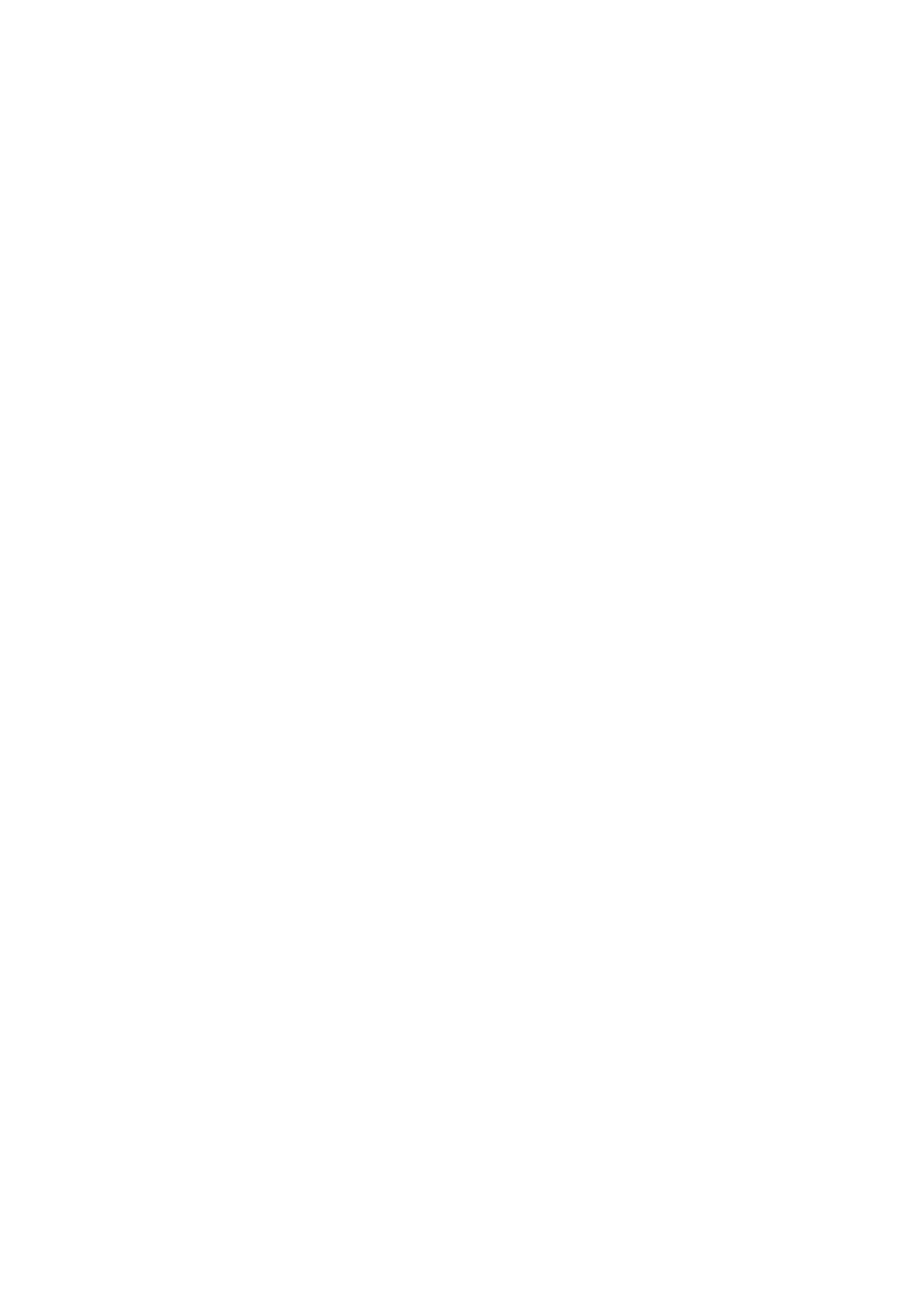
Version 07/10
BEI Sensors CANopen Manual serie M
5
1. Introduction
This manual explains how to install and
configure the OPTOCODE II absolute rotary
encoder with CANopen interface applicable for
military and industrial applications with CANopen
interface. The product is fully compliant with CiA-
standards:
DS301V402 CANopen Application Layer
DR303-1 Cabeling and connector pin assignment
DR303-3 CANopen indicator specification
DS305V200 CANopen Layer Setting Service
DS306V1R3 Electronic datasheet specification
DS406V32 Device Profile for Encoders
Measuring System
The measuring system consists of a light source,
a code disc pivoted in a precision ball bearing
and an opto-electronic scanning device. A LED
is used as a light source which shines through
the code disc and onto the screen behind. The
tracks on the code disk are evaluated by an
opto-array behind the reticle. With every position
another combination of slashes in the reticle is
covered by the dark spots on the code disk and
the light beam on the photo transistor is
interrupted. That way the code on the disc is
transformed into electronic signals. Fluctuations
in the intensity of the light source are measured
by an additional photo transistor and another
electronic circuit compensates for these. After
amplification and conversion the electronic
signals are available for evaluation.
Single-Turn
Single turn encoders specify the absolute
position for one turn of the shaft i.e. for 360°.
After one turn the measuring range is completed
and starts again from the beginning.
Multi-Turn
Linear systems normally need more than one
turn of a shaft. A single turn encoder is
unsuitable for this type of application because of
the additional requirement of the number of
turns. The principle is relatively simple: Several
single turn encoders are connected using a
reduction gear. The first stage supplies the
resolution per turn, the stages behind supply the
number of turns.
There are several types of encoder versions.
Please refer to the datasheets to find out which
is the best version for your application.
1.1 General CANopen Information
The CANopen system is used in industrial
applications. It is a multiple access system
(maximum: 127 participants), which means that
all devices can access the bus. In simple terms,
each user checks whether the bus is free, and if
it is the user can send messages. If two users try
to access the bus at the same time, the user
with the higher priority level (lowest ID number)
has permission to send its message.
Users with the lowest priority level must cancel
their data transfer and wait before re-trying to
send their message. Data communication is
carried out via messages. These messages
consist of 1 COB-ID followed by a maximum of 8
bytes of data. The COB-ID, which determines
the priority of the message, consists of a
function code and a node number. The node
number corresponds to the network address of