HEIDENHAIN iTNC 530 (60642x-03) User Manual
Page 523
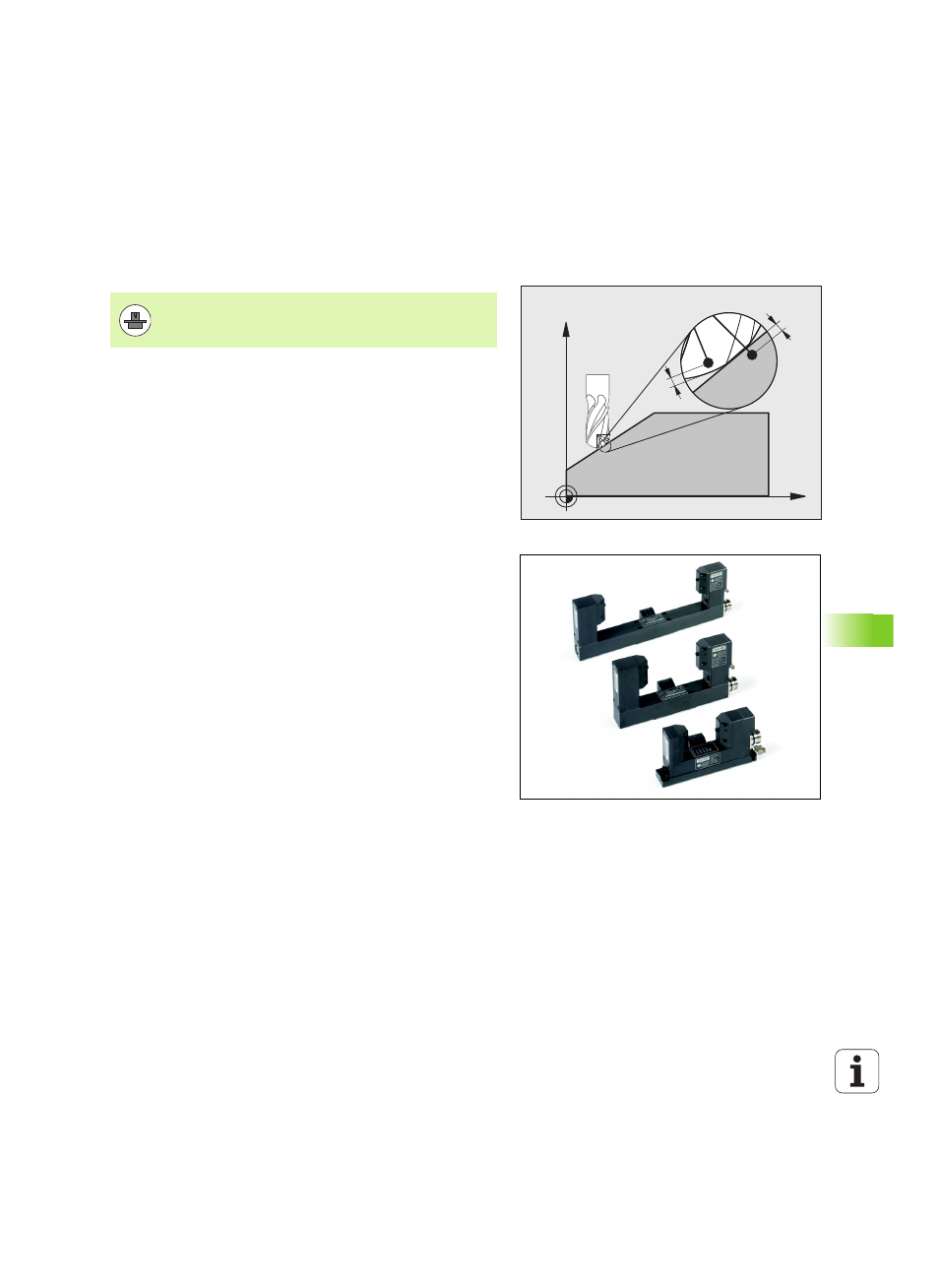
HEIDENHAIN iTNC 530
523
12.6 Thr
ee-dimensional t
o
ol compensation (sof
tw
ar
e option 2)
3-D tool radius compensation depending on the
tool’s contact angle (3D-ToolComp software
option)
The effective sphere radius of a radius cutter deviates from the ideal
form owing to the production process. The maximum form inaccuracy
is specified by the tool manufacturer; common deviations are
between 0.005 and 0.01 mm.
The form inaccuracy can be determined with a laser system and the
corresponding laser cycles on the TNC. It can then be saved as a
compensation value table. This table contains angle values and the
deviation from the nominal radius R2 measured on the respective
angle value.
The 3D-ToolComp software option enables the TNC to compensate
the value defined in the compensation value table depending on the
actual contact point of the tool.
Prerequisites
3D-ToolComp software option is enabled
Software option 2, 3-D machining, is enabled
Machine parameter 7680, bit 6 must be set to the value 1: The TNC
takes R2 from the tool table into account during tool length
compensation
The DR2TABLE column in the tool table (TOOL.T) is enabled (MP
7266.42)
The tool was measured with the laser system and the
compensation value table is available in a directory under TNC:\.
Alternatively you can also create the compensation table manually
(see "Compensation-value table" on page 524)
The tool dimensions L, R and R2 are entered in the tool table
(TOOL.T)
The path name of the compensation value table for the tool to be
compensated is entered (without file extension) in the DR2TABLE
column of the tool table (TOOL.T) (see "Tool table: Standard tool
data" on page 178)
NC program: NC blocks with surface normal vectors are required
(see "NC program" on page 526)
X
Z
DR20.004
DR2+0.002
Software option 2 is also required to be able to use
software option 92, 3-D ToolComp.