Measurement Computing ZonicBook 618E rev.3.4 User Manual
Page 20
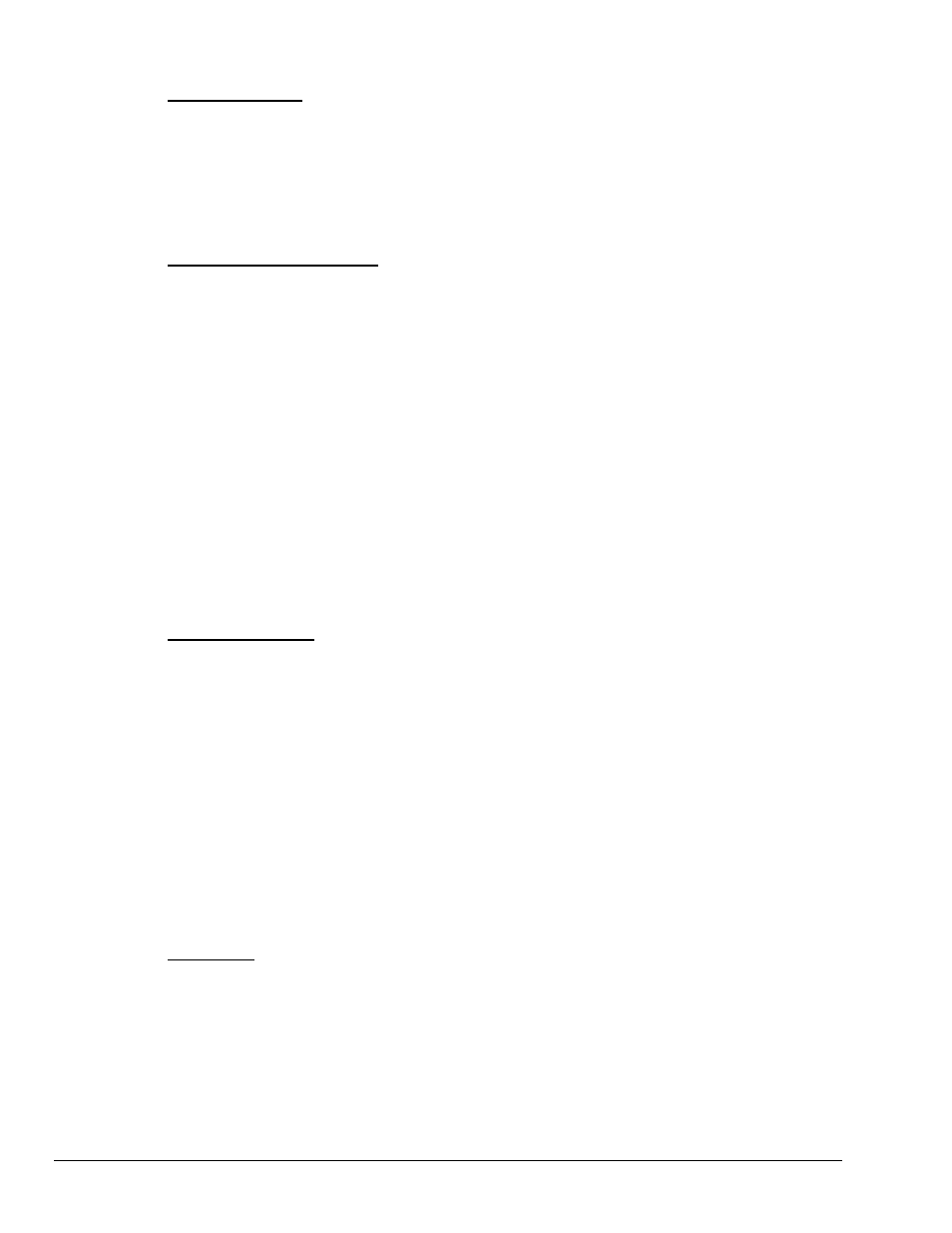
3-2 Connectors, Indicators, and Cables
918995
ZonicBook/618E User’s Manual
SOURCE OUTPUT: ZonicBook/618E includes a sine wave-based voltage source that can be set from
1 Hz to 5 kHz in discrete amplitudes ranging from 100 mVp-p to 10 Vp-p. The Source Output can be set
to either of two modes, i.e., continuous sine or sweep sine. Source Output can be used as a test source for
the input channels or as excitation for other system elements, such as the amplifier for a shaker table.
All Source Output parameters are software controlled. The output is conveniently provided on a front
panel BNC connection. Detailed information on the excitation source and its operation can be found in the
applicable eZ software documentation, e.g., the eZ-Analyst User’s Manual.
TRANSDUCER FAULT LEDS –
1 LED for each Analog Channel (CH1 through CH8)
When lit, a Transducer Fault LED indicates that the transducer for the associated channel has either an
open circuit or a short circuit. LEDs can only light when a channel has ICP “on,” as discussed in relevant
software documentation.
ZonicBook/618E’s dynamic signal conditioning circuitry provides constant current of 4mA to bias ICP
transducers. The bias current is sourced through the center conductor of the input channel BNC connector
and returns to the ZonicBook via the BNC outer conductor. The current source features an operating
compliance of 24V and is both short-circuit and over-voltage protected. Operating compliance refers to the
highest voltage that can be applied without change of the current source value. In the absence of a
transducer, the current source will output an open circuit voltage of 30V. For applications that do not
require bias, the current source can be disconnected from the input via software control on a per channel
basis.
When the current source is enabled, the input voltage is continuously monitored with level detection
circuitry. Recognition of a voltage greater than 25V (transducer open) or less than 1V (transducer short)
triggers a transducer fault condition for the affected channel. This error is communicated to the user via a
front panel LED and is also available through a software status request at the end of an acquisition. Faults
are detected and communicated when present. They are not latched. Consequently, even intermittent
faults are detected and communicated. Detection of a fault does not alter the acquisition process or its data.
OVERRANGE LEDS –
1 LED for each Analog Channel (CH1 through CH8)
When lit, an Overrange LED indicates that the associated channel’s input signal has exceeded the input
full-scale range.
Each analog channel (CH1 through CH8) is equipped with overrange detection circuitry, which is enabled
on a per channel basis. This feature indicates if data collected during an acquisition exceeded the input
full-scale range. Indication that data exceeded the range is important because overrange signals result in
clipped data that significantly corrupts FFT analysis.
The overrange error is communicated via a front panel LED and is also available through a software status
request at the end of an acquisition. When recognized, an error is latched until the commencement of a
new acquisition. Consequently, even intermittent faults are detected and communicated. An overrange
event does not stop the acquisition process or change the data.
An extension of the overrange capability could involve its integration into a process monitor application,
whereby the fault condition would be used to monitor the stability of a previously characterized dynamic
signal.
Status LEDS:
ACTIVE – Lights when a sample has been converted by the A/D Converter.
READY – Lights when software accesses the unit.
POWER – Lights when power is turned on and is present.