Service, Refrigerant circuit, Troubleshooting – Carrier 38AH044-134 User Manual
Page 44: Compressor motor protection
Attention! The text in this document has been recognized automatically. To view the original document, you can use the "Original mode".
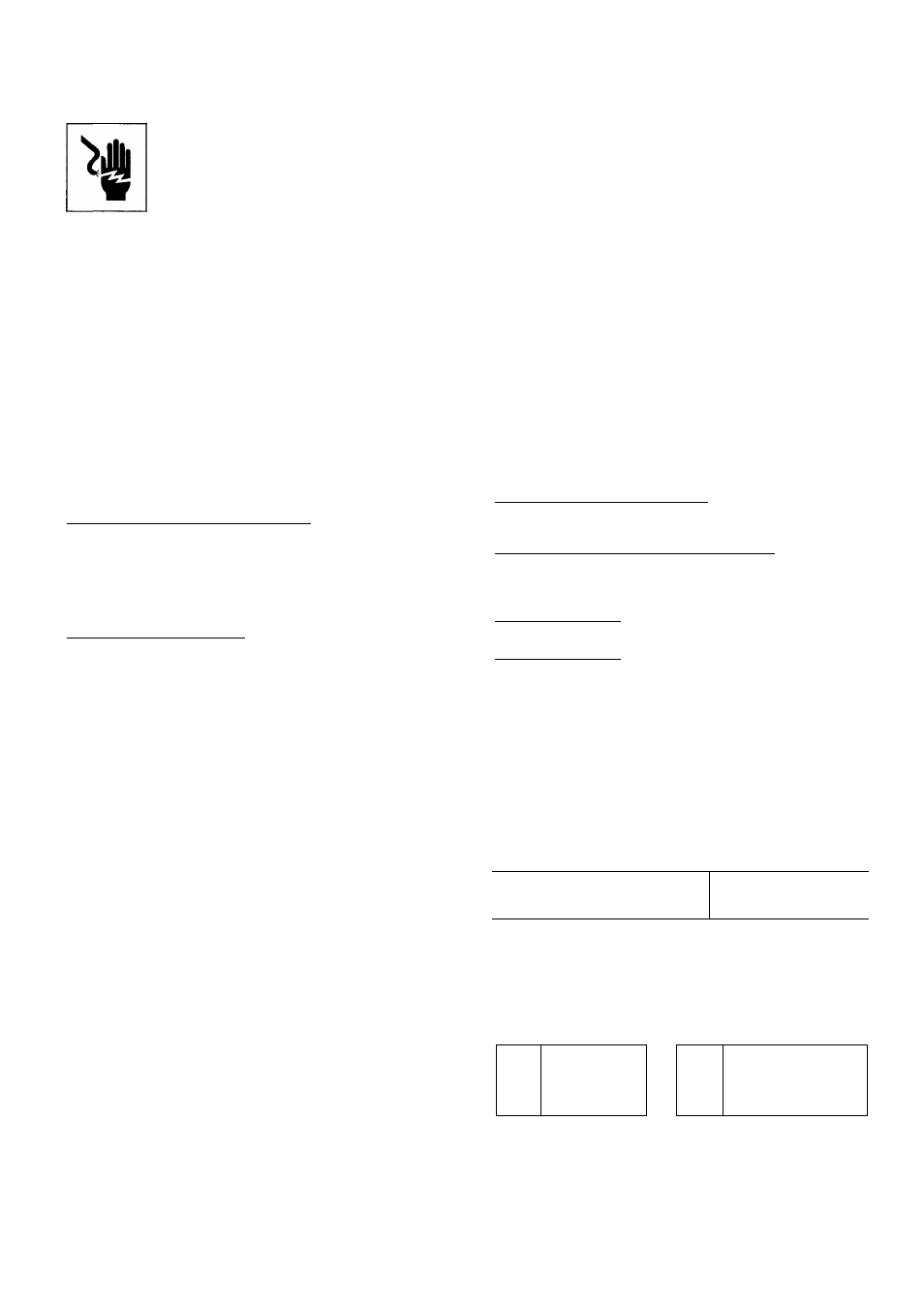
SERVICE
ELECTRIC SHOCK HAZARD
Turn off all power to unit before servicing.
The ON-OFF switch on control panel
does not shut off control power; use field
disconnect.
Coil Cleaning — Clean the colls with a vacuum cleaner,
compressed air, water, or a non-wire bristle brush.
Refrigerant Circuit
LEAK TESTING — Units are shipped with a holding charge
of R-22 (see Table 3A, 3B, 4A, or 4B) and should be under
sufiScient pressure to conduct a leak test. If there is no pres
sure in the system, introduce enough nitrogen to search
for the leak. Repair the leak using good refrigeration prac
tices. After leaks are repaired, system must be evacuated and
dehydrated using methods described in GTACII, Module 4,
System Dehydration.
REFRIGERANT CHARGE (Refer to Table 3A, 3B, 4A, or
4B) — At the liquid line connection point on each circuit is
a factory-installed liquid line service valve. On each
valve is a lA-in. Schrader connection for charging liquid
refrigerant.
Charging with Unit Off and Evacuated — Close liquid line
service valve before charging. Weigh in charge shown in Table
3A, 3B, 4A, or 4B. Open liquid line service valve; start unit
and allow it to run several minutes fully loaded. Check for
a clear sight glass. Be sure clear condition is liquid and not
vapor. Complete charging the unit in accordance with Start-
Up, Adjust Refrigerant Charge, page 39.
Charging with Unit Running — If charge is to be added while
unit is operating, it is necessary to have all condenser fans
and compressors operating. It may be necessary to block con
denser coils at low-ambient temperatures to raise condens
ing pressure to approximately 280 psig (1931 kPag) to turn
all condenser fans on. Do not totally block a coil to do this.
Partially block all coils in uniform pattern. Charge
vapor into compressor low-side service port located above
oil-pump crankshaft housing. Charge each circuit until sight
glass shows clear liquid.
Troubleshooting —
cated at back of book.
Refer to Troubleshooting chart lo-
Oil Pressure Safety Switch (OPS) — An oil pres
sure safety switch for each of the independent refrigerant
circuits shuts off the compressor in that circuit if oil pressure
is not established at start-up or maintained during operation.
If the OPS stops the unit, determine and correct the cause
before restarting the unit. Failure to do so constitutes equip
ment abuse and could affect the warranty.
Compressor Motor Protection
CIRCUIT BREAKER — A manual reset, calibrated trip cir
cuit breaker for each compressor protects against overcur
rent. Do not bypass connections or increase size of circuit
breaker for any reason. If trouble occurs, determine the cause
and correct it before resetting the breaker.
DISCHARGE GAS THERMOSTAT — A sensor in the
cylinder head of each compressor (Fig. 29) shuts down the
compressor if excessively high discharge gas temperature is
sensed. If the discharge gas thermostat shuts the unit down,
it may be reset by the thermostat or power disconnect switch.
CRANKCASE HEATER (See Fig. 29) — Each compressor
has an electric crankcase heater located in the bottom cover.
The heater is held in place by a clip and bracket and must be
tightly connected since exposure to the air causes the heater
to burn out. Each heater is wired into the compressor control
circuit through a relay which energizes only when the com
pressor is off. The heater keeps the oil at a temperature that
prevents excessive absorption of refrigerant during shut
down periods.
Energize the crankcase heaters when the unit is not run
ning exeept during prolonged shutdown or servicing. Ener
gize the heaters at least 24 hours before restarting the unit
after prolonged shutdown.
TIME GUARD® FUNCTION — This function prevents com
pressors from short-cycling.
Fan Motor Protection — Fan motors are protected
by a single circuit breaker for all motors.
Head Pressure Control — Head pressure control re
duces condenser capacity under low-ambient conditions. This
is achieved by fan cycling control (standard, all units) and
Motormaster® III control accessory (field installed).
FAN CYCLING —All condensing units have standard pro
vision for fully automatic intermediate season head pressure
control through fan cycling (see Table 17).
38AH044-Q84 Dual-Circuit Units — Fans no. 3 and 4 are
cycled by pressure control on all units. On 38AH074 and
084, fans no. 5 and 6 are also cycled by pressure control.
38AHQ44-084 Optional Single Circuit Units — Fans no. 3
and 4 are cycled by pressure control on all units. On 38AH074
and 084, fans no. 5 and 6 are cycled by an air-temperature
switch located in the bottom shelf of the control box.
Units 38AH094.104 — Fans no. 3 through 6 are cycled by
pressure control.
Units 38AH124.134 — Fans no. 3 and 4 on each unit mod
ule are cycled by pressure control. On module 134B only,
fans no. 5 and 6 are cyeled by an air-temperature switch lo
cated in the bottom shelf of the control box.
Pressure control is achieved via a fan cycling pressure switch
located on the cylinder head of the unit or circuit lead com
pressor (see Fig. 29).
The air-temperature switch used to control fans no. 5 and
6 on 38AH074,084 optional single-circuit units and on mod
ule 134B is closed and cycles the fans on when the ambient-
air temperature is above 70 F (21 C).
Table 17 — Fan Cycling Control — Psig (kPag)
Control by Pressure*
±7 (48)
Switch Opens
126 (869)
Switch Closes
264 (1820)
*On all units, fans no. 3 and 4; also on unit 38AH074, 084 (dual
circuit units only) and 38AH094,104, fans no 5 and 6.
NOTE; Fans no. 1 and 2 are noncycling Units 38AH074,084 optional
single-circuit units and module 134B fans no 5 and 6 are
cycled by an air-temperature switch which operates above 70 F
(21 C) ambient-air temperature
_l
О
© О
o“
Ü
0 0
_i
о
© © ©
o“
Ü
© © ©
38AH044-064,
Modules 124A, 124B,
134A
38AH074-104,
Module 134B
44