0 gas heat section maintenance, Rdcb, rdcc, rddb, rddc -30, 1 heat exchanger, burner, and venter – Reznor MAPS - A,B,C Users Manual User Manual
Page 21: 1 heat exchanger, burner, and venter maintenance
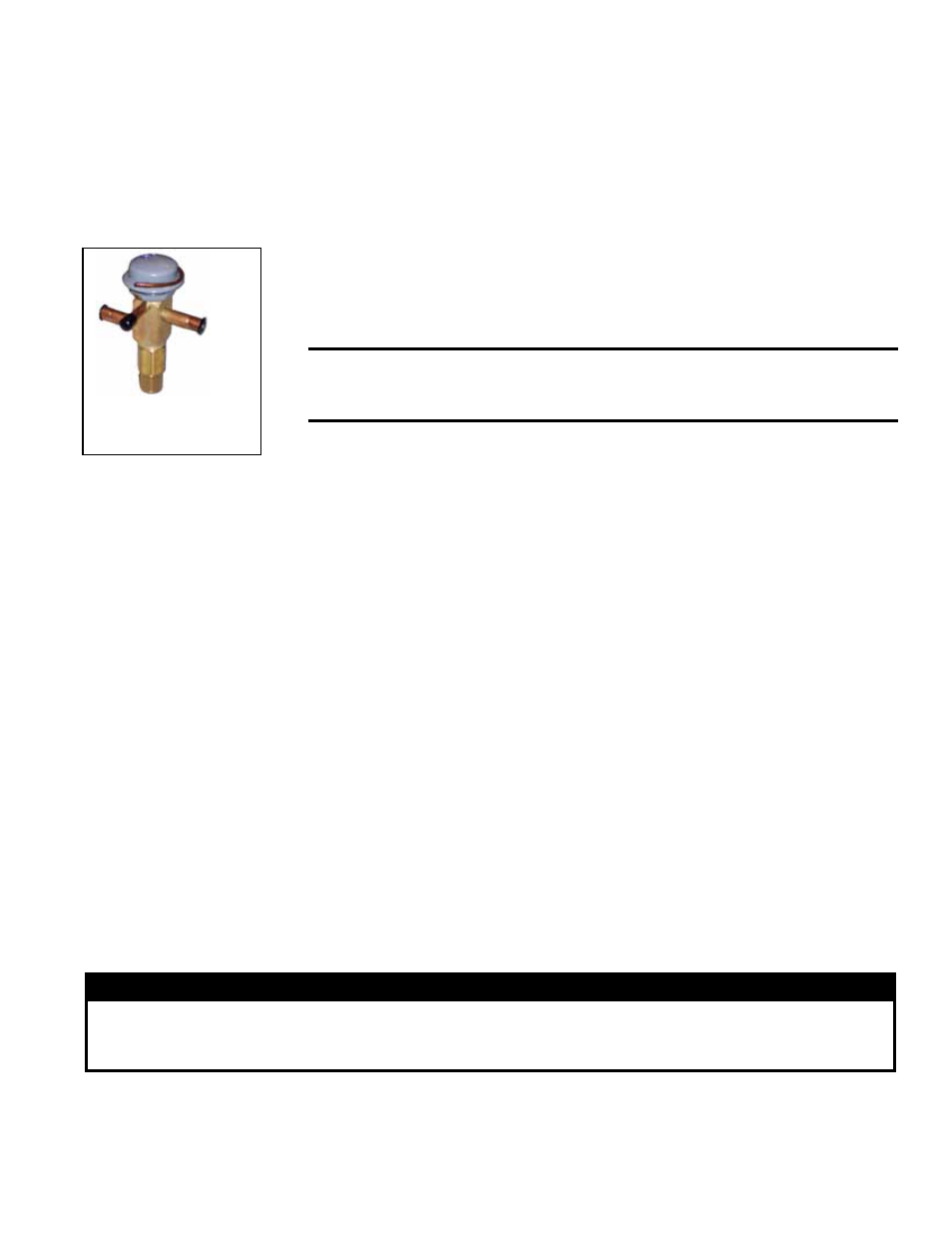
Form O-MAPSIII&IV Cabinets A/B/C, P/N 257004R8, Page 21
Function: The hot gas bypass valve allows some of the refrigerant gas from the suc-
tion line to be re-routed directly to the evaporator coil providing for expanded compres-
sor modulation at low outside air temperatures.
Service: To check the hot gas bypass valve setting, connect a pressure gauge to the
suction line and block the entering air to the evaporator coil. Suction pressure will drop,
and the hot gas bypass valve should begin to open at a approximately 115 psi and will
be fully open at 95 psi. When the valve begins to open it will be hot to the touch (see
caution below).
CAUTION: Touching the operating hot gas bypass valve can cause
a burn. Use caution when checking and adjusting the valve. See
Hazard Levels, page 3.
If a hot gas bypass valve needs to be replaced, use only a factory-authorized replace-
ment for R410-A refrigerant. All refrigerant service should be done by a qualified R410-A
service technician.
3.9.5 Hot Gas Bypass
Valve (Option AUC9)
3.9.4 Voltage
Protection,
Option PL4
Function: Phase loss and low or high voltage can cause damage to electrical com-
ponents. This safety control monitors phase loss and voltage and shuts down the unit
when its limits are exceeded. The device is auto reset and allows the unit to restart
when the power conditions are corrected.
FIGURE 9 - Hot
Gas Bypass Valve
3.9.6 Modulating
Reheat (Option
AUR1) - RDB, RDC,
RDDB, RDDC, REDB,
REDC
Function: Units with modulating reheat control (Option AUR1) have a temperature
control board with a potentiometer, an air temperature sensor, and an electric dis-
charge bypass valve. When reheat is active, the sensor monitors the air temperature
as it leaves the reheat coil. Based on the potentiometer setpoint, the board will open
or close the bypass valve. If the leaving air temperature is higher than the setpoint, the
board will open the valve adding refrigerant hot gas to the refrigerant liquid before it
enters the pre-cool coil. This reduces the coil's ability to absorb the heat, and thus, the
reheat coil's ability to reject. If the leaving air temperature is lower than the setpoint,
the opposite occurs.
Service: Check the wiring connections at the board. The board is polarity sensitive;
positive connects to terminal 1 and negative to terminal 2.
The valve may be tested by measuring the resistance of the leads. Remove the power
and the leads from the board before testing. Resistance between the black and white
leads should be about 75 Ohms. Resistance between the green and red leads should
be within 5% of the white and black.
Use only factory-authorized replacement parts.
4.0 Gas Heat
Section
Maintenance -
Models RDCB,
RDCC, RDDB,
and RDDC
This gas heater will operate with a minimum of maintenance. To ensure long life and
satisfactory performance, a heater that is operated under normal conditions should be
inspected and cleaned at the start of each heating season. If the heater is operating in
an area where an unusual amount of dust or soot or other impurities are present in the
air, more frequent maintenance is recommended.
When any service is completed, be careful to reassemble correctly to ensure that no
unsafe conditions are created. When re-lighting, always follow the lighting instructions
on the furnace.
This gas heat section is equipped with a
T
CORE
2
®
style heat exchanger and burner.
Inspect the gas heat section annually to determine if cleaning is necessary. If there is
an accumulation of dirt, dust, and/or lint, clean the compartment.
4.1 Heat Exchanger,
Burner,
and Venter
Maintenance
If a VFD needs to be replaced, contact the factory service department. Be prepared to
provide the model, serial, and wiring diagram number.
WARNING
Turn off the power before performing maintenance procedures. Lock disconnect switch in
OFF position. When you turn off the power supply, turn off the gas at the external manual
valve. See Hazard Levels, page 2.