0 maintenance/ service procedures (cont'd), 6 compressor maintenance (cont'd) – Reznor MAPS - A,B,C Users Manual User Manual
Page 18
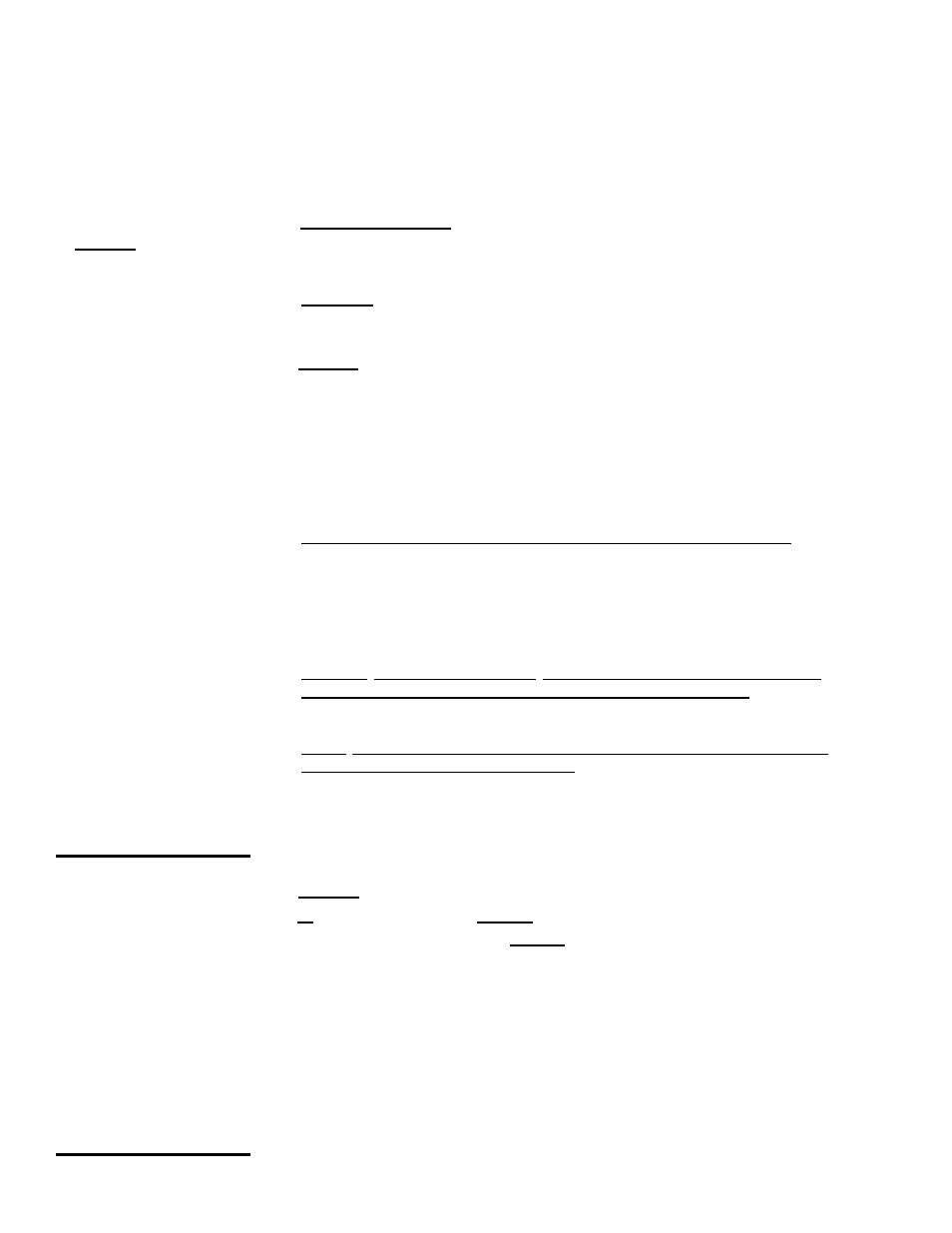
Form O-MAPSIII&IV Cabinets A/B/C, Page 18
Record the ambient temperature. Adjust the system controller so that a call for
cooling exists.
NOTE: Outdoor ambient lockouts may prevent mechanical cooling. Temporarily
override lockouts by lowering the cooling setpoint. When testing is complete, reset
the controller.
Because it is possible to unknowingly connect 3-phase power in such a way
as to cause the scroll compressor or blower to rotate in reverse, it is very
important to check this on startup.
Check Compressors - Immediately at startup, observe the gauges. If the
suction pressure rises and discharge pressure drops, the compressor is
operating in reverse and must be shut down. Turn off the power and switch
the 3-phase line voltage wiring connections before restarting the unit.
Important: If allowed to operate for several minutes in reverse, the compressor’s
internal protector will trip. If a compressor is repeatedly allowed to restart and run
in reverse, the compressor will be permanently damaged.
•
Step 11. Check Subcooling and Superheat
Superheat is the verification that the evaporator coil is properly using the
refrigerant supplied. Too much superheat indicates that the coil is undercharged.
Too little superheat indicates that the coil is overcharged and potentially flooding
liquid refrigerant to the compressor.
Subcooling is the measurement of liquid refrigerant stored in the condenser
coil. Too much subcooling indicates a system overcharge. Too little subcooling
indicates a system undercharge and may not provide the thermal expansion valve
with a full column of liquid refrigerant for proper operation.
Two important requirements before checking superheat and subcooling:
1) This unit has fully intertwined refrigerant circuits and each circuit MUST be
isolated before measuring its temperature. Another active circuit will influence the
reading and make it impossible to determine accurate superheat and subcooling.
2) If the circuit is equipped with an optional hot gas bypass valve, the valve must
be disabled before measuring superheat and subcooling. Method of disabling
depends on the model and date of manufacture.
All MAPS
®
IV Models & any MAPS
®
III Models with a shutoff valve in the line
between the compressor discharge and the hot gas bypass valve - Locate the
shutoff valve. Disable the hot gas bypass valve by closing the shutoff valve. When
measurements are complete, be sure to open the valve.
MAPS
®
III Models without a shutoff valve in the line between the compressor
discharge and the hot gas bypass valve - Disable the hot gas bypass valve by
removing the cover and adjusting the spring tension counterclockwise until the
spring tension is relieved.
Count and record the number of turns required so
that you can return the bypass valve to its original setting. To check setting, refer
to Paragraph 3.9.5.
3.6 Compressor
Maintenance
(cont'd)
•
Step 10. System
Startup (cont'd)
3.0 Maintenance/
Service
Procedures
(cont'd)
I
MPORTANT: Do not
release refrigerant
to the atmosphere!
If required service
procedures
include the adding
or removing of
refrigerant, the
qualified HVAC
service technician
must comply with
all federal, state or
provincial, and local
laws.
Follow the procedures in Paragraph 3.5 to check subcooling and superheat.
•
Step 12. (Select the procedure that applies.)
IF the oil measured in Step 2 was significantly less than in the table on
page 14 or the acid test in
Step 2 indicated a burnout, do the following:
a) Operate the unit for several hours. Check the pressure drop through the
temporary suction line filter drier. If the pressure drop exceeds 8 psig, recover
the refrigerant, replace the suction line filter drier with the same type as
removed, replace the liquid line filter drier, evacuate the circuit, and re-charge
with the recovered refrigerant.
Continue to monitor the pressure drop through the suction line filter drier and
repeat the process above until the pressure does not exceed 8 psig after
several hours of operation. (
NOTE: System must be allowed to run no more
than 72 hours with a suction line filter drier.)
b) Allow the system to operate for 4-8 hours. Recover the refrigerant and take an
oil sample. Retest the oil for acid.
NOTE: To identify MAPS
®
III
and MAPS
®
IV Models, see
Paragraph 1.0.