Reznor MAPS III, Cabinet D RECB Users Manual User Manual
Page 42
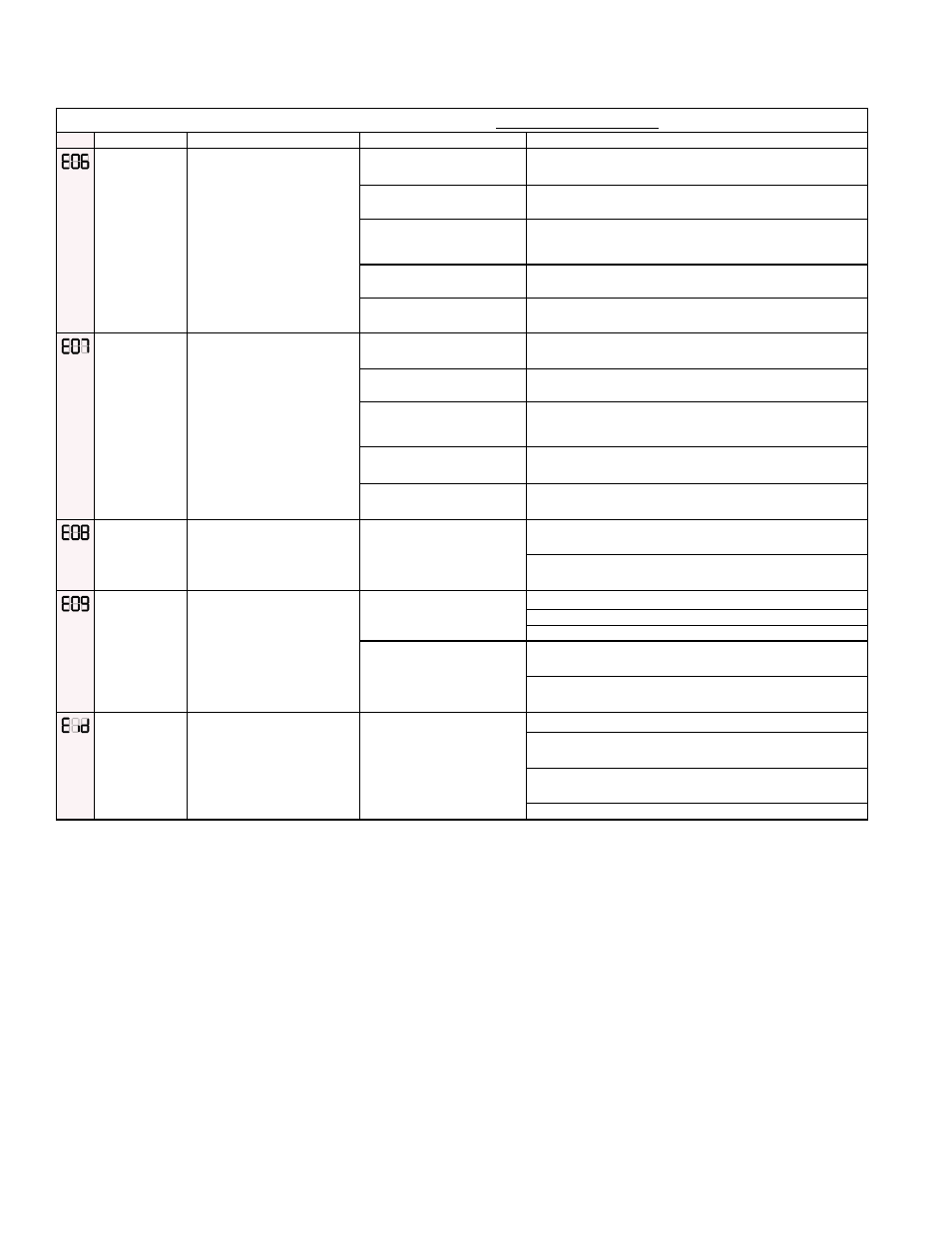
Form O-MAPSIII Cabinet D, P/N 222918R9, Page 42
Gas Heat Section Modulating Control LOCKOUT ERRORS (ccont'd)
Code
Alert
Description
Probable Causes
Solutions
Gas Sensor
Failure (EO6)
Pressure
Sensor
Reading Low
The gas transducer reading
is too low compared to
the expected value for the
modulating gas valve actuator
position.
When the furnace is operating
at 75% or higher -- greater
than 8 VDC analog input
voltage - the manifold
pressure sensor must read
1.4" w.c. or higher
A. Modulating actuator/ball
valve not properly aligned
1 Perform modulating system gas valve alignment
procedure; see Paragraph 4.3.
B. Line pressure too low
1. Ensure line pressure is properly adjusted for the gas and
application. Correct as needed.
C. Intermediate regulated
pressure to low
1. Ensure the safety gas valve(s) are properly adjusted
to the specified outlet pressure. Adjust per the installation
instructions as necessary.
D. Wrong gas pressure
sensor installed.
1. Ensure the proper gas transducer - either natural gas or
propane - is installed. Replace as needed.
E. Gas pressure sensor
faulty
1. Ensure gas manifold transducer is installed properly and
wired per the unit wiring diagram. Replace as necessary.
Gas Sensor
Failure (EO7)
Pressure
Sensor
Reading High
The gas transducer reading
is too high compared to
the expected value for the
modulating gas valve actuator
position.
When the furnace is operating
at 75% or lower - less than 8
VDC analog input voltage --
the manifold pressure sensor
must read 2.8" w.c. or lower.
A. Modulating actuator / ball
valve not properly aligned
1. Perform modulating system gas valve alignment
procedure; see Paragraph 4.3.
B. Line pressure too high
1. Ensure the line pressure is properly adjusted for the gas
and application. Correct as necessary.
C. Intermediate regulated
pressure too high
1. Ensure the safety gas valve(s) are properly adjusted
to the specified outlet pressure. Adjust per the installation
instructions as necessary.
D. Wrong gas pressure
sensor installed
1. Ensure gas sensor -- either natural or propane -- is
installed. Replace as necessary.
E. Gas pressure sensor
faulty
1. Ensure gas sensor is installed properly and wired per the
unit wiring diagram. Replace as necessary.
Improper Flame
Signal (EO8)
Control senses flame present
when the gas valve is
commanded off.
A. Flame remains lit in “Off”
cycle
1. Gas valve leaks - check wiring to remove continuous 24V
to gas valve.
2. Gas valve is stuck open – remove, repair, or replace gas
valve.
No Firing Rate
Input (EO9)
Call for heat is sensed (R & W
closed) but firing rate is below
defined voltage threshold for
furnace operation.
A. Faulty wiring into the
“Analog +” and “Analog –“
terminals
1. Ensure wiring is connected per unit wiring diagram.
2. Check for loose pins or bad connections.
3. Check for frayed wiring or shorts to ground.
B. No signal from source.
1. Check firing rate input voltage – must be greater than 1.5
VDC.
2. Troubleshoot controller providing firing rate input to the
deep modulation ignition control board.
Invalid I.D. Plug
(Eid)
The installed I.D. plug is not
valid for this control board.
A. Incorrect I.D. plug installed 1. Ensure I.D. plug is correct for the furnace – check label.
2. Ensure I.D. plug is properly inserted into the mating
connector on the control board.
3. With the I.D. plug installed, cycle power to the furnace.
The board will display the I.D. plug identity upon power-up.
4. Install correct I.D. plug as needed.
6.2 Troubleshooting Heat Section (cont'd)
6.2.2.2 Troubleshooting the Modulating Gas Control (cont'd)