Response time of encoder monitoring, Safety engineering – Lenze E94AYAE SM301 User Manual
Page 109
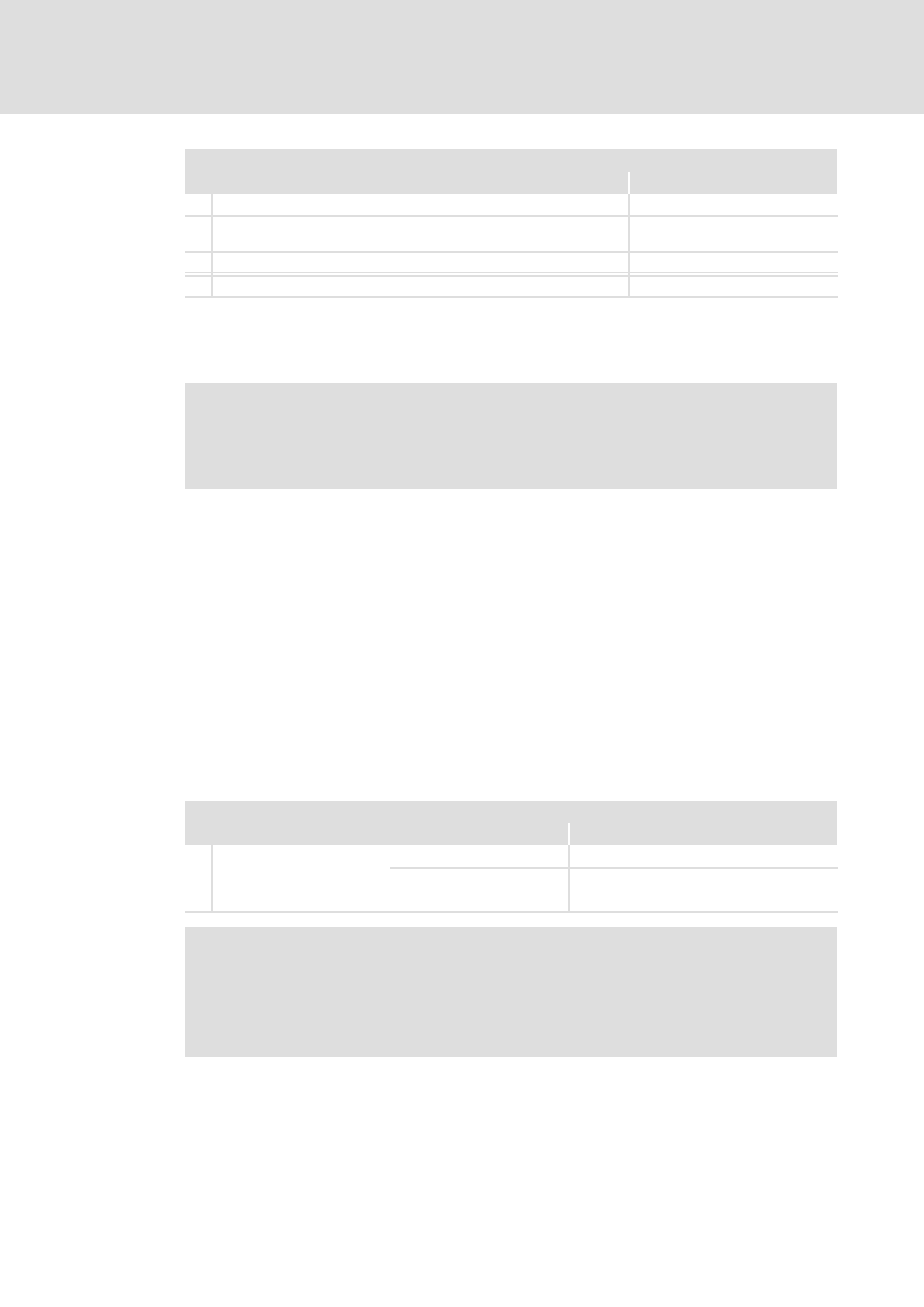
Safety engineering
Response times
Response time of encoder monitoring
l
109
EDS94AYAE EN 7.0
Response time to a PROFIsafe control word (PROFIsafe output data)
[ms]
t
4
Processing time in the safety PLC
must be calculated
t
Ps
PROFIsafe cycle time
according to manufacturer
information
t
5
Processing time in drive−based safety
14
Safety function starts after ...
S
Tab. 1−23
Response time in case of PROFIsafe request
Information on how to calculate the processing time and transmission time of the
PROFIsafe can be found in the documentation of the safety PLC used.
)
Note!
When the PROFIsafe communication is disturbed, it is changed to the fail−safe
state after the PROFIsafe monitoring time (F_WD_Time) has elapsed
(
¶ Tab. 1−17). The PROFIsafe communication is passivated.
Example
ƒ
After an event has occurred at a safe input, the message is fed back to drive−based
safety via the safety PLC.
ƒ
Drive−based safety activates a safety function.
ƒ
Hence, the maximum response time to the event is calculated as follows:
t
max response
= t
1
+ t
2
+ t
3
+ max {t
WD
; t
PS
+ t
4
+ t
Ps
+ t
5
}
When calculating the maximum response time, include the times of the safety functions,
e.g. in case of SS1 the stopping time (C15305) until STO is active.
1.8.4
Response time of encoder monitoring
Response time of encoder monitoring
[ms]
Time required to detect
faults due to continuous
signal errors at the encoder
interface.
12
(As of SM301 V1.2)
can be parameterised under
C15410
12/50/100
)
Note!
The minimum response time must be individually determined for each system.
A longer response time leads to an increased system availability, if, for
instance, during machine set−up with safe operating stop process−related
speed jumps occur for a short time.