Chapter 12: sensors, i/o and events, 1 modulo counting, Chapter 12: sensors, i/o and events -1 – ElmoMC SimplIQ Software Manual User Manual
Page 186: 1 modulo counting -1
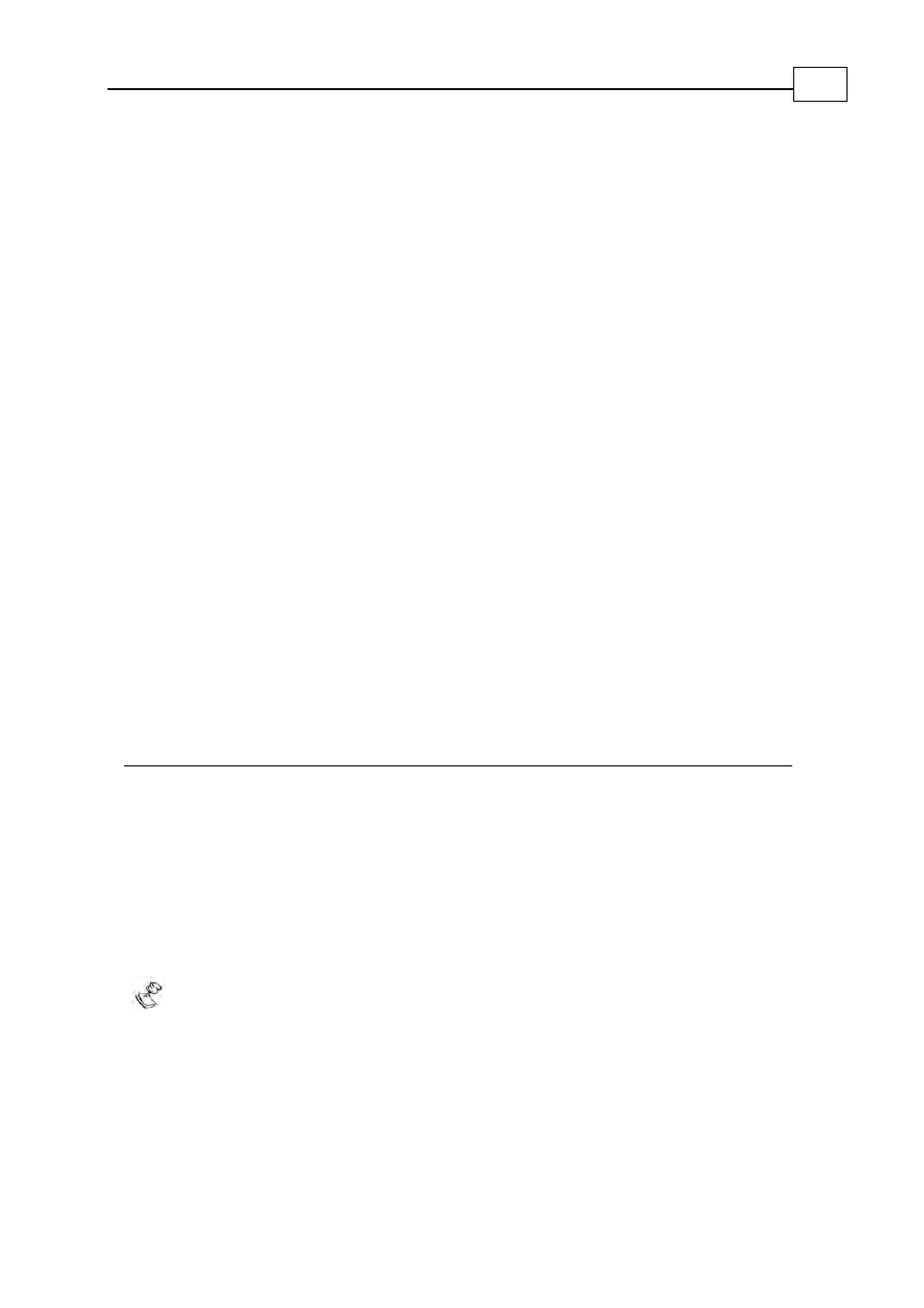
SimplIQ
Software Manual
MAN-SIMSW (Ver. 1.4)
12-1
Chapter 12: Sensors, I/O and Events
SimplIQ
drives have two encoder inputs for feedback, commutation and auxiliary
reference generation. It also includes an analog input, Hall sensor inputs and digital I/O.
The digital inputs and encoder index signals can generate events that register motor
position, reload the position counter, flag a digital output or call a special user program.
The digital outputs respond to software events, such as affirmation of conditions to start
the motor or brake activation upon starting or shutting the motor.
12.1 Modulo Counting
The PX variable counts the main position sensor. It is limited to the range [-10
9
…10
9
]. For
limited motions, this range is acceptable; however, certain applications require the motor
position to be counted cyclically. When a top position is reached, the position counter
“rolls over” and counting continues from the bottom position.
The most common examples of modulo counting are rotary pointing equipment such as
radar pedestals, camera pointers or rotary robot axes. In this type of equipment, the
position is normally counted modulo the mechanical rotation of the load. When the load
points in a given direction, the encoder readout is always the same, no matter how many
full rotations have been made.
The
SimplIQ
drive counts position cyclically; all software position modes handle cyclical
position counting. Point-to-point position motions always go the short way around.
The commands relevant to modulo counting are:
Command Description
XM[N]
Modulo count limits for main position counter. Main position
counting range is [XM[1]…XM[2]].
YM[N]
Modulo count limits for auxiliary position counter. Auxiliary position
counting range is [YM[1]…YM[2]].
RM
Reference mode. Must be 0 (do not use auxiliary reference generator) if
modulo counting is used. More details available in
Chapter 12.
Table
12-1: Commands Relevant to Modulo Counting
If the modulo value is selected low and the sensor speed is high, more than one full
revolution of the position counter may elapse within a single sampling time. This
will cause the position counter to behave in an unpredictable manner.
Directional limit switches or software motion limits (HL[3], LL[3], VH[3] and VL[3])
should not be placed near the position folding point, as illustrated in the following
example:
UM=5
, speed is 1000,000 counts/second, TS=75, XM[1]=0, XM[2]=1000, HL[3]=980