3 optimizing the controller sampling time, 3 optimizing the controller sampling time -4 – ElmoMC SimplIQ Software Manual User Manual
Page 100
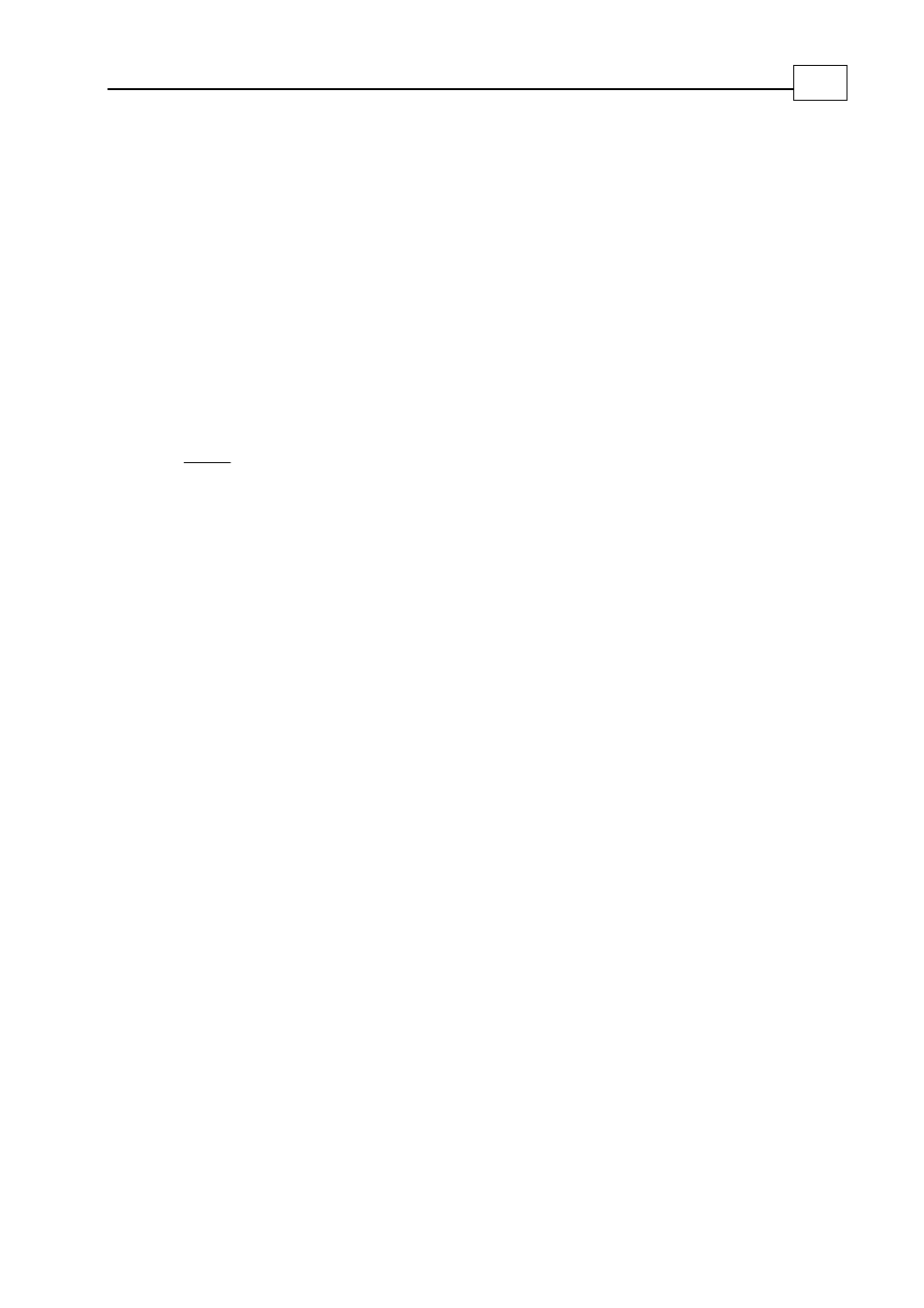
SimplIQ
Software Manual
Development Aids
MAN-SIMSW (Ver. 1.4)
7-4
7.3
Optimizing the Controller Sampling Time
Selecting a controller sampling time is a compromise between the following:
Possible control bandwidth
Maximum rate of CAN message acceptance
Maximum communication baud rate
Minimum latency for interpreter response
Maximum user program speed
The smaller the sampling time, the better the control performance. For mechanically ideal
plants, the achievable speed controller bandwidth (with reasonable gain and phase margins)
is approximately:
12000
BW
TS
=
which is approximately 120 Hz for a sampling time of 100 microseconds, and 170 Hz for a
sampling time of 70 microseconds. The bandwidth increases slightly with the closure of the
position loop.
For a low sensor resolution (speed always below 10,000 counts/second) or for moderate
control performance requirements, a larger sampling time is tolerable. For extreme control
performance, decrease the sampling time.
A lower sampling time implies a higher RS-232 baud rate. The
SimplIQ
drive can always
operate at a baud rate of 57,600, while it can operate at a baud rate of 115,200 for TS=80 or
less. Lower sampling times also imply that a larger number of CAN messages can be sent to
the
SimplIQ
drive without loss. The maximum continuous CAN message acceptance rate is
one message per 4 TS (bursts of up to eight messages can be accepted at the full CAN bus
rate of 1 Mbaud/second). However, lower sampling times imply a greater CPU load, which
causes the interpreter and the user program to operate at a slower rate. The “interpreter”
includes the RS-232 interpreter, CAN SDO handling and CAN receive PDO (other than
CAN high-speed motion commands) handling.
The CPU load is not only a function of the sampling time. DC motors consume less CPU
load than brushless motors. UM=4 and 5 loads the CPU the most, while UM=2 loads it less
and UM=1 and 2 the least. The specific design of the controller and sensor filters also affects
the CPU load.
An extreme CPU load (not likely at TS-70 unless a very large control filter is being
implemented) can cause a real-time overflow in the
SimplIQ
drive; it can be corrected by
setting TS to a new value.
The WI[7] command tests for the CPU load and reports the percentage of CPU power
remaining for the interpreter and the user program. A value no smaller than 25 is
recommended for WI[7]. In order to use a smaller WI[7] value, the sampling time should be
increased.