Chapter 8: commutation, 1 general description, 1 dc brush motors – ElmoMC SimplIQ Software Manual User Manual
Page 111: Chapter 8: commutation -1, 1 general description -1, Dc brush motors -1
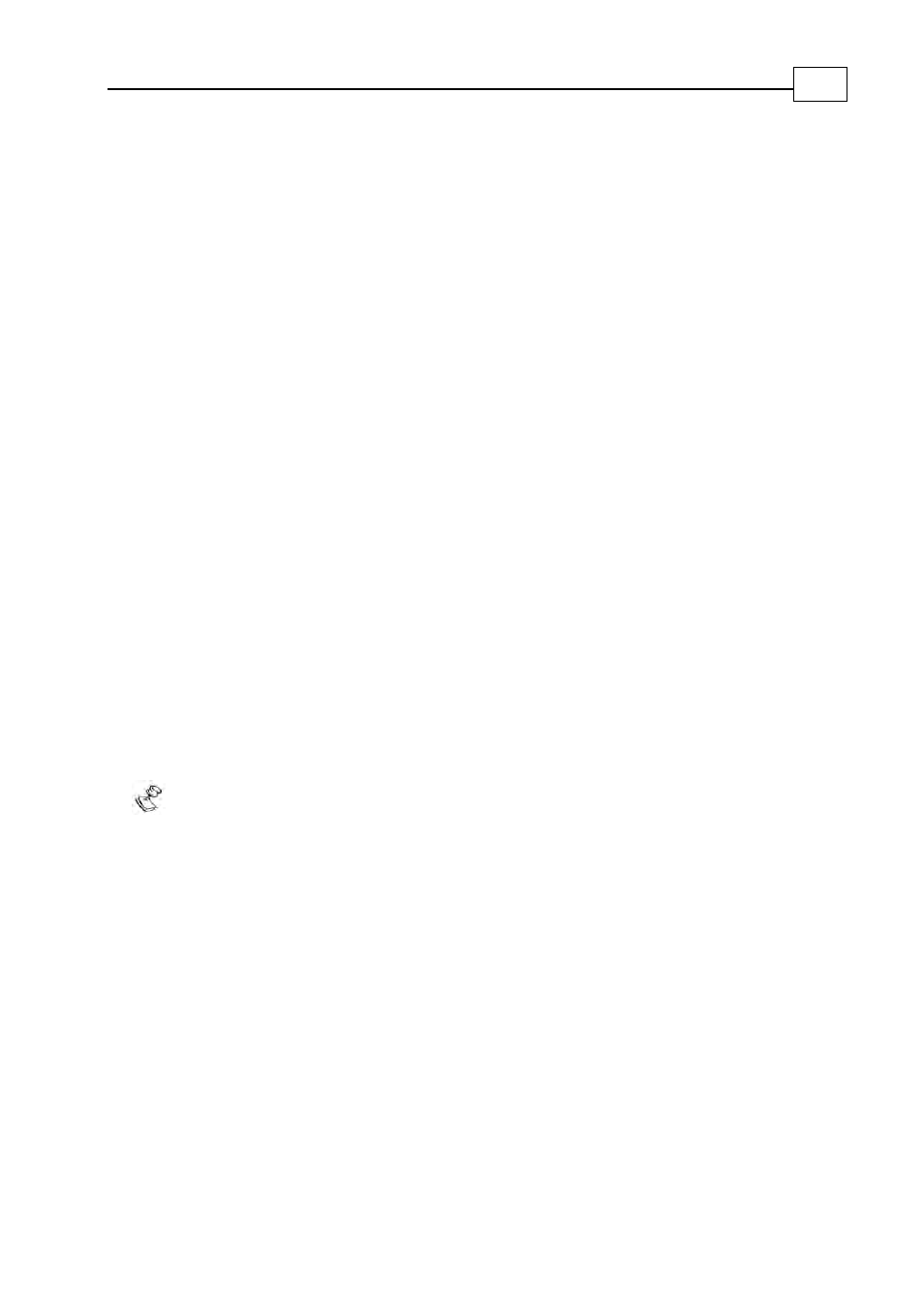
SimplIQ
Software Manual
MAN-SIMSW (Ver. 1.4)
8-1
Chapter 8: Commutation
8.1
General Description
The
SimplIQ
drives’ fixed magnet motors, in which a winding creates a magnetic field. If the
fixed magnet is directed along the field lines of the winding, it is in its steady state, and the
winding exerts no force on the magnet. If the magnet is not aligned along the winding field
lines, it will attempt to align with them.
Mathematically:
T = K
e
I * cos (θ)
where:
θ is the angle between the magnet and the field of the winding.
K
e
is a parameter, proportional to the strength of the magnet.
T is the motor winding torque.
I is the motor current.
If the magnet is allowed to move, it will rotate until it is aligned with the winding field, and
will remain stationary there.
A motor is composed of a fixed magnet and several windings arranged so that each winding
generates a field of different direction. By powering the windings alternately, the direction
of the winding field moves, and so does the direction to which the rotor is attracted. This
process of alternating the powered winding is called commutation.
DC brush motors are equipped with a mechanical device that selects which winding to
power. In brushless motors, this selection mechanism is electronic. The “commutation
policy” has two major types: stepper and BLDC (Brushless DC).
Commutation parameters are normally set using the Composer Wizard application.
To tune commutation manually, thoroughly read the CA[N] documentation in the
SimplIQ
Command Reference Manual.
8.1.1
DC Brush Motors
Each
SimplIQ
drive has three motor output connections, although a DC motor has only two
wires. In order to drive a DC motor with a servo drive, the motor is connected to the B and
C motor phase outputs and the phase A connection is left open.
The following parameters are set next:
CA[28] is set to 1 for a DC motor.
CA[18], encoder reference, is set for reference only. The CA[18] value does not affect
anything else at a later time.
CA[16], encoder direction, is set to 0 or 1 so that the encoder will count forward in the
desired direction of movement.