2 cyclical ecam – ElmoMC SimplIQ Software Manual User Manual
Page 176
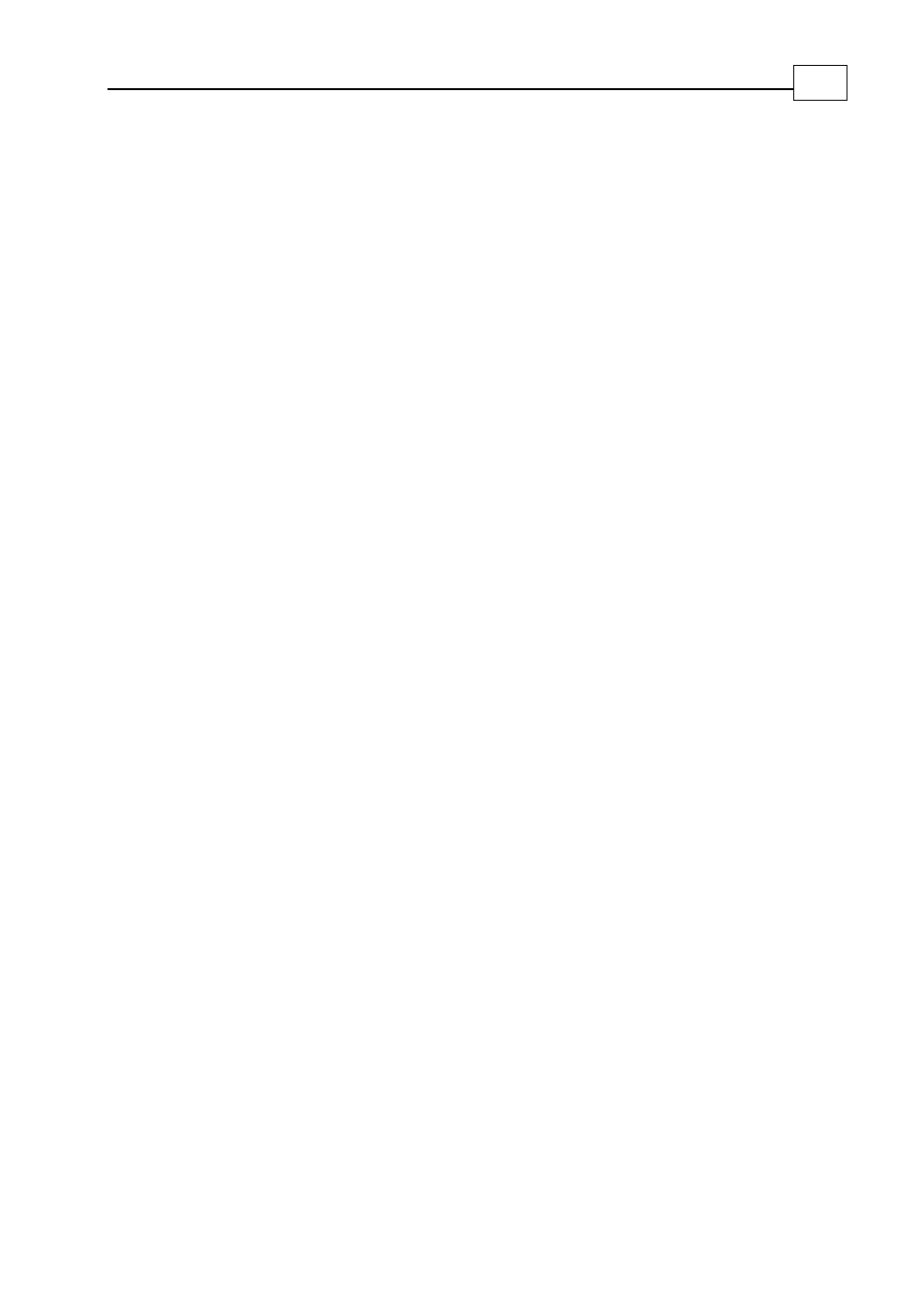
SimplIQ
Software Manual
The Position Reference Generator
MAN-SIMSW (Ver. 1.4)
11-35
One of the drives uses a digital output to control the flow of the chocolate out of the
drawing nozzle.
The drive program is:
IL[1]=7
Program DIN#1 as general-purpose input.
EM[1]=1
Enable
ECAM.
EM[2]=200
Length of ECAM vector.
EM[3]=0
Starting
position.
EM[4]=100
Conveyor encoder counts between two consecutive
ECAM table entries.
ET[1]=…;ET[2]=
…;ET[100]…; Program numeric data of ECAM table. If ECAM table
data is changed from cake to cake, consider loading
ECAM table using fast CAN loading method.
UM=5
Set single sensor position mode.
RM=1
Enable
external
referencing.
FR[3]=0;
Kill external input.
MO=1
Start
motor.
PA=1000;BG
Go to waiting position.
HY[2]=0;HY[3]=9;HY[1]=1
Null auxiliary encoder count upon cake arrival
(DIN#1
high).
Each drive has the following AUTO_I1 routine:
function AUTO_I1
DIN#1 has operated an already-programmed auxiliary
homing process to synchronize the following input.
OB[1]=1;
Activate
chocolate flow.
FR[3]=1;
Enable auxiliary encoder input with follower ratio of 1.
until (PY >= 2000)
Wait until end of head contour.
OB[1]=0;
Stop
chocolate.
until (PY >= 3000)
Go to start of eyes.
OB[1]=1;
Restart
chocolate.
until (PY >= 4000)
Draw
eyes.
OB[1]=0
Stop
chocolate.
FR[3]=0;PA=1000;BG
;
Return to starting point.
HY[1]=1
Program
auxiliary
encoder
to reset at next cake.
return
End of auto subroutine.
11.2.2.2 Cyclical ECAM
Cyclical ECAM mode is selected by EM[1]=2. In this mode, the master (auxiliary encoder
input) can advance indefinitely. The ECAM table defines the slave (motor position)
command for one master period, which is the input range to the ECAM table, IETmax.
In each master period (in which the master completes a travel of IETmax/FR[3] counts),
the slave advances by ET[EM[2]] - ET[EM[5]]. The following figure illustrates the
behavior of cyclical ECAM for EM[5]=1 and EM[2]=4.