Isolated drive output calibration – Red Lion MDC User Manual
Page 41
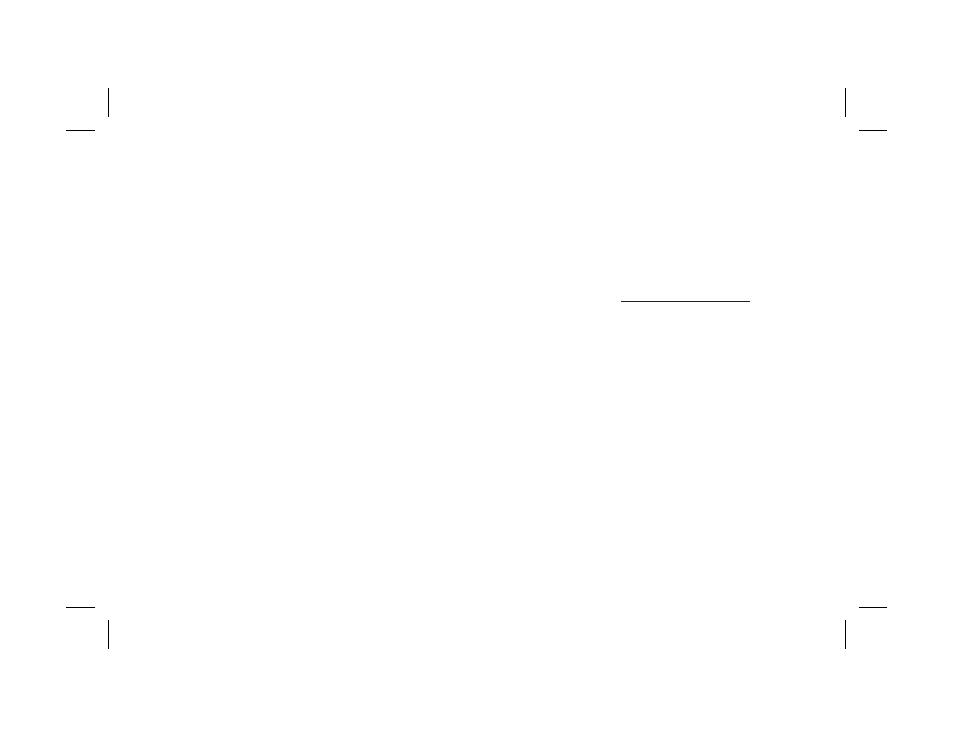
ISOLATED DRIVE OUTPUT CALIBRATION
Note: There is no need to calibrate the Drive Output Span if an EXTERNAL
reference is used or if the INTERNAL reference is used with the factory
calibrated 0 to 10 V span. If this is the case, skip Drive Output Span
Calibration and go to Motor Drive Setup.
DRIVE OUTPUT SPAN CALIBRATION
1) Make sure that the INTERNAL/EXTERNAL jumper above the bottom rear
terminal block is in the INTERNAL position.
2) Before connecting the MDC to the DRIVE, you must set the Span POT for
the Full scale control output required by the DRIVE. Connect a voltmeter
to the MDC drive output terminals. Power up the MDC. Enter the
Programming Module (see Programming General Description). In the
PROGRAM DIAGNOSTICS Menu, select TEST DRIVE OUTPUT. Push
the Up arrow until the %Output reads 100%. The meter should read 10
VDC. Adjust the Span POT for the desired Full scale value within the 5 to
15 VDC specified range of the MDC.
MOTOR DRIVE SETUP
1) Before connecting the MDC to the Motor Drive, set up the Drive according
to the manufacturer’s instructions.
2) Then set the Drive’s :
a) Acceleration / Deceleration POTs to minimum time (maximum rate).
b) IR compensation to a minimum.
c) Maximum Speed to 110% of the maximum normal operating speed with
an unloaded or lightly loaded motor.
This completes the steps necessary to calibrate the MDC for the Motor and
Drive. To verify that calibration is correct and to test system operation,
continue with VERIFYING SYSTEM OPERATION.
VERIFYING SYSTEM OPERATION
1) With the MDC connected to the Drive as noted in Installation and
Connections, power up the MDC and enter the Programming Module.
2) Set up the scaling for the MDC in the Program Scaling Menu, if you have
not already done so.
3) Power up the Motor and Drive. The motor should have no load or be only
lightly loaded.
4) Enter the Program Diagnostics Menu and select TEST DRV OUT. Use the
Up arrow key to select 100% output. The transducer feedback in Hz is
shown on display line two. It should be:
Feedback (Hz) = 1.1 x PPR FB x MAX RPM FB
60
This allows 10% headroom to maintain regulation under various motor
load conditions. If the feedback frequency is not close to this value, adjust
the DRIVE’s GAIN or MAXIMUM SPEED POT accordingly. Use the Up
and Down arrow key to test the drive/motor operation over the full speed
range. Use the F2/STP key to stop the motor immediately. Use the ESC key
to stop immediately and exit TEST DRV OUT.
5) Verification complete. Exit the PROGRAM MODULE.
TRIM
The Trim value can be displayed on one of the programmable displays (See
Program Displays Menu). The Trim value is the number of D/A correction
bits out of the available 4095 that are required to maintain the target speed.
This value should not be more than 200 to 300 during normal operation with
an UNLOADED motor. The Trim value will increase to compensate for an
increase in motor load. If the Trim value is over 300, refer to the Drive Output
Span Calibration and Motor Drive Set-up sections above.
-39-