Troubleshooting, 1 overview, Faulty instrument – Dwyer Series PUF User Manual
Page 47: Incorrect setup, Application problem, Troubleshooting 43, 1 overview 43
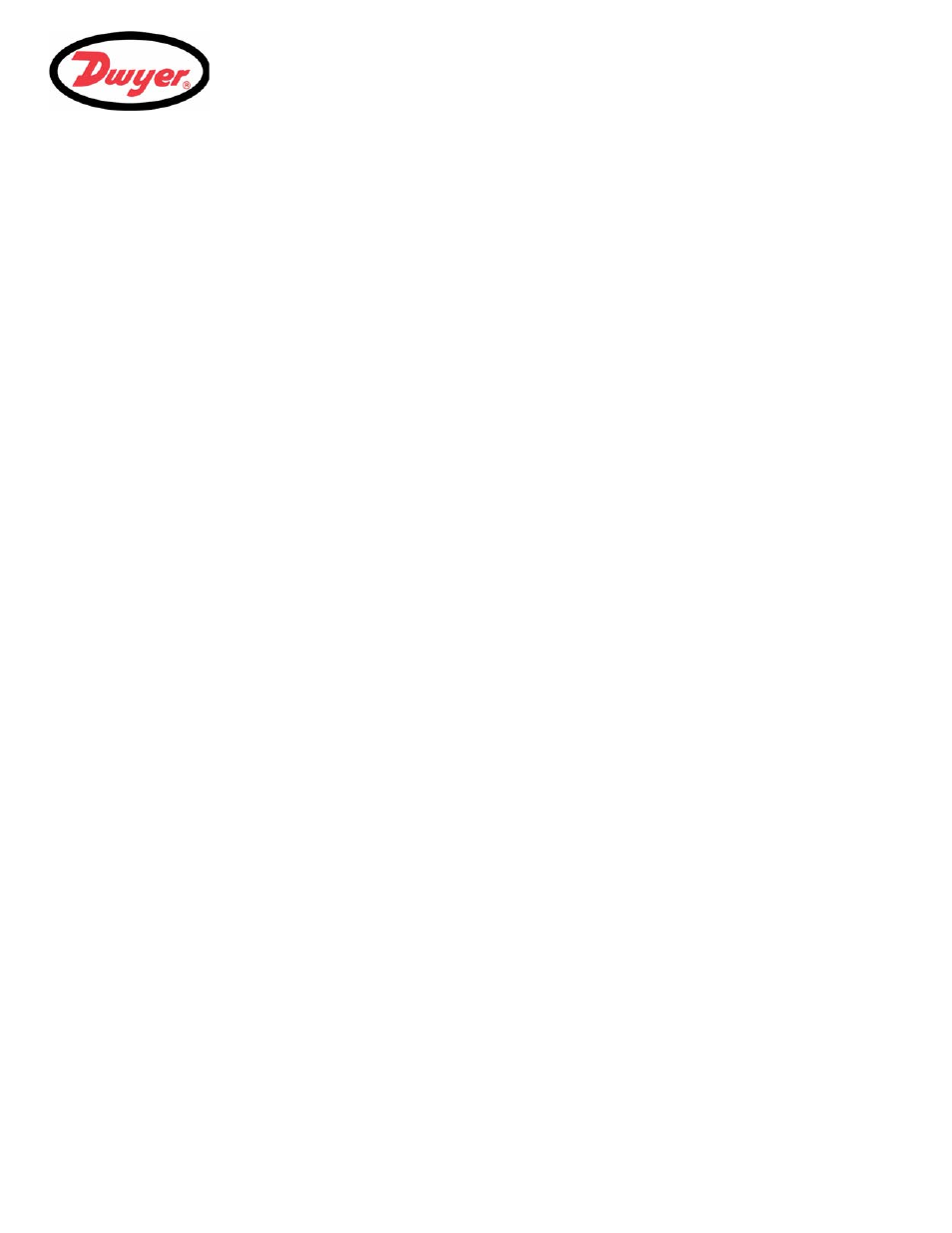
5: Troubleshooting
43
5: Troubleshooting
5.1
Overview
If you have a problem with your flow monitoring system it can be due to any of the following:
Faulty instrument
If you suspect the instrument is faulty, you can check it out using a test block as described in Paragraph 5.4. This
will establish that the instrument is functional and receiving a healthy signal from the connected transducers.
Incorrect setup
A low, or zero, signal could be caused by incorrect set-up such as:
• Incorrect site data entered into the instrument.
• Incorrect or non-matching ultrasonic transducers selected for use.
• Incorrectly fitted transducers – lack of couplant applied, incorrect spacing, insecure attachment.
• Poor connections between the probes and the instrument.
Application problem
If you are certain that the instrument is healthy and suitably set-up for the current site, and the probes are
properly assembled and fitted correctly, there could be an application problem concerned with the site.
Check such conditions such as:
Poor pipe outer surface quality
• Uneven surface preventing good surface contact with the transducer.
• Flaking paint (should be removed).
• Variable air gap in concrete-covered pipes affecting the ultrasonic signal quality.
Poor internal pipe construction
• Rough internal pipe walls affecting fluid flow (see roughness factor).
• Internal welds positioned in the transducer signal path affecting the signal quality.
• The ‘drippings’ in galvanized-dipped pipes or other irregularities interfering with the signal path.
Incorrect probe location
• Transducers located too close to bends or valves, disturbing the flow profile.
• Transducers located too close to insertion probes, disturbing the flow profile.
• For horizontal pipework, transducers should not be positioned on the top of the pipe.
Poor fluid conditions within the pipe
• Fluid contains bubbles, high particle density or sludge.
• Air in the top of the pipe.
Low fluid flow within the pipe
• Pipe obstructions.
• Malfunctioning valve not opening fully (or closed inadvertently).
Liquid content problems
• Multiple liquid contents do not comply accurately to expected sound speed criteria.
• Very hot pipe almost turns water to steam and therefore exhibits the wrong speed characteristics –could
be due to reduced pipe pressure.
• Flashover – liquid turns into a gas because of lower than required pressure.