2 sense connections, 3 grounding, Sense connections -9 – KEPCO EL Series Electronic Load Operator Manual P/N 243-1295 Firmware Version 4.00 to 4.xx User Manual
Page 27: Grounding -9, Erate. see 2.6.2.2 for, Warning
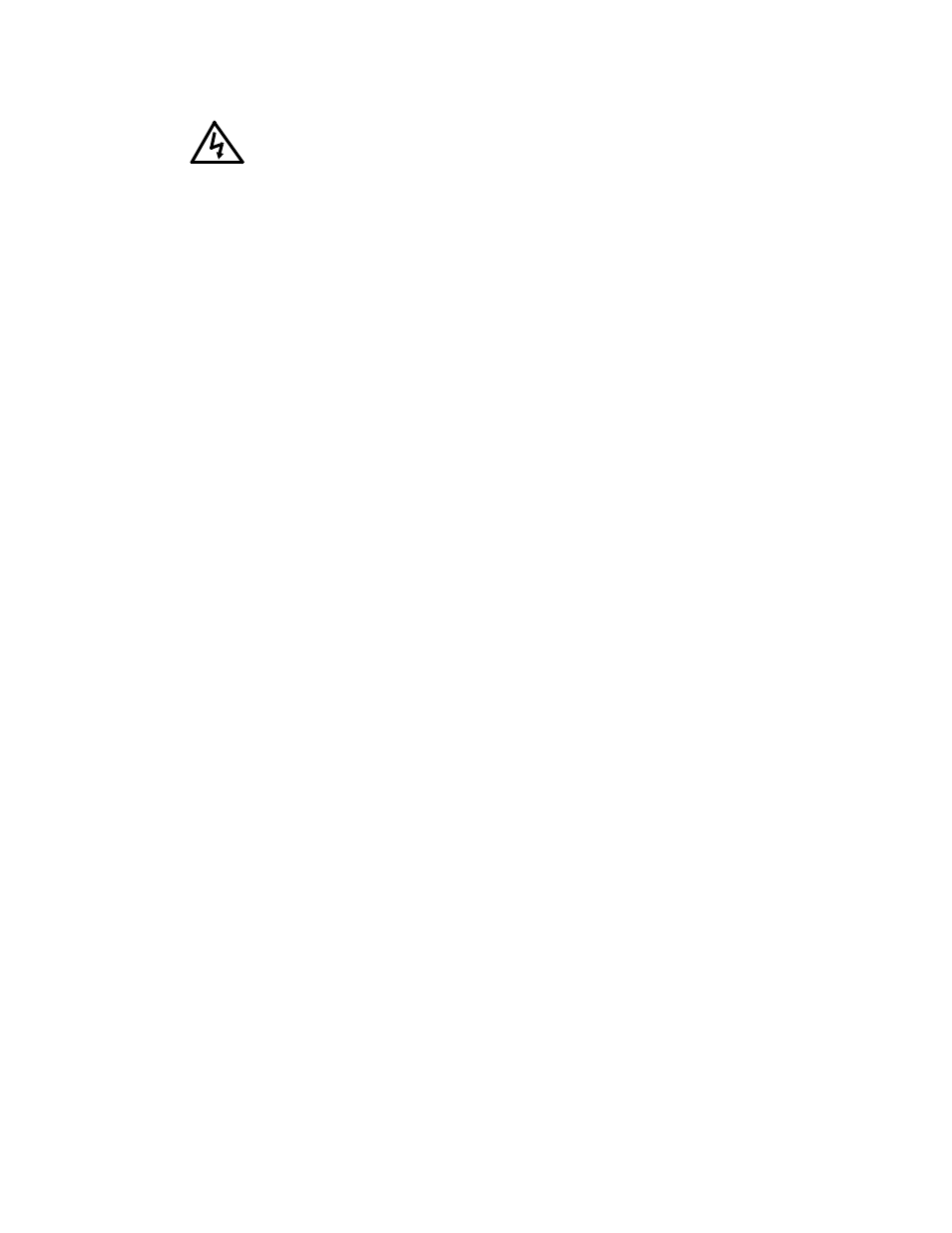
SERIES EL 071414
2-9
WARNING
Reversing the polarity at the LOAD terminals will cause immediate and
significant damage to the load and UUT!
2.6.2.2
SENSE CONNECTIONS
Remote Sensing terminals (±S) are provided for connection to the UUT in order to compensate
for voltage drops on the power cables connected to the ±LOAD terminals. When remote sensing
is used, the readings shown on the front panel accurately reflect the output of the UUT.
To use remote sensing first remove the local sense jumpers (NOTE: Local sense jumpers can
be fabricated as needed using #18 AWG stranded wire) installed on the SENSE Terminal block.
Then connect wires (#24 AWG or 22 AWG) from +S to the positive output of the UUT, and from
–S to the negative output of the UUT. Twisting of sense wires is recommended.
If remote sensing is not used, the pre-installed local sensing jumpers between S+ and + and
between S– and – must remain in place as shown in Figure 2-4 (single) or 2-5 (dual). Operating
the unit with neither local nor remote sensing in place will result in erroneous readings.
CAUTION: When connecting the load to the UUT be very careful not to accidentally short
the UUT output in the process of connecting the wiring. Best practice is to
make the connection to the UUT Positive (+) output connector the last con-
nection.
For remote sensing, remove jumpers from ±S and connect ±S terminals to corresponding ± out-
put terminals at the unit under test.
Connect the Series EL Electronic Load to the UUT using cabling appropriate for the current and
voltage drawn during testing. Contact Kepco if assistance is needed in selecting the appropriate
wire size, length and physical configuration. Ensure all connectors are suitable for the currents
and that connections are tight. Connections should be re-checked on a regular basis (see PAR.
2.6) to ensure continued low-resistance connections.
2.6.2.3
GROUNDING
It is required for EN 61326-1 compliance that the 1/4-inch bolt with wingnut and flat washers
(supplied) at the top left of the rear panel be connected to earth ground.
The LOAD Bus bars are isolated from the chassis and from the control circuits well into the 100s
of volts. The resistance between the REF IN – terminal and the load’s negative connection is
over 300 K ohms and the REF IN pins are rated for 600 volts.Since a single point failure could
render this resistance 0 ohms designated as Hazardous. The SELV analog control input (ANA-
LOG CONTROL connector pin 4, pin 8 return) is referenced to the chassis via a small 100 ohm
resistor and as a result there is no possibility of equipment damage.
The I-Load output (ANALOG CONTROL connector, pin 5, pin 9 SELV return) is independently
isolated from the control circuits and therefore is double-isolated from all other external connec-
tions. Lastly, all of the Remote Interface inputs (RS-232, USB 2.0, RS-522), optional LAN and
GPIB) are optically isolated from the control circuits and are therefore doubly isolated from all
other circuits.