Yokogawa Integral Oxygen Analyzer ZR202 User Manual
Page 144
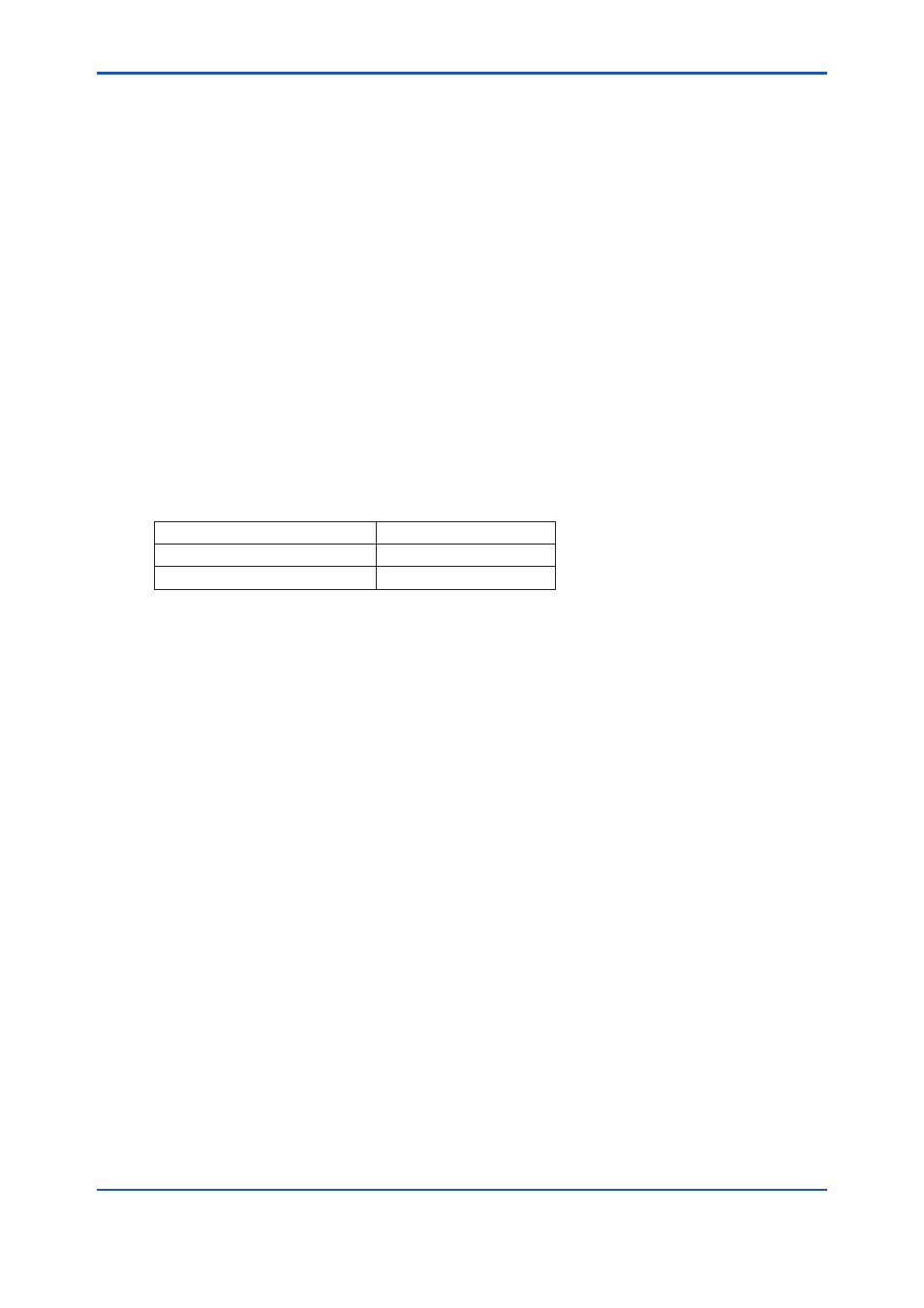
<12. Troubleshooting>
12-5
IM 11M12A01-04E
(1) Confirm the following and carry out calibration again: If the items are not within their proper
states, correct them.
a. If the indication for “Zero gas conc.” is selected in “Calibration setup,” the set value should
agree with the concentration of zero gas actually used.
b. The calibration gas tubing should be constructed so that the zero gas does not leak.
(2) If no alarm is generated as a result of carrying out re-calibration, it is suspected that improper
calibration conditions were the cause of the alarm in the preceding calibration. In this case, no
specific restoration is necessary.
(3) If an alarm is generated again as a result of carrying out re-calibration, deterioration of or
damage to the cell (sensor) is suspected as the cause of the alarm. Replacement of the cell
(sensor) with a new one is necessary. However, before replacement, carry out the following:
Check the cell voltages when passing the zero gas and span gas.
a. Display the cell voltage with the parameter code A11.
b. Check whether or not the value of the displayed cell voltage is very different from the
theoretical value at each oxygen concentration. Confirm the theoretical values of the
cell voltage in Table 12.3. Although it cannot be generally specified as to what extent the
difference from the theoretical value is allowed, consider it to be approximately ±10 mV.
Table 12.3
Oxygen Concentration and Cell Voltage Oxygen concentration
Oxygen concentration (% O
2
)
Cell voltage (mV)
1%
67.1
21%
0
(4) Confirm whether deterioration of or damage to the sensor assembly that caused the alarm has
occurred abruptly during the current calibration in the following procedure:
Check the history of the span gas correction ratio with the parameter codes A50 through A59,
Check the history of the zero gas correction ratio with the parameter codes A60 through A69.
The larger the parameter code number, the older the displayed data. Changes in deterioration of
the sensor can be seen.
(5) If deterioration of the cell assembly has occurred abruptly, it may show that the check valve,
which prevents moisture in the furnace from getting into the calibration gas tubing, has failed. If
the gas in the furnace gets into the calibration gas tubing, it condenses and remains in the gas
tubing. The cell assembly is considered to be broken for the reason that the condensation is
blown into the cell assembly by the calibration gas during calibration and so the cell cools quickly.
(6) If the cell assembly has been gradually deteriorating, check the cell assembly status in the
following procedure:
a. Display “Cell resistance” by specifying the parameter code A21. A new cell will show a cell
resistance value of 200Ω or less. On the other hand, a cell (sensor) that is approaching the end
of its service life will show a resistance value of 3 to 10 kΩ.
b. Display “Cell robustness” by specifying the parameter code A22. A good cell (sensor) will show
“5,” “Life > 1 year” (refer to Section 10.1.11).