Darex XPS-16 Operating Instructions User Manual
Page 65
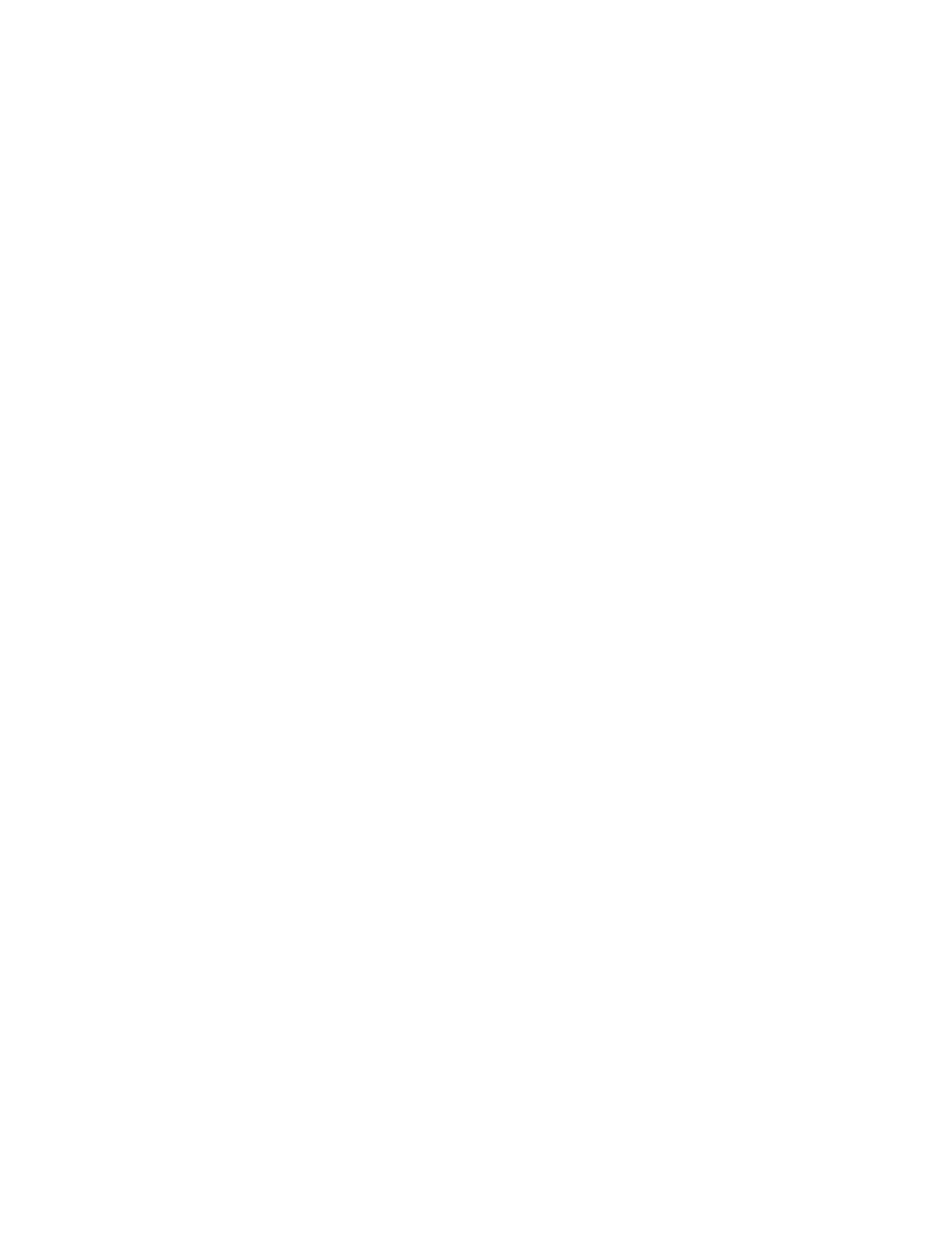
65
Symptom
Failed Initialization screen test
Cause
• Axis driver card failure
• Limit sensors bad
• Solenoid bad
• Machine has moved past the limit switches
Symptom
LCD screen too light or dark to read
Cause
• Contrast needs adjusted
Refer to page 32
• LCD back light failure
• LCD bad
Symptom
LCD screen displays garbage or grossly
inaccurate information.
Cause
• Machine temperature is too cold/hot – do
not operate until machine temperature
reaches above 7°C (45°F) but not more
than 32°C (90° F)
• Restore calibrations from locked area
• LCD battery is dead
• LCD is bad
Symptom
After pressing “Cycle Start” the machine
does not move into the sharpening cycle
Cause
• Make sure drill has been loaded properly
and sensor button has been depressed
• Close door
• Software has caused machine to hang up –
turn machine off and then on again
• Cycle start switch needs replacement
• Printed circuit board on back of LCD is bad
Symptom
Drill rotates in front of fiber optic sensor
failing to locate cutting edge
Cause
• Old software installed
• Drill diameter is smaller than 3mm
• Drill diameter is of a smaller dimension
with a thick web
• Color of drill is interfering with cutting
edge detection – typically gold or black
drills
Refer to page 61
• False diameter was input or detected in
• Fiberoptic Amplifier Baseline setting has
changed. Contact Darex for instructions.
manual mode
• Cutting edge is broken
• Cutting edge has shinny build up, such as
aluminum
• Surface finish too rough
• Calibration of fiber optic sensor is incorrect
and will need recalibrated
• Fiber optic lens is loose
• Fiber optic sensor needs replaced
• Fiber optic lens needs cleaned or replaced
• Fiber optic cable has been damaged
• Shank is larger than body of drill and cor-
rect diameter has not been manually input.
Example: Step drill
Symptom
Auto diameter detect will not detect cor-
rect diameter
Cause
• Diameter detection rod is bent
• Diameter detection rod has been improp-
erly installed.
Refer to page 47
• Incorrect diameter calibration
• Shank of drill may be larger/smaller than
actually body of drill
• Drill flutes are worn or damaged
• MTO #1 button excessively worn
Symptom
Auto web detection does not display cor-
rect web thickness
Cause
• Fiber optic sensor lens is dirty.
Refer to
page 81
• Fiber optic sensor is not calibrated cor-
rectly
• Fiber optic sensor is bad
• Old software installed
Symptom
Cutting edge is not positioned correctly
at 1:00
Cause
• Chip on cutting edge
• Burr on cutting edge
• The fiber optic sensor has detected the
split line as cutting edge
• Drill has a hook in the cutting edge – use
the Advance Screen to compensate.
Refer
to page 39
• Changing from extreme point angles. Ex-
ample: Converting a 180° drill into a 118°
point angle
• Material build up on cutting edge
• A value left in the Advance Screen
Trouble Shooting Section