4 provisioning the sensor calibration, 1 calibrating using an instrument – Alpha Technologies PowerAgent SC3 User Manual
Page 45
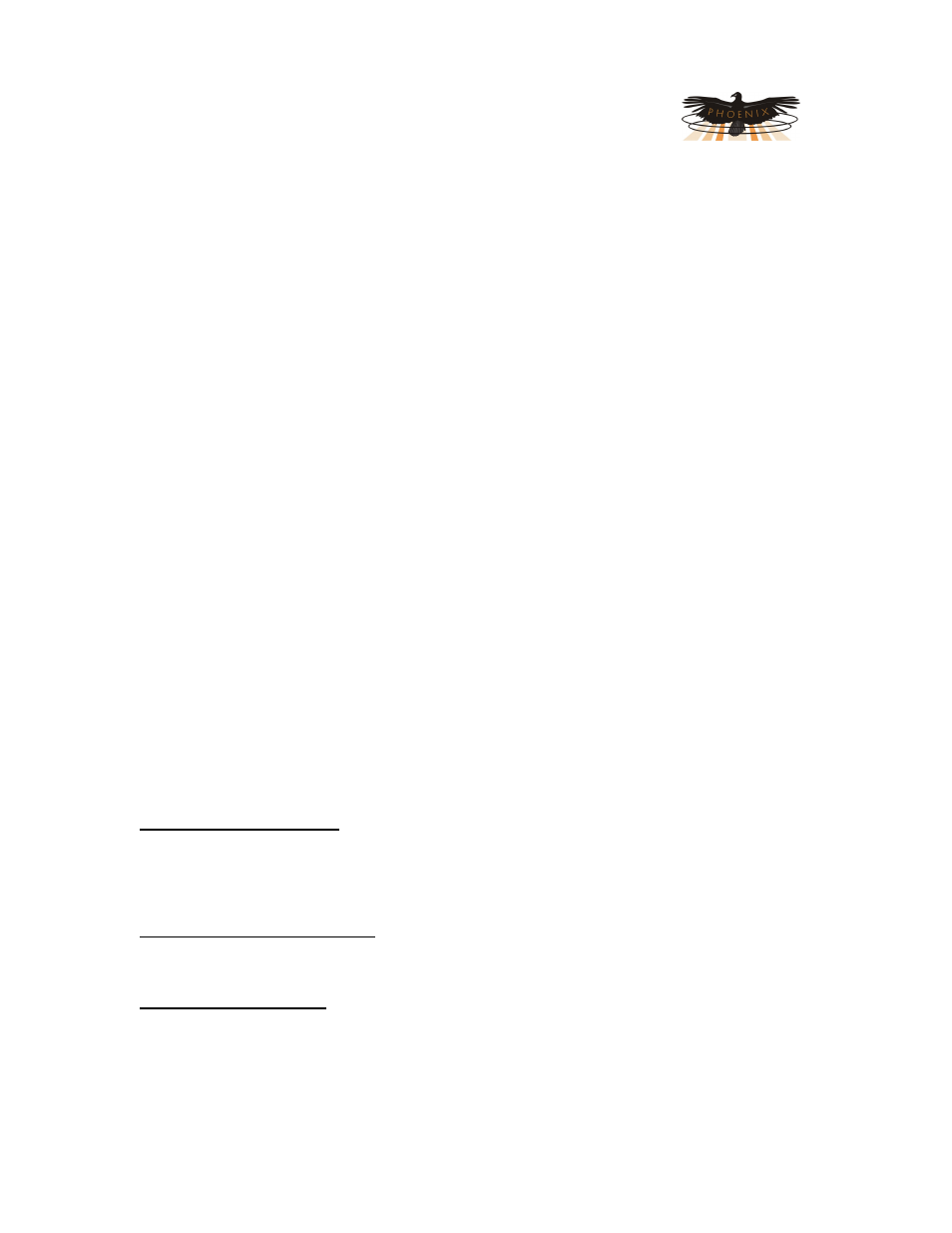
PowerAgent
TM
SC3 Site Controller
Document # 700-000014-01 Rev 2
Installation and Operation
Phoenix Broadband Technologies, LLC
10/28/2010
Page 45 of 57
6.5.4
Provisioning the Sensor Calibration
Instruments used to measure conductance or admittance can exhibit substantial variation
between various manufacturers and models of instruments. This variation is due to the different
techniques used to make the measurements and the different measurements actually made.
Some instruments measure DC resistance, others measure AC impedance at various
frequencies, still others measure the resistive component of the complex impedance at various
frequencies. These factors combine to produce variations of as much as 30% between
instruments.
In addition to these variations there is also significant variation due to the placement of the
instrument probes on the jar terminals. This is particularly important on high admittance batteries.
The admittance measurement made by the sensor without any calibration is accurate within 5%,
however this measurement may not agree with a specific instrument because of the factors
mentioned above.
6.5.4.1 Calibrating using an Instrument
The calibration process allows the monitoring sensor to be calibrated after installation using a
one-time measurement from a precision portable measuring instrument. Once a monitoring
sensor or transponder is installed on the equipment being monitored, reference measurements
from the precision instrument are entered into the monitoring system, and any errors between the
instrument and the sensor are subtracted before the result is displayed or reported. With
calibration, an inexpensive monitoring system gains all the advantages of stability, repeatability,
real-time-continuous data collection, and trend analysis, while retaining a measurement accuracy
that is comparable to the expensive portable instrument.
When monitoring a high capacity jar with an impedance/admittance monitoring system, the
sensor is required to measure jar equivalent resistances in the order of 100 micro ohms. The
resistance of the point of contact between the sensor and the jar strap or lug is typically in the
order of 35-75 micro ohms. In high capacity batteries this ‘spurious’ contact resistance can
produce errors of 20% or more. In the PBT Battery Monitoring System, the calibration process
essentially subtracts the spurious contact resistance from the total measured resistance, leaving
a stable, reproducible, and accurate measurement of true jar admittance that can be analyzed
and trended to allow pre-emptive maintenance. There are three software mechanisms that are
used to calibrate the admittance measurement:
Sensor Factory Calibration
The Site Control Unit recognizes the type of sensor that is used to monitor a high-capacity jar.
Whenever it receives a measurement from this type of sensor, it subtracts a small fixed
resistance (typically about 35 micro-ohms) from the reading before converting it to admittance
and displaying it.
String-Level On-Site Calibration
The installer can enter a user-defined constant into the Site Controller which will cause all the
batteries in a given string to be corrected, in addition to the built-in factory correction.
Individual Jar Calibration
The installer can enter an instrument measured admittance into the Site Controller which will
cause an individual jar to be corrected, in addition to the string-level constant and the built-in
factory correction.