Example – Siemens MICROMASTER 420 User Manual
Page 51
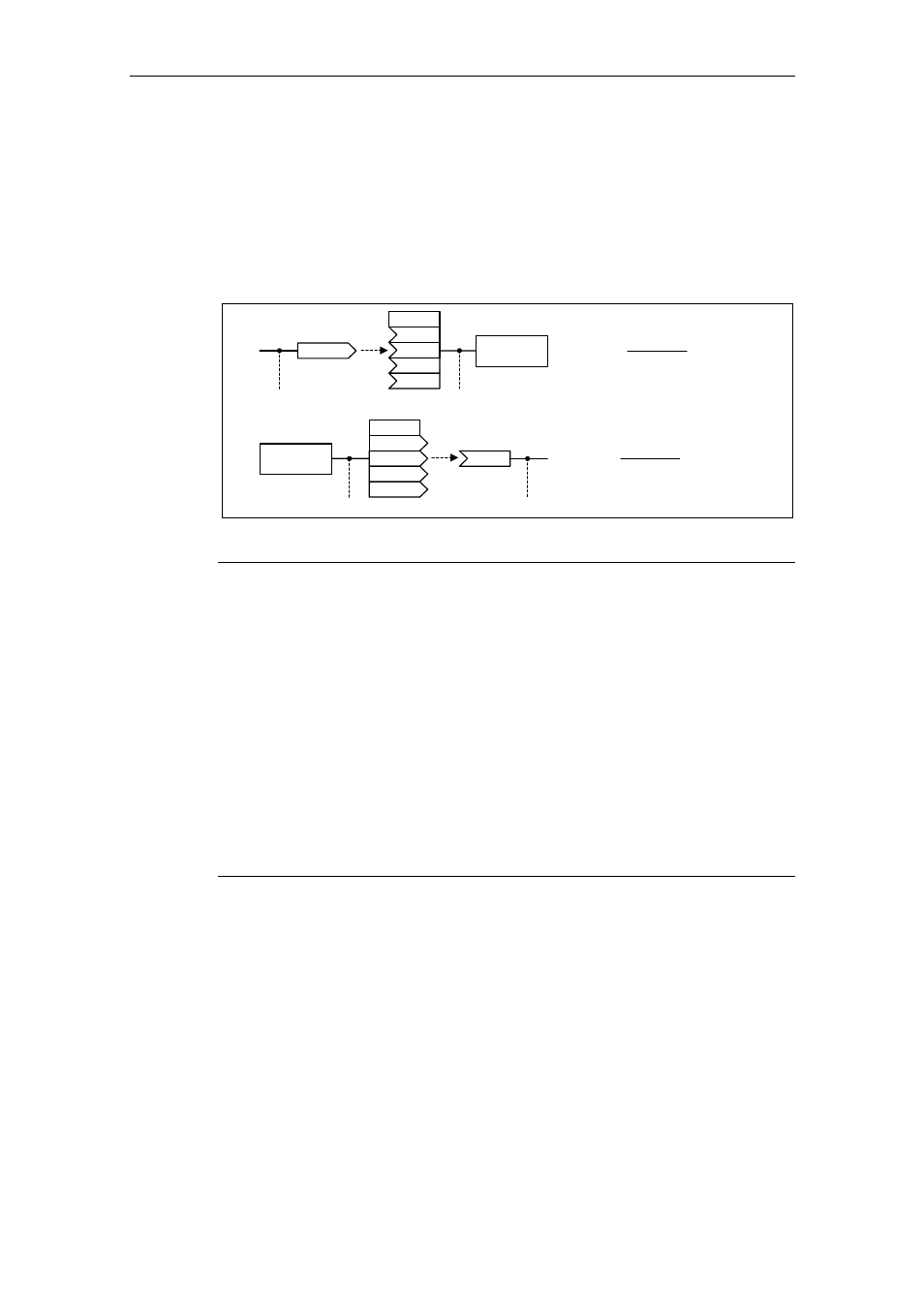
Issue 07/04
3 Functions
MICROMASTER 420 Operating Instructions
6SE6400-5AA00-0BP0
51
Example
The normalization / de-normalization via the "USS to BOP link" serial interface is
shown using the reference frequency P2000.
If the connection between two BICO parameters is closed (directly using BICO
parameters or indirectly using P0719 or P1000), that have a different
representation/notation (normalized representation (hex) or physical representation
(Hz)), then the following normalization is made in the drive inverter to the target
value:
P1070
y[Hz]
2000
P
4000[Hex]
r2015[1]
y[Hz]
⋅
=
r2015
[0]
[1]
[2]
[3]
P2016
[0]
[1]
[2]
[3]
r0021
x[Hz]
y[Hex]
x[Hex]
]
Hex
[
4000
P2000[Hz]
r0021[Hz]
y[Hex]
⋅
=
USS-PZD
BOP-Link
USS-PZD
BOP-Link
Fig. 3-7
Normalization / de-normalization
Note
Analog values are limited to 10 V or 20 mA. A maximum of 100 % can be output
/ read-in referred to the appropriate reference values as long as no DAC/ADC
scaling (factory setting) was made.
Setpoints and actual value signals via the serial interface:
♦
When transferring this data via the PZD part, it is limited to the value 7FFF h.
This is the reason that the max. value 200 % is referred to the reference
value.
♦
When transferring this data via the PKW part, it is transferred as a function of
the data type and units.
Parameter P1082 (max. frequency) limits, in the drive inverter, the frequency
independently of the reference frequency. This is the reason that when P1082 is
changed (factory setting: 50 Hz), then the P2000 (factory setting: 50 Hz) should
always be adapted. For instance, if for a NEMA motor the parameter is set to 60
Hz and P2000 is not changed, then the analog setpoint / actual value at 100 %
or a setpoint/actual value signal at 4000 h is limited to 50 Hz!