KEPCO KLP Series (older -1200 models) Operator Manual User Manual
Page 110
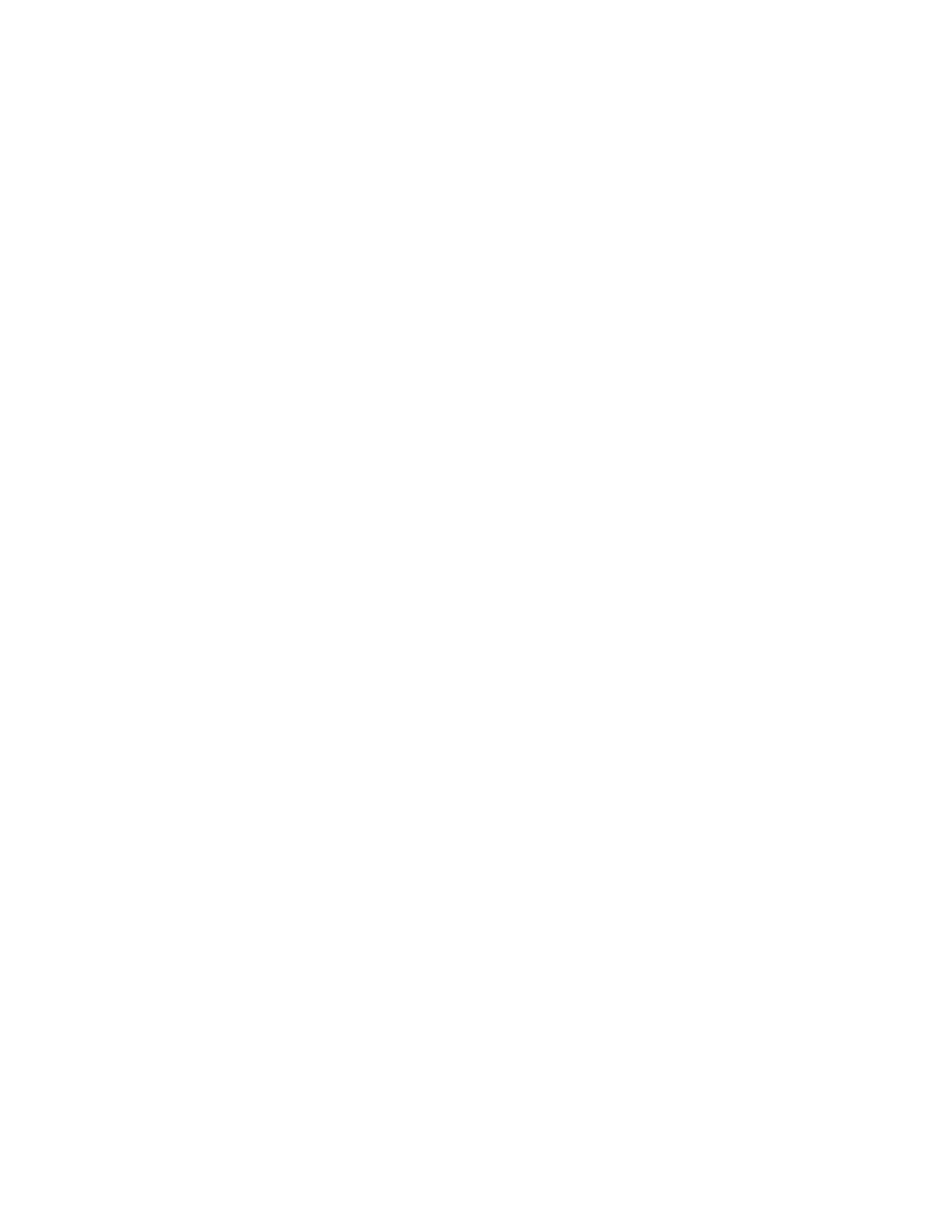
How do I enter/exit Function mode? To enter a function, repeatedly press FUNCTION using a thin tool until status reads VIRT (vir-
tual model, see below), ADDR (set GPIB address, PAR. 3.2.8), BAUD (set RS 232 baud rate, PAR. 3.2.9), M/S (Master/Slave, PAR.
3.2.10) or UTIL (utility, PAR. 3.2.11). To exit a function, continue to press FUNCTION until staus display is blank.
How do I view/change the virtual model settings? The virtual model limits the maximum programmable settings that can be
accepted. The default Virtual Model is: V = rated voltage, A = 1200/rated voltage, e.g., for KLP 75-33-1200: 75V/16A (1200/75=16A).
If status shows SET, exit setpoint mode (tap either knob once). Use thin tool to press FUNCTION repeatedly until status reads VIRT.
VOLTS and AMPS displays show the maximum voltage and current of the present virtual model. If no change exit function mode (see
above). Press DC OUTPUT once. Status shows PASS (password). Enter password (see above) and tap DC OUTPUT to accept.
When password is accepted, status reads VIRT. To change setting rotate Voltage and Current knobs until VOLTS and AMPS dis-
plays show desired virtual model settings. (Press and hold knob in while turning for fine adjustment.) Press DC OUTPUT to accept
virtual model settings. Unit displays DONE, then resets and repeats power on sequence while status flashes VIRT. Default protection
limits (based on new virtual model settings) are displayed while status reads PROT. When complete, unit is placed in setpoint mode
with VOLTS and AMPS displays reset to 0 volts, minimum amps (see PAR. 3.2.5).
How do I view/change overvoltage and undervoltage protection limits? Overvoltage (OVP) and overcurrent (OCP) protection
limits default to 120% of programmed virtual model limits. If status reads SET, tap either knob to exit setpoint mode. To view protec-
tion limits, use a thin tool to press and hold PROTECT until status reads PROT, VOLTS and AMPS displays show the protection lim-
its; To change limits, while continuing to hold PROTECT in, adjust OVP and OCP limits as desired using the Voltage and Current
knobs. When PROTECT released, values showing in VOLTS and AMPS displays are the new protection limits (see PAR. 3.2.7).
REMOTE ANALOG OPERATING MODE INSTRUCTIONS
How do I enable analog operating mode? Connect ANALOG_CTRL (pin 12) to GROUND (pin 9, 11, 13, or 15) of analog port prior
to power-up to enable remote analog programming for that session. Remote analog control is indicated by "aREM" in status display.
The status of ANALOG_CTRL is sensed at power-up only. Enabling analog operating mode disables the local operating controls on
the front panel.(see PAR. 3.7).
How do I Enable or disable the output? Connect REM_INH (pin 8) to GROUND (pin 9, 11, 13, or 15) of analog port to disable
power supply output. Opening the connection will enable the output (see PAR. 3.7.1).
How do I adjust voltage and current setpoints using an external voltage source? Set analog I/O DIP switch positions 1 and 2 up
(factory default position) to use external voltage for remote analog programming of voltage and current, respectively. Full scale pro-
gramming voltage for output voltage and current is factory set at 10V. To alter full scale value perform calibration (PAR 4.3) and exter-
nal calibration (PAR. 4.3.3). Apply a 0-10V signal from Vref (pin 1) and Cref (pin 3) to GROUND (pin 9, 11, 13, or 15) of analog port to
adjust the setpoint values for output voltage and current proportionally. A maximum combination of programmed voltage and current
cannot exceed 1200 watts. Programming input pins are only active when analog port is enabled. (See PAR. 3.7.3 for details.)
How do I adjust voltage and current setpoints using an external resistance? Set analog I/O DIP switch positions 1 and 2 down
to use external resistance for remote analog programming of voltage and current, respectively. Full scale programming resistance for
output voltage and current is factory set at 10KOhms; see PAR 3.2.1.3 for instructions on altering full scale value and use 1KOhm per
volt scale factor. Applying a 0-10KOhm resistance from Vref (pin 1) and Cref (pin 3) to GROUND (pin 9, 11, 13, or 15) of analog port
adjusts the setpoint values for output voltage and current proportionally. Maximum combination of programmed voltage and current
cannot exceed 1200 watts.Programming inputs are only active when analog port is enabled. (See PAR. 3.7.2 for details.)
How do I Read back operating voltage and current? Analog signals proportional to actual output voltage and current levels are
available at VOLT_RBACK (pin 6) and CURR_RBACK (pin 7) of analog I/O port. Full scale signal level is the same as that for full
scale programming. Readback signals are always available at analog port, even if analog programming is not enabled.
How do I exit remote analog programming mode? Depressing and releasing both Voltage and Current knobs forces the unit to exit
remote analog programming mode and return to local operating mode. This can also be done by sending a SYST:KLOC OFF com-
mand (PAR. B.81) via the RS 232 or GPIB remote digital inputs. To restore remote analog control recycle source power.
REMOTE DIGITAL OPERATING MODE INSTRUCTIONS
How do I enabling digital operating mode? Sending any digital command via either the GPIB or RS 232 port immediately sets the
unit in remote digital operating mode and disables the local operating controls on the front panel. For details on command formatting
and communication protocols see PARs 3.4 (RS 232) and 3.5 (GPIB). Additional information about common commands and SCPI
commands, including programming examples, are included in Appendices A and B.
How do I exit remote digital programming mode? Depressing and releasing both Voltage and Current knobs will force the unit to
exit remote digital programming mode and return to local operating mode. Remote digital control is reactivated upon transmission of
any digital command by the control (host) computer.
How do I change the GPIB address? The factory default GPIB address for all KLP models is 6. Using a thin tool, press FUNCTION
repeatedly until status reads ADDR; the active GPIB address shows in the AMPS display. Press FUNCTION to exit or rotate Current
knob to change address. Tap DC OUTPUT to accept; unit advances to the next function (see PAR. 3.2.8). The GPIB address can
also be changed using the SCPI command SYST:COMM:GPIB:ADDR (PAR B.66).
How do I adjust RS 232 baud rate? see PAR. 3.2.9. The factory default RS 232 baud rate for all KLP models is 9600. Using a thin
tool, press FUNCTION repeatedly until status reads BAUD; AMPS display shows active baud rate x 1000 (e.g., 9600 is displayed as
9.6). Press FUNCTION to exit or rotate Current knob to change the baud rate. Tap DC OUTPUT to accept; unit advances to the next
function. The baud rate can also be changed using the SCPI command SYST:COMM:SER:BAUD (PAR B.68).