Contour data (cycle g120), G120 contour data (essential), 7 sl cy cles g roup ii – HEIDENHAIN iTNC 530 (340 422) ISO programming User Manual
Page 342
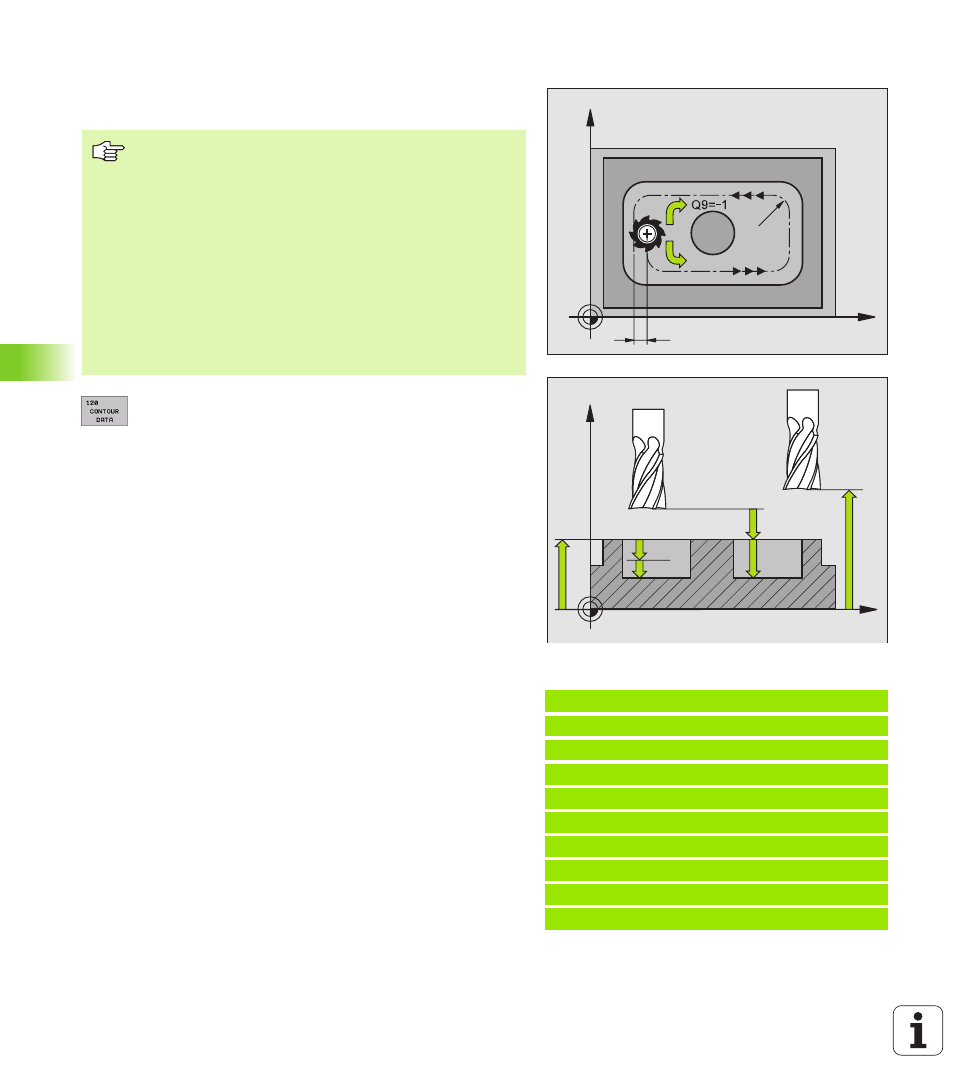
342
8 Programming: Cycles
8
.7 SL Cy
cles G
roup II
CONTOUR DATA (Cycle G120)
Machining data for the subprograms describing the subcontours are
entered in Cycle G120.
U
U
U
U
Milling depth
Q1 (incremental value): Distance
between workpiece surface and bottom of pocket.
U
U
U
U
Path overlap
factor Q2: Q2 x tool radius = stepover
factor k.
U
U
U
U
Finishing allowance for side
Q3 (incremental
value): Finishing allowance in the working plane
U
U
U
U
Finishing allowance for floor
Q4 (incremental
value): Finishing allowance in the tool axis.
U
U
U
U
Workpiece surface coordinate
Q5 (absolute value):
Absolute coordinate of the workpiece surface
U
U
U
U
Set-up clearance
Q6 (incremental value): Distance
between tool tip and workpiece surface.
U
U
U
U
Clearance height
Q7 (absolute value): Absolute
height at which the tool cannot collide with the
workpiece (for intermediate positioning and retraction
at the end of the cycle).
U
U
U
U
Inside corner radius
Q8: Inside “corner” rounding
radius; entered value is referenced to the tool
midpoint path.
U
U
U
U
Direction of rotation ? Clockwise = -1
Q9:
Machining direction for pockets.
n
Clockwise (Q9 = –1 up-cut milling for pocket and
island)
n
Counterclockwise (Q9 = +1 climb milling for pocket
and island)
You can check the machining parameters during a program
interruption and overwrite them if required.
Example: NC block
N57 G120 CONTOUR DATA
Q1=-20
;MILLING DEPTH
Q2=1
;TOOL PATH OVERLAP
Q3=+0.2
;ALLOWANCE FOR SIDE
Q4=+0.1
;ALLOWANCE FOR FLOOR
Q5=+30
;SURFACE COORDINATE
Q6=2
;SET-UP CLEARANCE
Q7=+80
;CLEARANCE HEIGHT
Q8=0.5
;ROUNDING RADIUS
Q9=+1
;DIRECTION OF ROTATION
X
Y
k
Q9=+1
Q8
X
Z
Q6
Q7
Q1
Q10
Q5
Before programming, note the following:
Cycle G120 is DEF active which means that Cycle G120
becomes effective as soon as it is defined in the part
program.
The algebraic sign for the cycle parameter DEPTH
determines the working direction. If you program
DEPTH = 0, the TNC does not execute that next cycle.
The machining data entered in Cycle G120 are valid for
Cycles G121 to G124.
If you are using the SL Cycles in Q parameter programs,
the Cycle Parameters Q1 to Q19 cannot be used as
program parameters.