6 f u ll-surf ace mac h ining with turn plus – HEIDENHAIN SW 54843x-02 DIN Programming User Manual
Page 557
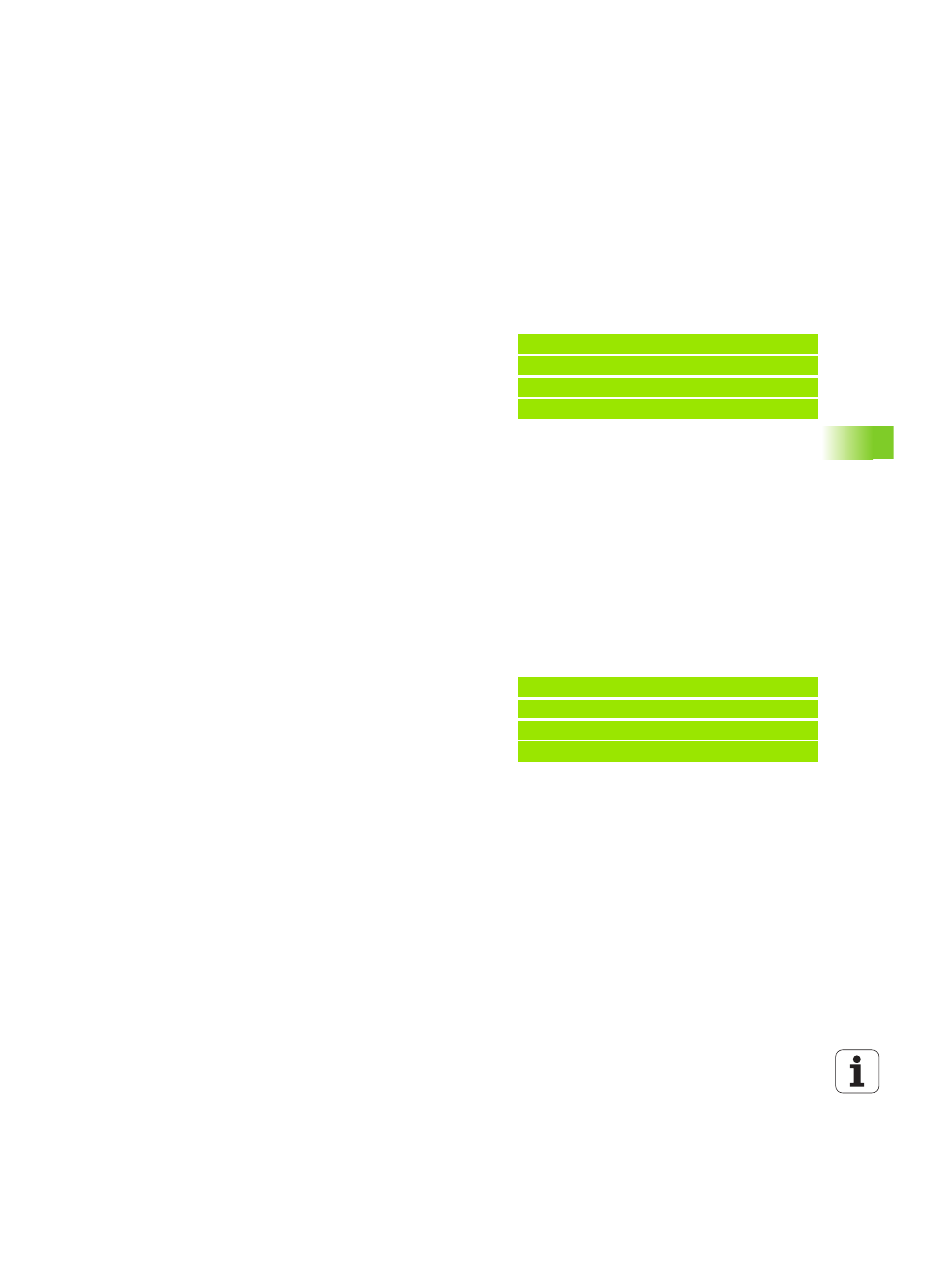
HEIDENHAIN MANUALplus 620, CNC PILOT 640
557
7.
6 F
u
ll-surf
ace mac
h
ining with TURN PLUS
Defining the chucking equipment for full-surface
machining
The full-surface machining sequence is defined in the chucking-
equipment dialog. You also define the zero points, pick-up position and
cutting limits in this dialog.
Example of first setup for full-surface machining:
Example of second setup for full-surface machining:
Example: Defining the first chucking equipment
. . .
CHUCKING EQUIPMENT 1
H0 D0 R0 J100 K15 X120 Q4 V0
. . .
Parameter
No. of clamping H
CHUCKING EQUIPMENT 1
No. of spindle AWG D
0: Main spindle
Clamp type R
0: External clamping or 1: Internal
clamping
Chuck edge Z
No entry (AWG uses the value from the
user parameters)
Chuck jaw reference B
No entry (AWG uses the value from the
user parameters)
Clamping length or free
length J
Enter the clamping length or free length
Cutting limit, outside O
Is calculated by AWG (if external
clamping is used)
Cutting limit, inside I
Is calculated by AWG (if internal
clamping is used)
Overlap K
Overlap jaw/workpiece
Clamping diameter X
Clamping diameter of workpiece blank
Chuck form Q
4: External or 5: Internal
Shaft machining V
Select the desired AWG strategy
Example: Defining the second chucking
equipment
. . .
CHUCKING EQUIPMENT 2
H0 D3 R1 J15 K-15 X68 Q4 V0
. . .
Parameter
No. of clamping H
CHUCKING EQUIPMENT 2
No. of spindle AWG D
0: Main spindle or 3: Opposing spindle
(depending on type of rechucking)
Clamp type R
0: External clamping or 1: Internal
clamping
Chuck edge Z
No entry (AWG uses the value from the
user parameters)
Chuck jaw reference B
No entry (AWG uses the value from the
user parameters)
Clamping length or free
length J
Enter the clamping length or free length
Cutting limit, outside O
Is calculated by AWG (if external
clamping is used)
Cutting limit, inside I
Is calculated by AWG (if internal
clamping is used)
Overlap K
Overlap jaw/workpiece
Clamping diameter X
Clamping diameter of workpiece blank
Chuck form Q
4: External or 5: Internal
Shaft machining V
Select the desired AWG strategy