Recessing g860, 1 7 cont our -based t u rn ing cy cles – HEIDENHAIN SW 54843x-02 DIN Programming User Manual
Page 273
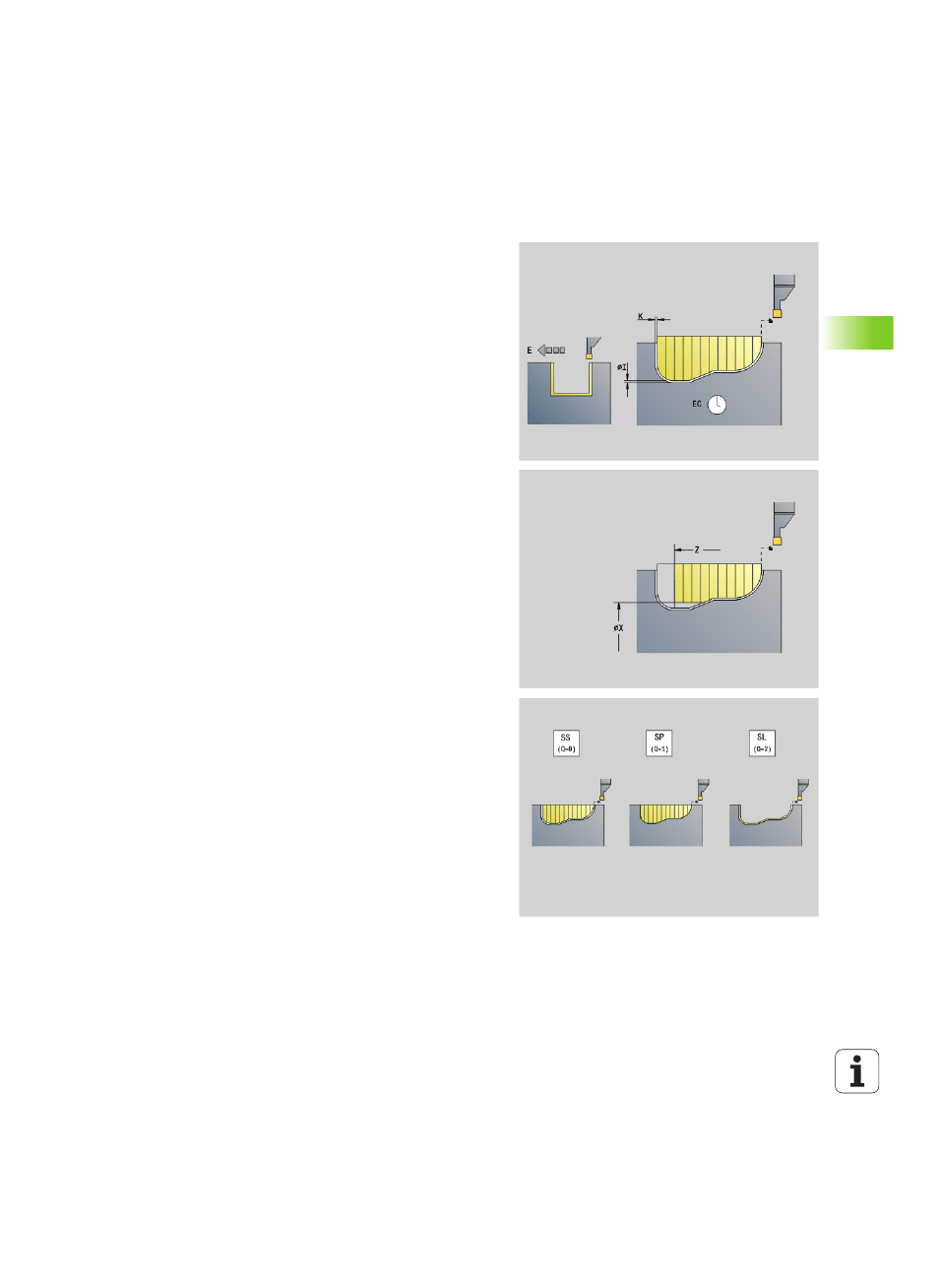
HEIDENHAIN MANUALplus 620, CNC PILOT 640
273
4.1
7
Cont
our
-based t
u
rn
ing cy
cles
Recessing G860
G860 machines the defined contour area. The reference to the
contour to be machined can be transferred in the cycle parameters, or
the contour can be defined directly after the cycle call (see "Working
with contour-based cycles" on page 260). The contour to be machined
can contain various valleys. If required, the area to be machined is
divided into several sections.
Parameters
ID
Auxiliary contour—ID number of the contour to be machined
NS
Start block number
Beginning of the contour section, or
Reference to a G22/G23-Geo recess
NE
End block number (end of contour section)
NE not programmed: The contour element NS is machined
in the direction of contour definition.
NS=NE programmed: The contour element NS is machined
opposite to the direction of contour definition.
NE is inapplicable if the contour is defined by G22/G23-Geo
I
Oversize in X direction (diameter value) – (default: 0)
K
Oversize in Z direction (default: 0)
Q
Action (default: 0)
0: Roughing and finishing
1: Only roughing
2: Only finishing
X
Cutting limit in X direction (diameter value) – (default: no
cutting limit)
Z
Cutting limit in Z direction (default: no cutting limit)
V
Identifier start/end (default: 0) A chamfer/rounding arc is
machined:
0: At beginning and end
1: At beginning
2: At end
3: No machining
E
Finishing feed rate (default: active feed rate)
EC
Dwell time