Modulo – BECKHOFF EL7037 User Manual
Page 149
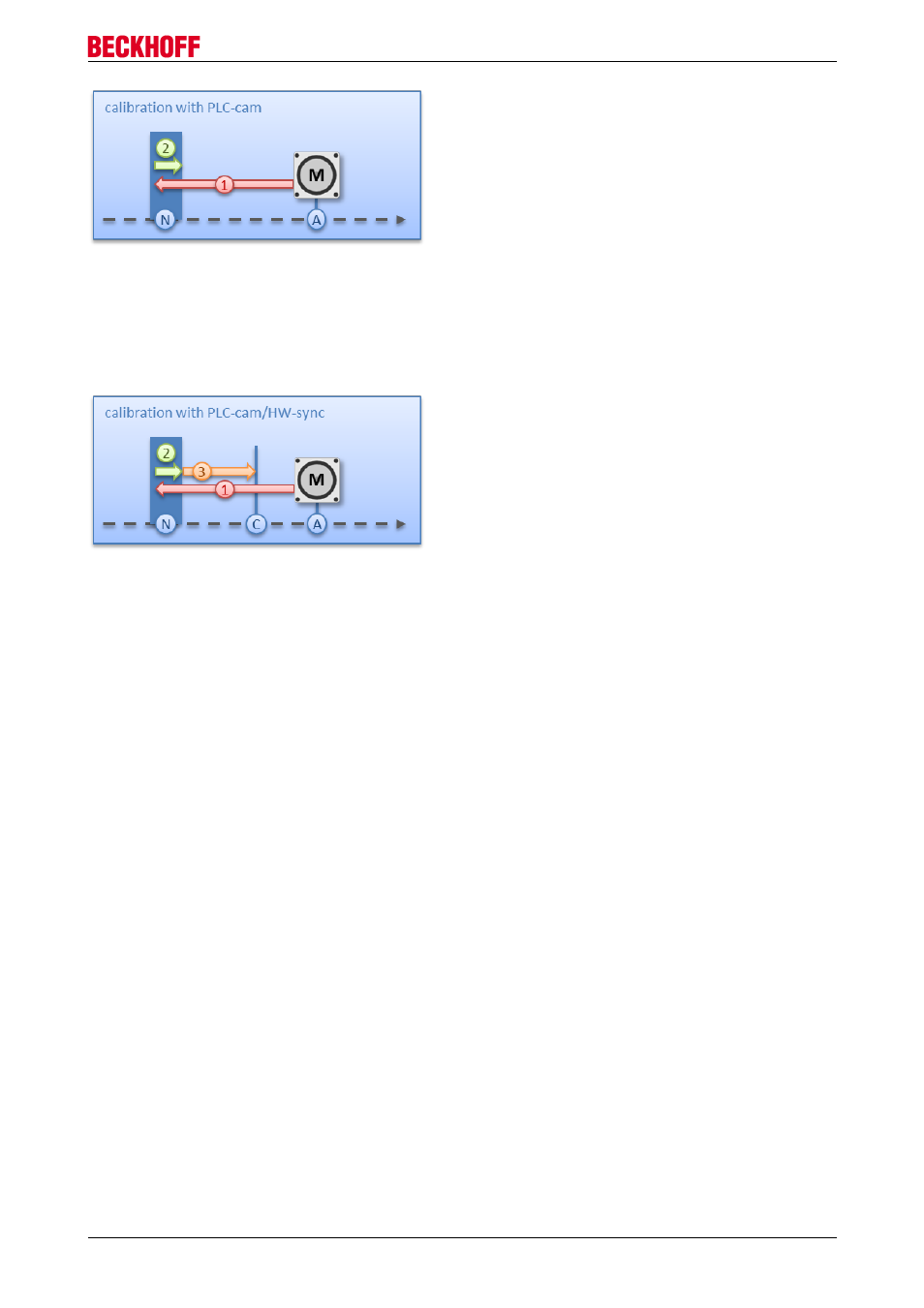
Commissioning
Fig. 171: Calibration with cam
For a more precise calibration, an HW sync pulse (C-track) is used in addition to the cam. This calibration
proceeds in exactly the same way as described above, up to the point at which the motor travels away from
the cam. The travel is not stopped immediately; instead, the sync pulse is awaited. Subsequently, the “In-
Target timeout” runs down again and the calibration position is taken on by the terminal as the current
position.
Fig. 172: Calibration with cam and C-track
If calibration by hardware is not possible due to the circumstances of the application, the user can also set
the “Calibrated” bit manually or automatically. The manual setting or deletion takes place with the commands
“SET_CALIBRATION” and “CLEAR_CALIBRATION”.
It is simpler, however, if the standard start types (Index 8021:01 [
184]) are set to
“SET_CALIBRATION_AUTO”. The “Calibrated” bit will now be set automatically by the first rising edge on
“Enable”. The command is conceived only for this purpose; therefore, it does not make sense to use it via
the synchronous data exchange.
MODULO:
The modulo position of the axis is a piece of additional information about the absolute axis position. Modulo
positioning represents the required target position in a different way. Contrary to the standard types of
positioning, the modulo positioning has several pitfalls, since the desired target position can be interpreted
differently.
The modulo positioning refers in principle to the "Modulo factor" (Index 8020:0E [
183]), which can be set in
the CoE. In the following examples, a rotary axis with a “Modulo factor” equivalent to 360 degrees is
assumed.
The “Modulo tolerance window” (Index 8020:0F [
183]) defines a position window around the current modulo
target position of the axis. The window width is twice the specified value (set position ± tolerance value). A
detailed description of the tolerance window is provided below.
The positioning of an axis is always referenced to its current actual position. The actual position of an axis is
normally the target position of the last travel command. Under certain circumstances (incorrect positioning
due to the axis stalling, or a very coarse resolution of the connected encoder), however, a position not
expected by the user may arise. If this possibility is not considered, subsequent positioning may lead to
unexpected behaviour.
EL70x7
149
Version 1.0