Delta MMC120 User Manual
Page 33
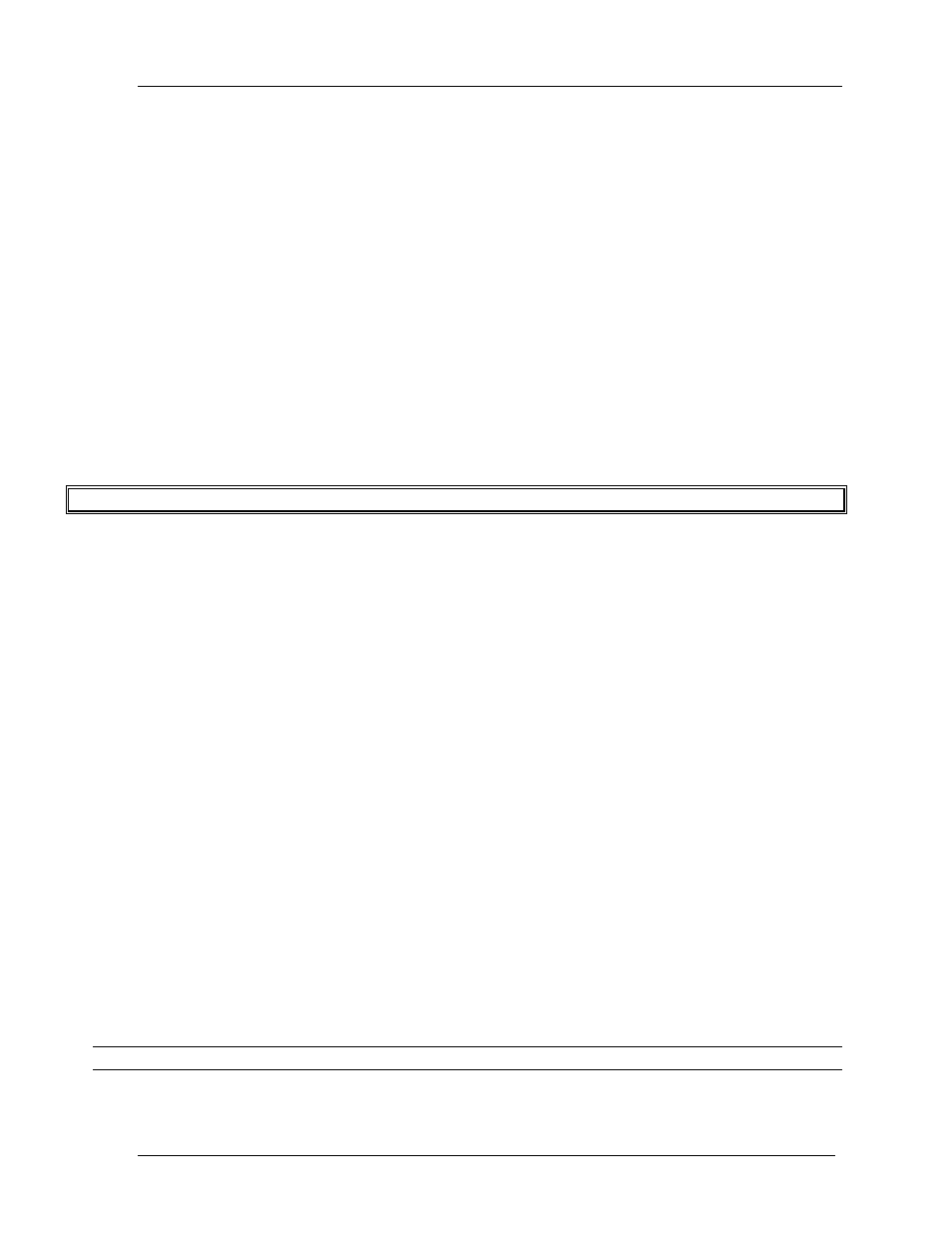
MMC120 Linear Motion Control Module
Motion Control Parameters
Delta Computer Systems, Inc. 360/254-8688
33
EXTEND ACCELERATION FEED FORWARD (Default: 0) Range: 0 to 65535
An axis will not respond to a change in the drive output until some time has passed. This causes the error
between the actual and target positions to be larger for axes that are moving large masses or have slow valves.
The MMC120 can help compensate for these factors by increasing the drive output. The increase in drive is
controlled by the value of this parameter, which has units of millivolts of drive per 100,000 position units per
second per second.
If the position unit is .001 inches, this equals millivolts of drive per 100 inches per second per second.
RETRACT ACCELERATION FEED FORWARD (Default: 0) Range: 0 to 65535
Same as EXTEND ACCELERATION FEED FORWARD, except it is used when retracting.
DEAD BAND ELIMINATOR (Default: 0)
Some valves and drives do not react to small changes in output around the null drive value; this effect is
termed "dead band". The DEAD BAND ELIMINATOR value is the number of millivolts added to or
subtracted from the drive output (depending on the direction of travel) so the drive output is outside the dead
band.
CAUTION: Do not make this value too large or the drive will oscillate.
IN POSITION (Default: 50)
IN POSITION specifies the size of a window around the COMMAND POSITION. When the ACTUAL
POSITION gets within this window, the In Position bit is set (but not latched) in the STATUS word.
For example, if an axis COMMAND POSITION is 10,000 and the IN POSITION parameter is 30, the In
Position bit will be set when the ACTUAL POSITION is between 9,971 and 10,029. The bit will be cleared
whenever the ACTUAL POSITION is outside the range. Note that if the IN POSITION parameter is 0 (zero),
the In Position bit will never be set.
FOLLOWING ERROR (Default: 250)
The FOLLOWING ERROR determines how large the difference between the TARGET POSITION and
ACTUAL POSITION can get before the Following Error bit is set in the STATUS word.
AUTO STOP (Default: 0FFE0 - Soft Stops enabled, Hard Stop enabled
for transducer errors)
Bits 1 through 8 in the AUTO STOP field have a one-to-one correspondence with bits 1 through 8 in the
STATUS word. The bits in this byte enable a Soft Stop whenever the corresponding error bit (1 through 8) is
set in the STATUS word. During a Soft Stop, the target speed ramps down to zero using the current
DECELERATION value. On startup these bits are all set, so any error will cause a Soft Stop. Bits 1, 2, and 3
(the transducer error bits) cannot be cleared. This means that a transducer error will always cause a Soft Stop,
and will cause a Hard Stop if bits 9, 10, or 11 are set. If a transducer error causes a Soft Stop then the axis
goes into open loop and ramps the drive output to null using the current open loop ramp rate.
NOTE: To input hexadecimal numbers using DCS120, enter a zero as the first character: 0FFFF
Bits 9 through 16 in the AUTO STOP field also have a one-to-one correspondence with bits 1 through 8 in the
STATUS word. The bits in this byte enable a Hard Stop whenever the corresponding error bit (1 through 8) is