Delta MMC120 User Manual
Page 15
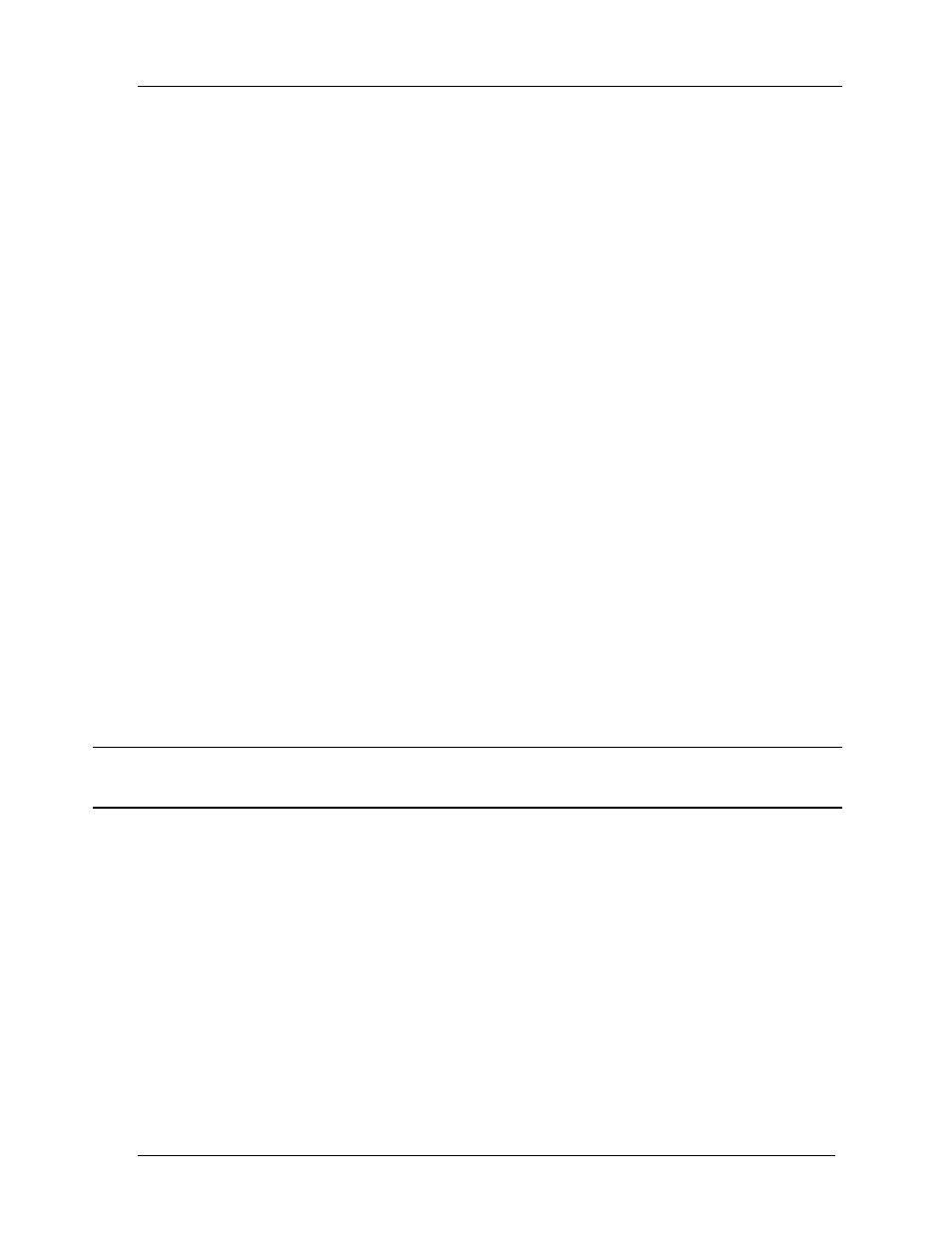
MMC120 Linear Motion Control Module
Description
Delta Computer Systems, Inc. 360/254-8688
15
In addition to the closed loop drive, the MMC120 has two feed forward terms, made up of EXTEND and
RETRACT FEED FORWARD, and EXTEND and RETRACT ACCELERATION FEED FORWARD. These
feed forward terms give approximately the drive needed to make the axis follow the target, freeing the PID
loop to correct for nonlinearity in the system and changes in system load.
Drive Output
The drive generated by the MMC120 is sent through optical isolation to a 12 bit digital-to-analog converter
(DAC). The output from the DAC is amplified to provide a ±10 volt output to the hydraulic valve. Servo
valves that need current input require a voltage-to-current converter (Delta part number VC2100).
Proportional valves work directly with the voltage signal.
Quantum Interface
The MMC120 communicates with the Quantum controller over the backplane. The module is I/O mapped as
a
DCS MMC 120 0x
with four input and four output registers. Commands and status for both axes are
transferred across the backplane in groups of four 16-bit words.
Programming
Commands to the MMC120 are sent by writing to the Programmable Controller's output registers. The first
two registers send commands to axis 1 while the next two registers send commands to axis 2. Programming
details are presented in the section "COMMUNICATING WITH THE MMC120."
Event Control
Sequences of commands can be stored and executed by the MMC120 with little intervention by the
Programmable Controller. This allows a 1 millisecond response time by the MMC120 to internal events such
as move done or elapsed time.
FLASH Memory
You can store parameters, profiles, and Event Control steps in the MMC120's non-volatile FLASH Memory.
This reduces the memory requirements in the Programmable Controller and eliminates the need to transfer
initialization parameters back and forth.
NOTE: Since data is stored in the module, when you replace one module with another you must transfer the
parameters and profiles to the new module . Because of this, you must store all parameters and profiles
either in the ladder logic program or in a DCS120 file so they can be transferred to a module when needed.