Motion control parameters, Initialization parameters – Delta MMC120 User Manual
Page 27
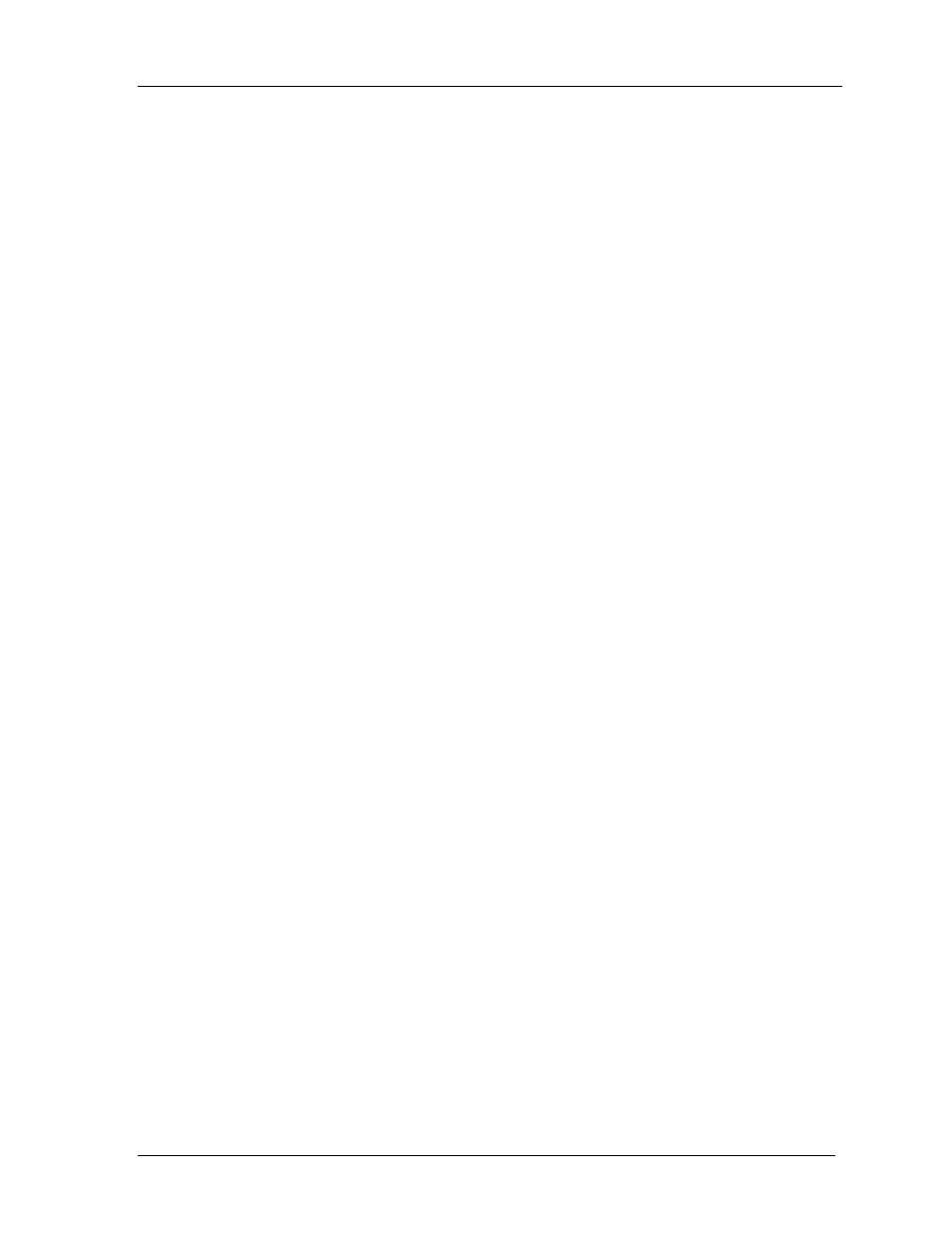
MMC120 Linear Motion Control Module
Motion Control Parameters
Delta Computer Systems, Inc. 360/254-8688
27
MOTION CONTROL PARAMETERS
Sixteen Parameter registers and 6 Command registers control the operation of the MMC120. The status of the
module is shown in 10 internal Readback registers. Manipulating the contents of the Parameter and
Command registers is key to the successful application of the MMC120.
Delta's DCS120 program (included with the module) gives you direct access to all the internal registers. This
is helpful for setup and debugging.
The chapter 'Communicating With The MMC120' describes how the Quantum Programmable Controller gains
access to the internal registers of the MMC120. This chapter describes these internal registers.
Initialization Parameters
CONFIGURATION Word (Default: 0000)
Eleven bits of this 16-bit word control the configuration of the module. Bit 16 is the LSB; bit 1 is the MSB.
Bits 1 - 4 - Transducer Type bits
Set these bits all to 0 if the transducer is start-stop. If the transducer is gated, set the bits so the value of these
four bits equals the number of recirculations the gated transducer is set to (bit 1 = 8, bit 2 = 4, bit 3 = 2, and bit
4 = 1). For example, if the transducer is set to one recirculation, bit 4 should be set. If the transducer is set to
10 recirculations, bits 1 and 3 should be set, and if it is set for 15 recirculations, all four bits should be set to 1.
When a transducer is set for multiple recirculations, there is a small time delay between those recirculations.
During this time the counter on the MMC120 continues to count, resulting in about 2700 extra counts per
recirculation which are added to the transducer count. These extra counts create an offset; to correct this offset
the module calculates the extra counts based on the number of transducer recirculations and subtracts them
from the transducer count. If the value of these bits and the transducer recirculations agree, the transducer
count should be slightly positive when the transducer is at its minimum position. If your minimum position
count is negative, reduce the setting of these bits until the count is slightly positive.
If you are using a gated transducer and want resolution better than 0.001 inches, we suggest using 10
recirculations and setting bits 1 and 3. This will give 0.0001 inch resolution with a stroke of about 6.5 inches.
Bit 10 - Reverse Drive Mode bit
When this bit is set the polarity of the axis’ output voltage is reversed. This bit is useful when you are
connected to two drives which do not have differential or isolated inputs, and you need one to extend with
positive drive and the other to extend with negative drive. (If the drives have differential or isolated inputs,
you can just reverse the connections to the drive that must extend with negative drive.) When this bit is set,
transducer counts will DECREASE with positive drive and the displayed drive will be the opposite of what is
output by the module (a positive display will output a negative voltage).
Bit 11 - Absolute Mode bit
This mode is intended for use with a two-valve system, one controlling the flow rate and the other the
direction. This axis controls the flow rate valve. The directional valve must be controlled by other means. In
this mode, the axis generates a positive drive output regardless of the direction of the move. The drive will not