Part 1 the revolving field ac generator – Generac Power Systems 53187 User Manual
Page 44
Attention! The text in this document has been recognized automatically. To view the original document, you can use the "Original mode".
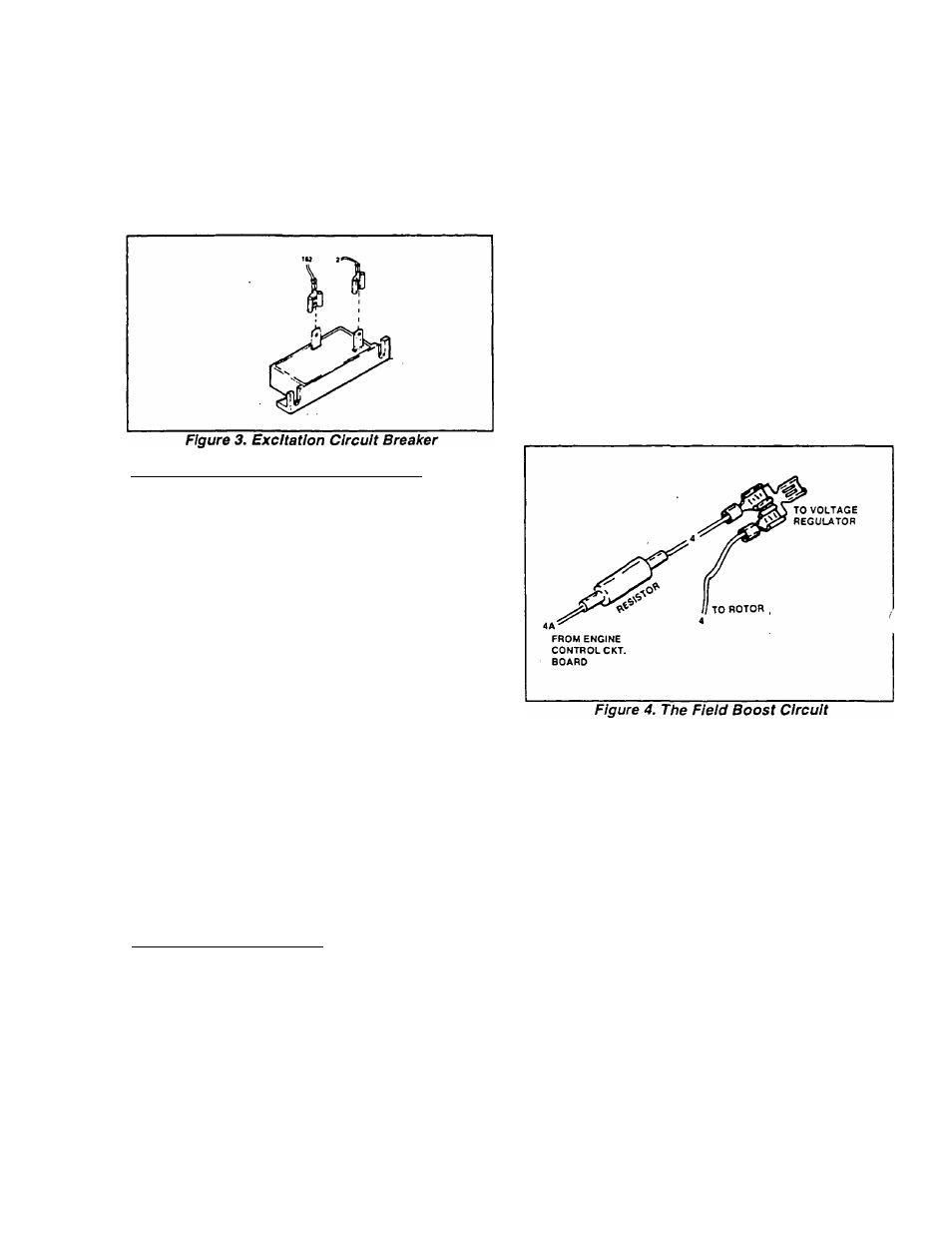
SECTION 1.7- TROUBLESHOOTING
(UNITS WITH 10 INCH STATOR)
1
PART 1
THE REVOLVING FIELD AC GENERATOR
Diagnostic Tests (Continued)
Results:
1. Replace excitation circuit breaker if it fails the test.
2. If the circuit breaker tests good, go on to Test 7.
TEST 7- TEST STATOR EXCITATION W INDING:
Discussion: An open or shorted stator excitation
w inding can seriously affect the generator’s AC output.
For exam ple, an open condition w ill result in loss of loss
of excitation AC output to the Regulator. Excitation
current flow to the Rotor w ill then drop to zero and
generator AC output voltage w ill drop to a value com
m ensurate w ith residual m agnetism plus field boost.
Procedure: Refer to Test 5. A VOM, connected
across W ires No. 5 and 6, should read the resistance
of the stator excitation w inding (about 1.00 ohm ). A
reading of "infinity" indicates an open w inding. A very
low reading indicates a possible shorted condition. To
test for a GROUNDED condition, proceed as follow s:
1. Set a VOM to a very high resistance scale, such
as “Rx10,000" or “Rxl K". Zero the m eter.
2. Connect one VOM test probe to stator lead No.
5; connect the other test probe to a clean fram e ground
on the stator. The m eter should read "infinity". Any
reading other than "infinity" indicates a grounded con
dition.
Results:
1. If excitation w inding is open, shorted or
grounded, replace the stator assem bly.
2. If excitation w inding checks good, go to Test 8.
TEST 8- CHECK FIELD BOOST:
Discussion: Approxim ately 4 to 8 volts output from
the stator excitation w inding is required to turn the
Voltage Regulator on. The field boost feature delivers
additional current to the Rotor during engine cranking.
The additional field boost current creates a Rotor m ag
netic field strength that is additive to the Rotor’s resid
ual m agnetism . The end result of field boost is an early
"pickup" voltage to build induced voltage into the stator
w indings early during startup.
It is norm al for som e residual m agnetism to be
present in the Rotor at all tim es. This residual m agne
tism can be lost under certain conditions. If Rotor
residual m agnetism has been lost, it w ill norm ally be
restored by field boost current during engine cranking.
How ever, if Rotor residual m agnetism has been lost
AND field boost does not "flash the field" during crank
ing, sufficient voltage to turn the Regulator on m ay not
be developed. Loss of residual m agnetism accom pa
nied by loss of field boost current w ill likely result in a
reduction of generator AC output to zero volts.
Reid boost current Is alw ays available to the Rotor
w hen the engine is running, by the action of an endne
control circuit board housed in the control panel. Bat
tery voltage is delivered to the Rotor via Term inal 8 of
that circuit board. W ire 4A, field boost resistor, and W ire
4.
Procedure: To test the field boost function, pro
ceed as follow s:
1. Disconnect W ires No. 4 from the Voltage Regulator.
This is a "piggy-back" term inal w ith one W ire No. 4
routed to the brushes and one W ire No. 4 com ing from
the engine control circuit board. The latter w ire, w ith
in-line resistor, is the field boost circuit.
2. Connect a DC voltm eter across the term inal end of
W ire No. 4 at the Voltage Regulator and Term inal 2 of
the engine control circuit board (to w hich W ires No. 0
[ground] connect).
3. Crank the engine. During cranking, the m eter should
read approxim ately 9-10 volts DC, indicating that field
boost voltage is available.
a. If field boost voltage is indicated, end the test and
go to Test 9.
b. If voltage is NOT indicated, go to Step 4.
4. Connect the DC voltm eter across Term inal 8 (W ire
No. 4A) of the engine control circuit board and Term inal
2 (W ire No. 0) of the circuit board. Crank engine and
m eter should read battery voltage (about 12-13 volts
DC).
PAGE 1.7-6